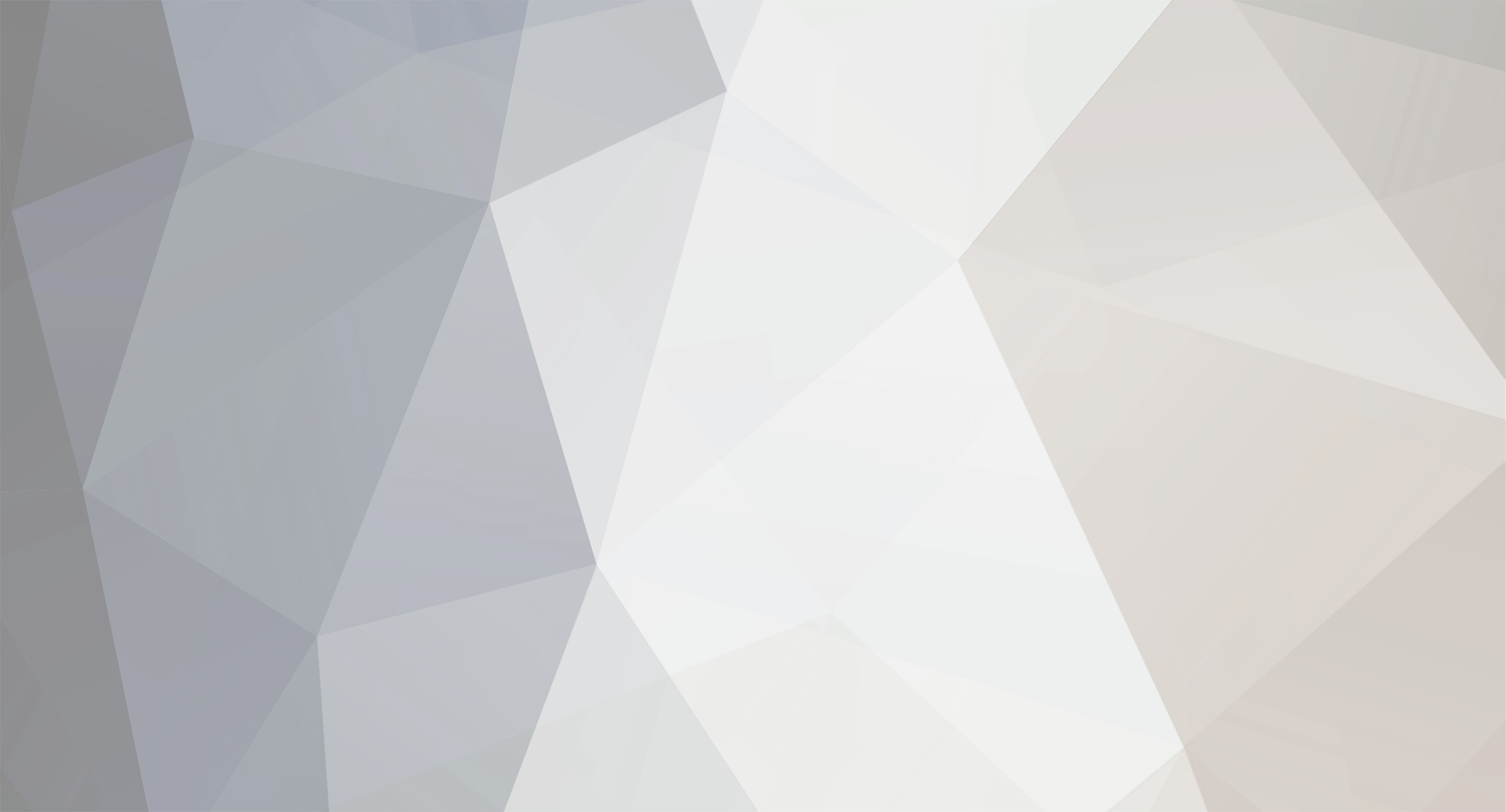
Rayhan
Gold Tier-
Posts
117 -
Joined
-
Last visited
-
Days Won
4
Content Type
Profiles
Forums
Events
Store
Downloads
Gallery
Everything posted by Rayhan
-
There is nothing to say this wasn't created by the smith especially for a Sa smith. I think study is required by everyone on this thread, myself included.
-
What is the soul of your collection ?
Rayhan replied to Benjamin's topic in General Nihonto Related Discussion
The soul of my collection are the memories associated with each sword. From the first sword, the journey that brought me to it. To the people involved, the good memories and the bad, the best lessons and the worst (which are actually the most essential) to the friends and loved ones now part of those memories. -
I am only inclined to recommend swords that have (or can paper up) and these generally are higher priced. But in the end people will buy what they like and this is also ok, we cannot detract from the "itch" but I hope people will do justice to their bank accounts as well as their desires.
-
Sorry but I've seen very good ones go for 3500. 5 to 6 k USD is a good starting budget if you just want a sword to study. It gets tricky when you start to specialise though, then you're right @Bosco, it's more expensive when we spec our desired sword.
-
Let us know what you find
-
There are quite a few people with connections in Japan to swordsmiths who could tell us how this is achieved and polishers who are also knowledgeable. Perhaps we can ask them? Also, there is plenty of historical text on the subject but in Japanese. I will ask a few connections in Japan for insights and hopefully others here can do the same?
-
DTI has a few wonders close to or over 1m USD and the most expensive Japanese Sword i have seen sell was the Sanchomo for 5m USD not to mention the recent Sotheby's sale Mikazuki Kanemitsu https://www.sothebys.com/en/digital-catalogues/crescent-moon-the-mikazuki-kanemitsu-from-the-paul-l-davidson-collection which I'm sure was priced quite high. Not an open auction but still publicly advertised so you could apply to be included.
-
Some of the Kiyomaro in this exhibit really had a presence, huge energy. The Masahide, especially with the exquisite horimono are sublime.
-
This exhibit was really impressive, where are the pics of Kiyomaro?
-
Learned something there! Thank you @Franco. So it's akin to tachi, nagamaki is about the koshirae and less the suguta of the blade? So Jussi pinned it as Nagato which is the right terminology?
-
I would like to take a moment to apologise to the JSSUS for not verifying and doing my research properly before posting one of their magazines (taken down long ago). If I had been more clinical I would have found this link https://www.jssus.org/Japanese_Sword_Society_Archive.html That has a full host of valuble materials and made available for free. Ladies and gentlemen of the JSSUS please forgive my oversight and arrogance. And for those students please check the link to see great material for beginners and seasoned collectors alike. Rayhan
-
- 7
-
-
-
People generally get very annoyed at me for saying this but you should ideally aim for a 5k USD budget and higher for your first sword. Even tradionally made gendaito are pushing 3500 USD these days. I think the collecting guide by Kiril puts things in good perspective.
-
Dropping an interesting old text for everyone to download and read. Before the copyright police jump on me, this book is free to download from JSTOR as well and was published first in 1905. Light reading for fun. Not sure if it is in the downloads section already? The Japanese Book of the Ancient Sword.pdf
-
- 7
-
-
-
-
Art of the Samurai for download
Rayhan replied to Rayhan's topic in General Nihonto Related Discussion
To have seen this in person must have been such an honour. It is a great book to go through and we are all lucky it is so freely available. -
https://www.samurai-nippon.net/SHOP/V-2061.html
-
@Jacques sir I do love this this thread but now we're pushing into obscurity. It is absolutely obvious how we can tell. Firstly where the tang of a Naginata meets its hamachi and munemachi is different to an intentional made, exaggerated, katana of Naginata Naoshi shape. The other differential is when we observe the jigane in areas that have been altered and hamon in areas altered (cut/ground down) and again historical records of swords that have had the process conducted. @Jacques we need data to get into this and that isnt available here. @everyone else start looking deeper i guess, I'm sure our books have answers
-
There is a lot of speculation in answering how core steel is addressed but I would think that was taken into consideration before they proceeded with the changing of the blade. Kamakura boshi on Naginata were not even and precise in most cases and then there is always the possibility of saiha on the reshaped area, way too much speculation i think.
-
I think Shinsakuto are very important aspects of Bushido today and still at the heart of Japanese culture. If you take example from Gassan school this is still the longest running school and has an unbroken 800 year history. Tsunahiro school is still in operation in Japan also so there is no copying there is still a strong legacy in Shinsakuto and if possible we should support them. If you practice Iaido or Kendo and have achieved a high level then having a Shinsakuto is also very important and a life achievement. In short, they are still grand examples of Nihonto history. Which school or smith is making your sword?
-
Whoa a Bungo thread! I do appreciate a good Bungo sword and can share the below examples for viewing pleasure. Takada is correct. If you want better resolution please download the images and open them in your gallery viewer. The Muneyuki is in a very interesting Hitatsura Bungo Tomoyuki Zufu.pdf Takada Muneyuki Sayagaki.pdf Takada Muneyuki Tokubetsu Hozon.pdf
-
I take example from you and Darcy and @Brano who are always sharing information, @Jussi Ekholm who is always lending help where he can and so many other friends i have met in this community. @Brian who keeps everything going and keeps himself going even though it must be so stressful dealing with characters like me everyone who shares information and takes time to meet up or organise meetings, kudos to all of you.
-
Lastly there is this Enju. It shows the progress from Hozon to Juyo. I hope the work of Markus and the sharing of these Zufu will help who ever comes across them and answer some of the questions collectors may have about their own swords and fittings. I only wish there was more we could share with all. Enju Hozon.pdf Enju Juyo Paper.pdf Enju Juyo Zufu.pdf Enju sayagaki.pdf