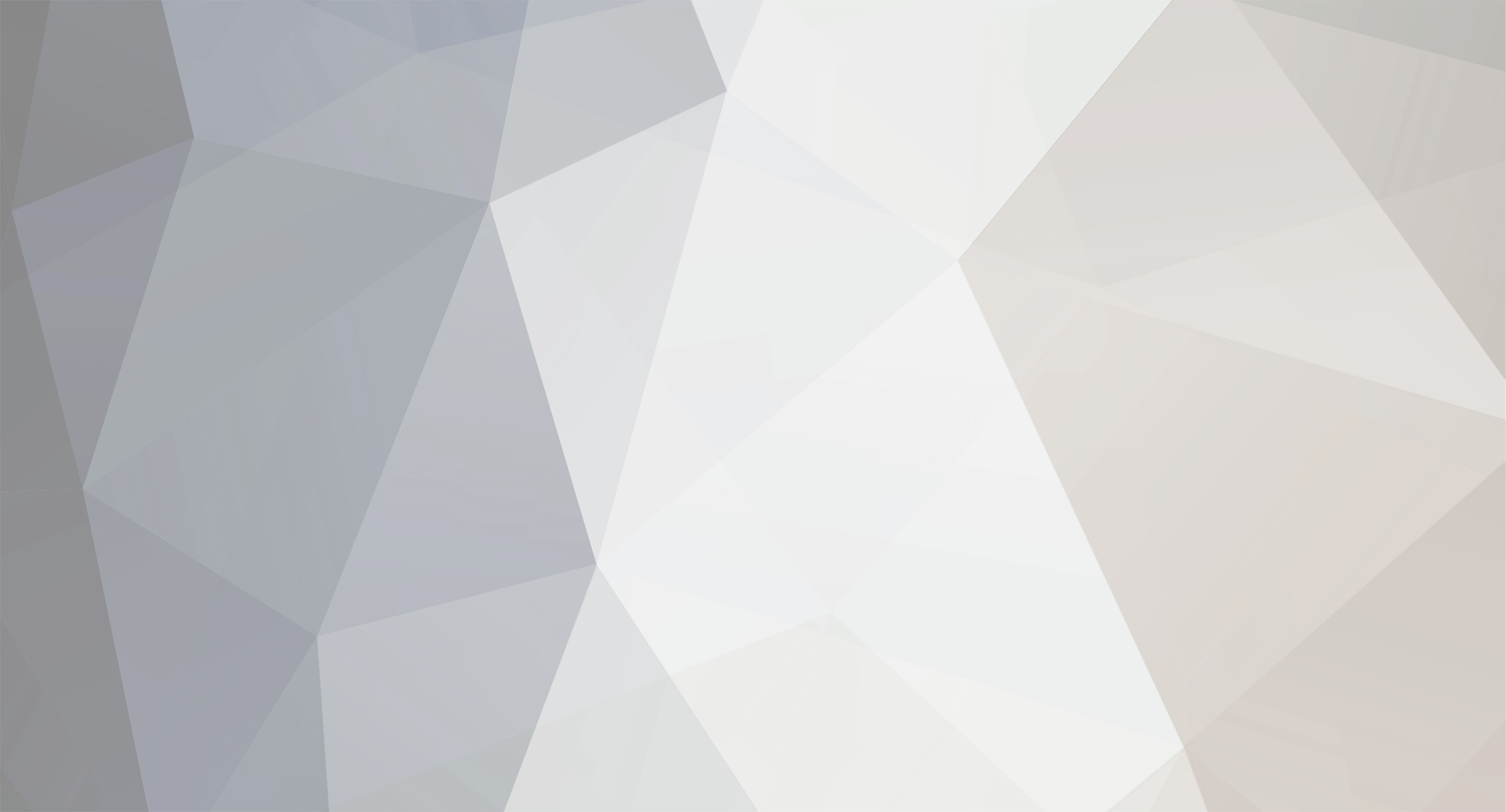
Mustafa Umut Sarac
Members-
Posts
22 -
Joined
-
Last visited
Contact Methods
-
Website URL
www.archive.org, www.academia.edu
Profile Information
-
Gender
Male
-
Location:
Istanbul
-
Interests
Archaeology of Future and Past
Profile Fields
-
Name
Mustafa Umut Sarac
Recent Profile Visitors
The recent visitors block is disabled and is not being shown to other users.
Mustafa Umut Sarac's Achievements
-
Thought of new idea, electroforming of swords and knives
Mustafa Umut Sarac replied to Mustafa Umut Sarac's topic in Nihonto
I know enough people around the world and everyday I recieve e mails from argentina to turkmenistan. I shared an important idea , judge from there. -
Thought of new idea, electroforming of swords and knives
Mustafa Umut Sarac replied to Mustafa Umut Sarac's topic in Nihonto
I am an archaeologist and know the history stuff better than you Brian , today is futures archaeology plus there is a branch as archaeology of future , my sister is an professor about it. If you want to masturbate how you are intelligent and intellectual because you know the past of something , you can do it but I will make my way at future not at the past of Japanese sword like simple stuff. Brian , play chess , it improves your IQ in next 30 years , I think you need to play to reach my level. I gave my 10 minutes to train you. If you want to want to be trained more , I will give randez vous to 30 years later , start chess and think like chess.- 31 replies
-
- 16
-
-
-
-
I have a new idea in my mind shaped in long time. As you know electroforming is in use at worldwide to craft bronze sculptures . And US and world banknotes copied from the master engraving with electroforming to print large amount of money. I dont know whether steel could be electroformed and with desired crystal structure or say phase. But if we can do it , we can electroform - not only 7 layers in Japanese swords - but hundreds of different layers, different metals, different microstructures , may be for example tungsten at the hard edge or chrome hamon , or whatever you imagine. Electroforming is a way to cathode anode transfer of metals within liquid and with the help of electricity. This idea is copyrighted worldwide and others can not patent the ideas here. Mustafa Umut Sarac Istanbul mustafaumutsarac@gmail.com
-
Hello David, I found him at facebook , Japanese scissors guy , I did not see better than his trade. I will write him. Thank you very much.
-
https://en.wikipedia.org/wiki/Jian Jian Chinese Sword Link with Image https://en.wikipedia.../Dao_(Chinese_sword) Double Crescent Sword Kung Fu Video Link
-
Below is a list of notable Chinese steel swords—with approximate historical periods and brief descriptions—that highlight the evolution of Chinese sword-making and metallurgy: 1. Early Jian (Straight, Double-Edged Swords) Time Period: Zhou Dynasty (c. 1046–256 BCE) to Warring States Period (475–221 BCE) Description: These are among the earliest known Chinese steel swords. Characterized by a straight, double-edged blade, they served as both weapons and status symbols. Their design laid the foundation for later refined versions used by scholars and warriors. 2. Han Dynasty Jian Time Period: Han Dynasty (202 BCE–220 CE) Description: With improved steel-making techniques, these jian became more balanced and elegantly designed. They are noted for their finer craftsmanship and are often seen as the archetypal “gentleman’s sword.” 3. Early Dao (Curved, Single-Edged Swords) Time Period: Transitioning from the late Warring States into the Han Dynasty Description: Evolving from the straight sword, early dao featured a single-edged, slightly curved blade. These were popular among soldiers for their ease of use in slashing motions. 4. Zhanmadao (Horse-Cutting Sword) Time Period: Prominently used during the Sui–Tang dynasties (6th–10th CE) Description: A long, heavy sword designed specifically to counter cavalry, with a length and curvature suited for cutting down horses. Its design reflects the tactical demands of mounted warfare. 5. Liuyedao (Willow-Leaf Sword) Time Period: Song Dynasty (960–1279 CE) Description: Renowned for its gracefully curved “willow leaf” profile, which offers both elegance and excellent cutting ability. This sword is celebrated for its balance and the high quality of its steel, embodying refined craftsmanship. 6. Changdao (Long Sword) Time Period: Appearing in various forms throughout Chinese history Description: The term “changdao” (literally “long sword”) generally refers to longer blades, often used with two hands for increased reach and power. Their designs varied by region and period, reflecting both martial needs and evolving metallurgical practices. 7. Legendary and Folkloric Swords Fangtianjian (Square-Heaven Sword): Time Period: More mythological than historically verified, this sword appears in legends and literature. Description: Often associated with divine justice and heroic figures, it symbolizes the ideal of righteous power in Chinese folklore. Guan Dao (Green Dragon Crescent Blade): Time Period: Popularized during the Three Kingdoms period (220–280 CE) and later romanticized in literature Description: Although technically a polearm due to its long haft, the guan dao’s design and legendary status (famously wielded by the general Guan Yu) have made it one of the most iconic “sword-like” weapons in Chinese martial lore. Metallurgy & Quality Steel Production: Chinese sword-makers traditionally used bloomery and later crucible methods to produce high-quality steel. Although their processes generally yielded more uniform steel (as opposed to the differential hardening seen in Japanese tamahagane), the craftsmanship was highly refined—resulting in blades that were both functional and artistically celebrated. Cultural Impact: These swords were not only tools of warfare but also carried cultural and symbolic significance, influencing martial arts, literature, and art throughout Chinese history.
-
I think and read somewhere chinese language , ceramics and metallurgy are predates Japan , and there is religion aspect also but I am not educated neither of them. I want to see the chinese swords and chronology list and the swords reached the Japan land and the metallurgy of them ? Did China make a steel like tamahagane ? How was the quality ? Did China widely used softcore technology ? Compare timing with China and Japan. Chinese metallurgy has a very long history—one that predates many aspects of Japanese culture such as language, ceramics, and even sword‐making. Over centuries, China developed sophisticated techniques for producing bronze and iron (and later, steel) weapons, and its sword-making traditions influenced—and were later distinguished from—the evolving practices in Japan. Chinese Swords: A Chronological Overview Bronze Age (circa 1100–500 BCE): Early Chinese swords were made of bronze, used by elites and warriors alike. Early Iron Age / Spring and Autumn Period (770–476 BCE): Transition from bronze to iron swords. Iron technology allowed for stronger, more durable weapons. Warring States Period (475–221 BCE): The jian—a straight, double-edged sword—became prominent. This period saw significant refinement in iron-working and forging techniques. Imperial China (Han Dynasty onward, ~202 BCE–220 CE): Steel-making techniques improved, and the jian evolved into not only a weapon but also a symbol of scholarly and martial prowess. Tang (618–907 AD) and Song (960–1279 AD) Dynasties: Further advancements in metallurgy led to high-quality, aesthetically refined swords. Techniques such as pattern welding and precise heat treatment were in use, producing blades celebrated both for their functionality and artistry. Ming Dynasty (1368–1644 AD): Continued evolution produced swords that combined ceremonial beauty with battlefield effectiveness. Transmission to Japan and the Evolution of Japanese Swordmaking Cultural Exchanges: From the Yayoi period onward (roughly 3rd century BCE to 3rd century AD), Chinese cultural and technological influences—often transmitted via Korea—began reaching Japan. Early Japanese swords, influenced by Chinese (and Korean) designs, initially imitated straight blades like the jian. Local Evolution: Over time, Japanese swordsmiths developed their own techniques, most notably the production of tamahagane steel in a traditional tatara furnace. This unique process, along with the practice of differential hardening, led to the creation of curved, single-edged swords (like the katana) that were highly prized for their exceptional sharpness and resilience. Chinese Steel vs. Japanese Tamahagane Chinese Steel Production: Traditionally produced using bloomery and crucible techniques, Chinese steel-making often resulted in more homogeneous steel. The quality was high for its era, and many Chinese swords were both functionally effective and artistically decorated. However, the processes generally did not focus on creating a blade with a deliberately varied hardness. Japanese Tamahagane: Made from iron sand and charcoal in a tatara furnace, tamahagane is prized for its variable carbon content. This variability allows swordsmiths to forge a blade with a hard edge for sharpness and a softer core for flexibility and shock absorption—a process known as differential hardening. Quality Comparison: Both traditions produced excellent blades. Chinese swords were admired for their craftsmanship and often featured beautiful patterning or decoration. Japanese tamahagane, however, became legendary for its performance in combat, with the specific process of differential hardening setting it apart. “Softcore” Technology and Differential Hardening Japanese Differential Hardening: In Japanese sword-making, the blade is coated with a layer of clay before quenching. This causes the edge to cool and harden more quickly than the spine, resulting in a hard edge and softer core. This method (sometimes informally referred to as a "soft core" design) is a hallmark of the Japanese katana, providing a balance of strength, flexibility, and cutting ability. Chinese Techniques: Traditional Chinese sword-making, while advanced, typically did not emphasize a deliberate differential hardening process to create a soft core with a hardened edge. Instead, Chinese blades were often uniformly hardened or produced using pattern welding techniques, focusing on the intrinsic qualities of the steel available. Timing and Innovation: Although Chinese metallurgy and forging date back millennia, the specific innovation of differential hardening emerged prominently in Japan during the later Heian period (around the 10th century) and was further refined during the Kamakura period. In contrast, while Chinese smiths experimented with various forging techniques, the "soft core" approach became a defining characteristic of Japanese sword-making rather than a widespread Chinese practice.
-
Here’s a step-by-step guide to achieving all major colors on your Tamahagane jewel steel, using precise temperature control and oxidation methods. 1. Surface Preparation (Before Heating) Before applying heat, prepare the steel for uniform oxidation: ✅ Polish to a mirror finish → Use 800–2000 grit sandpaper or a buffing wheel. ✅ Clean with acetone or alcohol → Removes oil and fingerprints. ✅ Degrease completely → Any residue can create uneven colors. 2. Heating & Color Formation Table Each color appears at a specific temperature range, controlled by either torch heating or an oven. Color Temperature (°C) Oxide Formed Key Techniques Light Bronze / Gold 200 – 250 Fe₂O₃ (thin layer) Light heating, even flame Deep Bronze 250 – 300 Fe₂O₃ (thicker) Hold temp for a few minutes Purple 300 – 400 Fe₃O₄ + SiO₂ (thin) Even heating, slow cooling Deep Blue 400 – 500 Fe₃O₄ + Cr₂O₃ (if present) Hold at temp for better depth Dark Blue / Black 500 – 800 Thick Fe₃O₄, FeO High temp, low oxygen Red / Orange 250 – 450 Fe₂O₃ (increasing thickness) Expose to more oxygen Greenish Tint 400 – 700 Cr₂O₃ or Fe-P compounds Requires chromium in alloy 3. Methods for Each Color A) Light Bronze / Gold (200–250°C) Heat gently with a torch or in an oven at 200–250°C. Keep exposure brief to avoid going into deeper bronze. Best cooling method: Air cooling. B) Deep Bronze (250–300°C) Hold the steel at this temp longer (1–2 minutes). If using a torch, pass the flame evenly until the color develops. Best cooling method: Slow air cooling. C) Purple (300–400°C) Slowly increase heat; the steel will first turn bronze, then purple. Use an oven for even color distribution. Best cooling method: Air cooling (not quenching). D) Deep Blue (400–500°C) Even, sustained heating is required. A propane torch or an oven works best. Reduce oxygen exposure slightly for a deeper blue. Best cooling method: Slow air cooling. E) Dark Blue / Black (500–800°C) Let Fe₃O₄ grow thicker by holding at high temperatures. Low oxygen will darken the color. Best cooling method: Slow air cooling. F) Red / Orange (250–450°C) Expose to more oxygen by heating in an open flame. Increase oxidation duration to thicken the Fe₂O₃ layer. Best cooling method: Air cooling. G) Greenish Tint (400–700°C, with Chromium) This is rare in pure Tamahagane, but if there’s chromium or phosphorus, heat to 400–700°C. Heat slowly and oxidize gently. Best cooling method: Slow air cooling. 4. Best Heating Techniques Option 1: Torch Heating (Best for Small Pieces) Use a butane, propane, or oxy-acetylene torch. Move the flame evenly across the steel. Stop heating immediately when the desired color appears. Quench or air cool depending on the desired result. Option 2: Oven Heating (For Uniform Color) Preheat an oven or kiln to the exact temperature. Place the steel inside and monitor color changes. Remove and air cool when the target color is reached. Option 3: Controlled Atmosphere (For Professional Results) A salt bath or reducing atmosphere kiln ensures perfect oxidation control. Best for consistent blues, purples, and blacks. 5. Locking in the Colors (Sealing & Finishing) Once the desired color is achieved, seal it for durability: ✅ Clear lacquer → Jewelry & display pieces ✅ Renaissance wax → Protects while keeping a natural look ✅ Automotive clear coat → Best for long-term durability Final Tips ✅ Heat slowly for better control. ✅ Monitor oxidation changes carefully—colors appear in order. ✅ Polish & clean before heating for an even surface. ✅ Test on a scrap piece first!
-
Barry , there are lot more to say, When steel is heated, iron reacts with oxygen to form iron(III) oxide (Fe₂O₃), which gives a reddish hue. which celcius degrees between ? ChatGPT: Iron(III) oxide (Fe₂O₃), which gives a reddish hue, forms on steel when heated in air. The temperature range for Fe₂O₃ formation depends on oxidation conditions, but generally: Temperature Range for Fe₂O₃ (Red Iron Oxide) Formation: 200°C to 500°C → Fe₂O₃ begins forming as a thin reddish layer. 500°C to 800°C → Fe₂O₃ thickens, becoming more visible. Above 800°C → Fe₂O₃ can convert into Fe₃O₄ (magnetite), which is black or blue-black. At lower temperatures (~200–300°C), Fe₂O₃ appears as a thin light red or orange-brown layer. As temperature increases, the layer thickens and darkens. If heating continues above 800°C, Fe₂O₃ transitions to Fe₃O₄, losing its red color. Would you like to control the oxidation to achieve a specific color on your Tamahagane steel? others ? Besides iron oxides (Fe₂O₃, Fe₃O₄), other chemicals and trace elements can contribute to the red, bronze, blue, and purple zones on Tamahagane jewel steel—especially if the steel contains natural impurities from the traditional smelting process. Here's a more detailed list of which chemicals contribute to each color: 🔥 Red & Bronze Zones (200°C – 500°C) Chemical Color Temperature (°C) Notes Iron(III) Oxide (Fe₂O₃) Reddish 200–500°C Main red pigment on steel surfaces. First oxide layer. Copper Oxide (Cu₂O) Reddish-brown 200–400°C If small traces of copper impurities are present in Tamahagane ore. Chromium Oxide (Cr₂O₃) Bronze-green 300–500°C If the steel contains chromium from impurities in the iron sand. Nickel Oxide (NiO) Yellow-Bronze 300–450°C Rare in Tamahagane, but could appear if nickel is present. 🌊 Blue & Purple Zones (300°C – 600°C) Chemical Color Temperature (°C) Notes Iron(II,III) Oxide (Fe₃O₄) Blue-Black 300–600°C Second oxide layer. Blue tint at thinner layers. Titanium Oxide (TiO₂) Blue or Purple 350–550°C From natural titanium impurities in Japanese iron sand (Satetsu). Chromium Oxide (Cr₂O₃) Greenish-Blue 400–600°C Only if chromium is present. Manganese Oxide (Mn₂O₃) Purple-Blue 400–550°C Common in high-quality Tamahagane from Satetsu. 🔥 Purple Zones (450°C – 600°C) Chemical Color Temperature (°C) Notes Titanium Oxide (TiO₂) Violet 400–550°C Natural impurity from Satetsu. Manganese Oxide (Mn₂O₃) Purple-Blue 450–550°C Rare but can create purple halos around blue areas. Iron Oxide Interference Layers (FeO) Purple 500–600°C Due to thin-film interference from multi-layered oxides. How Do These Colors Appear in Tamahagane? The traditional folding process of Tamahagane refines the steel but leaves micro impurities like titanium, manganese, and copper inside the metal. When polished and heated, different oxide layers grow on the steel at different rates. This creates the rainbow-like "jewel steel" effect—especially on high-quality Tamahagane. 🔑 Layer Structure Explanation Layer Color Thickness (nm) Metal Oxide Top Layer Blue, Purple 100–300 nm Fe₃O₄ + TiO₂ + Mn₂O₃ Middle Bronze 300–500 nm Fe₂O₃ + Cu₂O Base Red 500–700 nm Fe₂O₃ Summary Color Ranges: Color Chemicals Temperature (°C) Red Fe₂O₃, Cu₂O 200–500°C Bronze Fe₂O₃, NiO, Cr₂O₃ 300–500°C Blue Fe₃O₄, TiO₂, Cr₂O₃ 350–600°C Purple TiO₂, Mn₂O₃, Fe₃O₄ 450–600°C 🔥 How to Control These Colors on Tamahagane: Color Temperature Time Atmosphere Red 200–300°C Short Dry air (Oxygen-rich) Bronze 300–450°C Medium Dry air Blue 350–550°C Long Dry air or slightly humid Purple 450–600°C Long Dry air + small humidity Conclusion The "jewel steel" effect of Tamahagane is a combination of: Traditional smelting impurities Controlled oxidation layers Natural elements in Satetsu (iron sand) If you want to enhance red, blue, or purple zones, the best method is: Polishing with charcoal or whetstones. Heat tempering between 200–600°C. Using different atmospheres (dry air vs. humid air).
-
Thank you very much Brian and all , I am sure you can give me list of that monosteel technology terminology in Japanese. And I want to know the mono steel spectrum analysis and phase diagram and I say again where the metallurgy locked in the phase diagram.Can you give me references ? And I want to know what did early 1100/1200 years era people did to prevent the blade breakage ? Umut Istanbul
-
Hello Bruce , all I saw about coreless Manu technic is a cutaway computer drawing and filled black and says it is full of hard steel and technics name is manu. Is coreless blade , an 16th century technic or not , I want to know about. At the side of that computer drawing , there were dozen of hard core blades drawings. Umut
-
Hello Bazza, Chatgpt had a answer to my question, The colors observed on Tamahagane jewel steel—red, bronze, blue, and purple—are primarily due to oxide layer formation and light interference effects on the steel's surface. Different elements in the steel contribute to the oxidation process, leading to distinct hues. Here’s a breakdown of which chemicals or compounds are responsible for these colors: 1. Red & Bronze Zones Iron oxides (Fe₂O₃, Fe₃O₄) When steel is heated, iron reacts with oxygen to form iron(III) oxide (Fe₂O₃), which gives a reddish hue. A thinner oxide layer may appear bronze or golden due to interference effects. Copper (if present as an alloy element) Some jewel steels may have trace amounts of copper, which can contribute to a reddish or bronze tint when oxidized. 2. Blue & Purple Zones Iron oxides (Fe₃O₄) & Magnetite layers Fe₃O₄ (magnetite) produces blue-black hues. Interference effects from very thin FeO layers can also lead to a blue or purple sheen. Titanium & Chromium Oxides (if present in alloy) Titanium oxides (TiO₂) & Chromium oxides (Cr₂O₃) can also create blue to purple hues. Heat Tinting & Light Interference Different oxidation thicknesses create thin-film interference, resulting in blue, purple, and other iridescent colors. Color Development Sequence with Heat When steel is heated, the oxide layer grows thicker, creating different colors: Pale yellow → Bronze (thin Fe₂O₃ layer) Reddish → Brown (thicker Fe₂O₃) Purple → Blue (Fe₃O₄ and interference effects) Dark blue to black (thick oxide layers, magnetite formation)