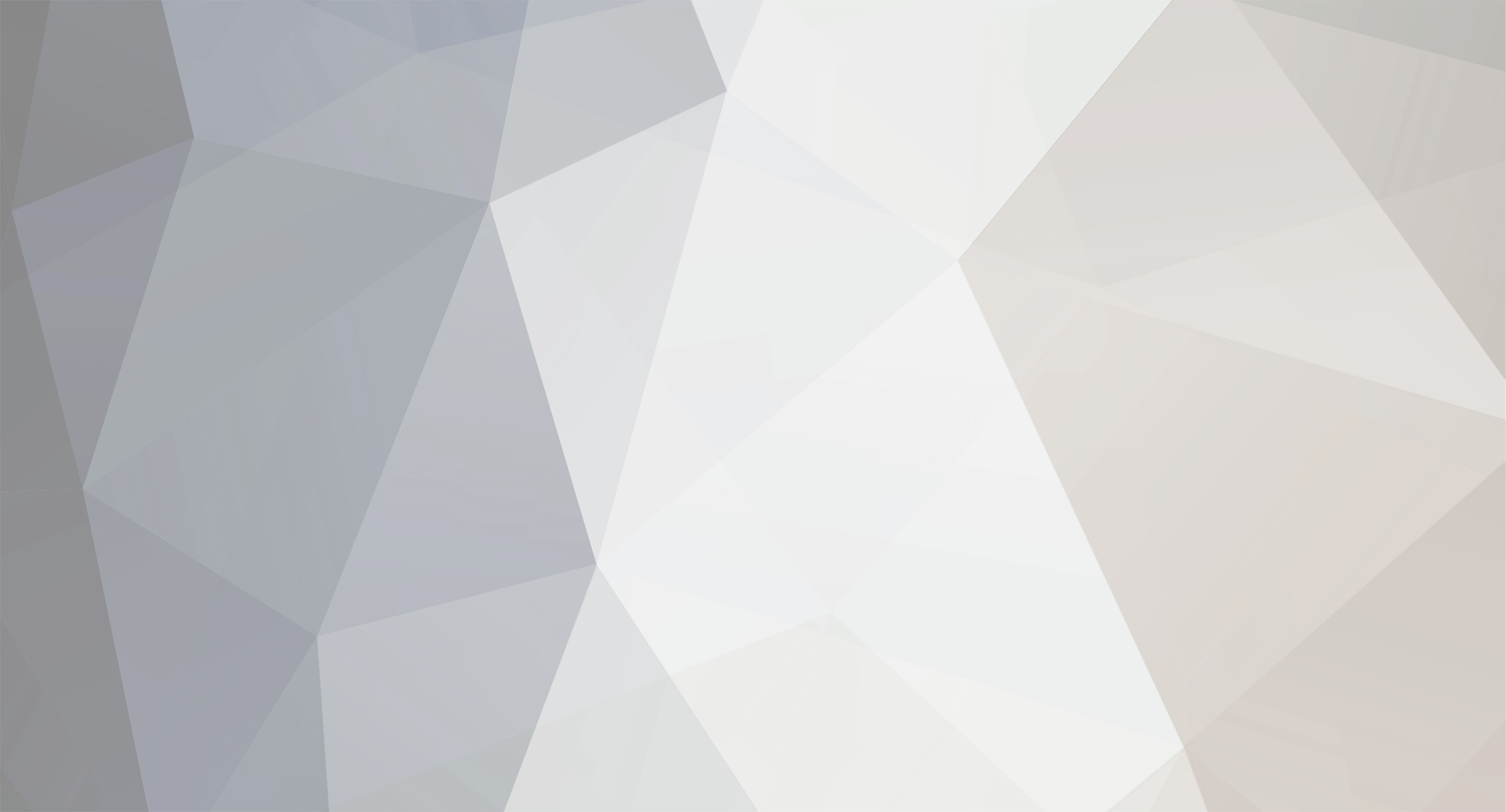
Rayhan
Members-
Posts
22 -
Joined
-
Last visited
Profile Information
-
Gender
Male
-
Location:
Singapore
Profile Fields
-
Name
Rayhan
Recent Profile Visitors
The recent visitors block is disabled and is not being shown to other users.
Rayhan's Achievements
-
Any investment in an art form like Nihonto needs to be carefully considered. You cannot simply buy this and that Rai and assume monetary value... Why not study Rai Kuniyuki a bit more and then see? The future buyers will study and see also...
-
Totally agree. But it's really important to see than to feel
-
How accurate is this certificate ?
Rayhan replied to Bosco's topic in General Nihonto Related Discussion
Allow me to impart a story of Hamon suffocated by hadori. A few years ago 2016, I was in Osaka and went to see a Hirotsugu sword. The sword was clearly Hitatsura and had been polished badly and was presented in suffocating Hadori...oh my I bought the sword, no papers. The sword was sent to a very good polisher to be done in sashikomi polish. After that it went from Hozon - THozon in the same sitting on to Juyo 2 years later. Hirotsugu Juyo is rare. If you study the sword, feel it has the suguta you think is correct and strong, etc then go with your gut and try. If you have even a single doubt, don't regret. -
Bizen Saburo Kunimune is one of the Soshu zero group, the founding pillars of Soshu Den, he would have a place in any one sword collection and the owner would be proud. There is a funny aspect with Saburo Kunimune swords as many (in the context of known and documented swords of Kunimune) are existing with signatures, however there are very few TJ and above. Owning one regardless is a definative moment for any collector looking for high end Kamakura. This sword though has a faded signature of sorts, hard to discern. It looks like first generation signature, remember there is a 2nd generation that signed with 5 characters. The second generation did more sugu style based hamon. Shodai Kunimune did subtle Bizen hamon before Kamakura and more flamboyant gunome based hamon after (during). The utsuri seems very forced by the polisher and interrupts more than exemplifies this smiths work. The bohi is later placement (open to opinions here). On the Rai, I also feel that this is in the wrong polish. It looks a tired sort but in both cases they are signed works so that is a definative point. With Rai you want Hamon to study, because Rai hada is interesting but Kuniyuki has such wealth in his hamon. I think in my personal opinion, if you want to spend this amount of money you should be willing to wait and find swords that really define these smiths in their pinacle works. All artisans and manufacturers have pinacle moments that command such prices so seek that moment in their work and don't settle for less.
-
It could also be the way steel or tamahagane was manufactured. Higher temperatures in smelting removing more impure areas and giving smiths a more uniform raw material. I also suspect, like everything in Japan, that these process was standardised in the later years after the Muromachi when iron distribution within Japan was quite tightly controlled.
-
I think the article on iron distribution clearly states that initially there were scattered tatara being used for iron production, which then moved to a combination of imported iron from China and Korea no doubt, then as tatara technology increased (tenpin bellows) we have a more self sufficient local supply by the edo period and finally a whole opening up of the iron trade with even European iron coming in. That's in a condensed version. It stated that the Chugoku region still maintained heavy iron sand production through the 1000 year span. That is summary. I think technological changes in tatara also should be taken into account. Trade didn't stop completely in the edo period, it was just very selective on who and what was allowed into Japan and from which regions.
-
So if we add Ko-Hoki to the list we see early schools: Ko-Hoki, Ko-Bizen, Ko-Ichimonji, Yamashiro, Aoe and even Bungo that have Utsuri in some capacity. Is it not plausible to then say that if this feature was initially an accident it very soon became a consistent feature and part of the manufacturing process during Heian into Nanbokucho and slightly beyond? The steel that was made in these regions via Tatara (not the in house steels mos likely made by earlier shops) was distributed across the region and perhaps these smiths who worked in various methods had certain agreement on foundational procedure given the cross of the same raw material. How to fundamentally prepare this steel for sword making ? Perhaps the heat treatment that leads to utsuri is there because this was a tried and tested procedure for iron sands in this region? The exact history of steel distribution from in-house manufacturers in Heian to Tatara in Heian and after is known but that knowledge is with Paul Martin (from an English perspective) unless there is another member who has studied the distribution of raw iron sand and mass production of tamahagane in the medieval Japan? What is clear is that the Hoki and Bizen regions were epicentre locations for iron sand and the composition is quite similar.
-
Thanks for chiming in all! @Gakusee allow me to correct my terminology, when I say low quality steel i simply meant the initial raw material from the furnace/tatara before it is put through the refining stages of manufacture. It is low quality in this context only and not as a whole. I am sorry, i know that Bizen blades are some of the finest and I have a deep love for them as well. @Jacques awesome list and thank you for this. It is most helpful for looking at which schools produced utsuri and their relevant locations across Japan and in what eras. Most appreciated.
-
Oh my, so much time has passed and no input from the more knowledgeable. Perhaps it is my oni spirit causing commotion... Anyway, utsuri in general falls to the Bizen tradition and the Yamashiro. Both schools show very distinguished traces of utsuri. We know that Bizen and Yamashiro forged in heats that were low in the context of Nihonto. We know that the sword smiths in the Heian/ Kamakura produced their own raw material and indeed followed the river systems in Bitchu, Bizen etc to produce tamahagane. Later this moved further north and spread across Japan. And so Utsuri might be a sign of lower quality steel being refined to a huge milestone. Interesting is it not, that these two schools came together to make soshu. Forging at such high heats that impure remnants are left behind. Also an interesting note is that by the time soshu came round we had tatara making much higher grades of raw material. Perhaps @Brano @Jussi Ekholm @Gakusee you might have some data? Sorry to call you out.
-
So we have some very nice images being shared and this is the main way we can study online, with shared images or video. There are other members being silent but who have access to great data to help this query. Perhaps if the more knowledgeable that have access to data could summarise which swords in the juyo and tokuju registry have been noted to show Utsuri and in what form we could break this up into era, utsuri type, frequency, etc. Much to be learned from the study of zufu and its contents as well as how they (the NBTHK) phrase the presence of utsuri on a sword. From my perspective the presence of utsuri denotes excellent and consistent heat treatment of steel and the uniformity in that particular area of the steel. Because it is a sign of excellent thermocycling and consistent practices that leads to uniform steel fit for purpose. Especially when dealing with raw materials such as forge made or tatara made Tamahagane. This raw material, although beautiful to behold, is not a forgiving medium and comes with it's own challenges when striving for "good sword steel ".
-
Modern steel does not require the process that producess Utsuri as stated in my previous post.
-
Im getting on my flight. Gents and ladies please think how these process(s) relate tonthe creation of a blade over weeks and months and not from hours or minutes. Sayonara. Ps: for those in Japan now the NBTHK is showing Kiyomaro (excellent examples and not so excellent but all Juyo) it is good to see what experts mean when they say excellent Kiyomaro and not so excellent. Masahide and Naotane also. The Tokyo National Museum is showing Soshu and Bizen (also Bitchu) in all it's glory, go see. Not to mention the other sword specific museums in Nagoya and such.
-
This is now an amazing example, what we should be wishing to see here is how the clay was placed in various intervals of heating. If only we had that time machine Darcy spoke of so often
-
So, back to this. @Rivkinthermocycling yes. Please stop putting the cart before the horse. We do not need to speak of Yaki-ire at all when we speak of Utsuri. The development of a blade has its stages and if the smith uses thermocycling (annealing is a process that is involved also but not mutually exclusive) https://knifesteelnerds.com/2021/08/28/how-to-thermal-cycle-knife-steel/ I know knife steel nerds is not a scientific journal but this article helps. If we imagine the process where we are changing the structure of the steel as we go along all the way till Yaki-ire then we can build the visual base for utsuri. @C0Di am not fortunate enough to see Utsuri being produced in real life today, being produced infront of my eyes to say, however, if you have this information please share it here so we can all benefit. I can say that i have an Ichimonji blade and Aoe that both have wonderful Utsuri and will share that when i am close to them again after my travels.
-