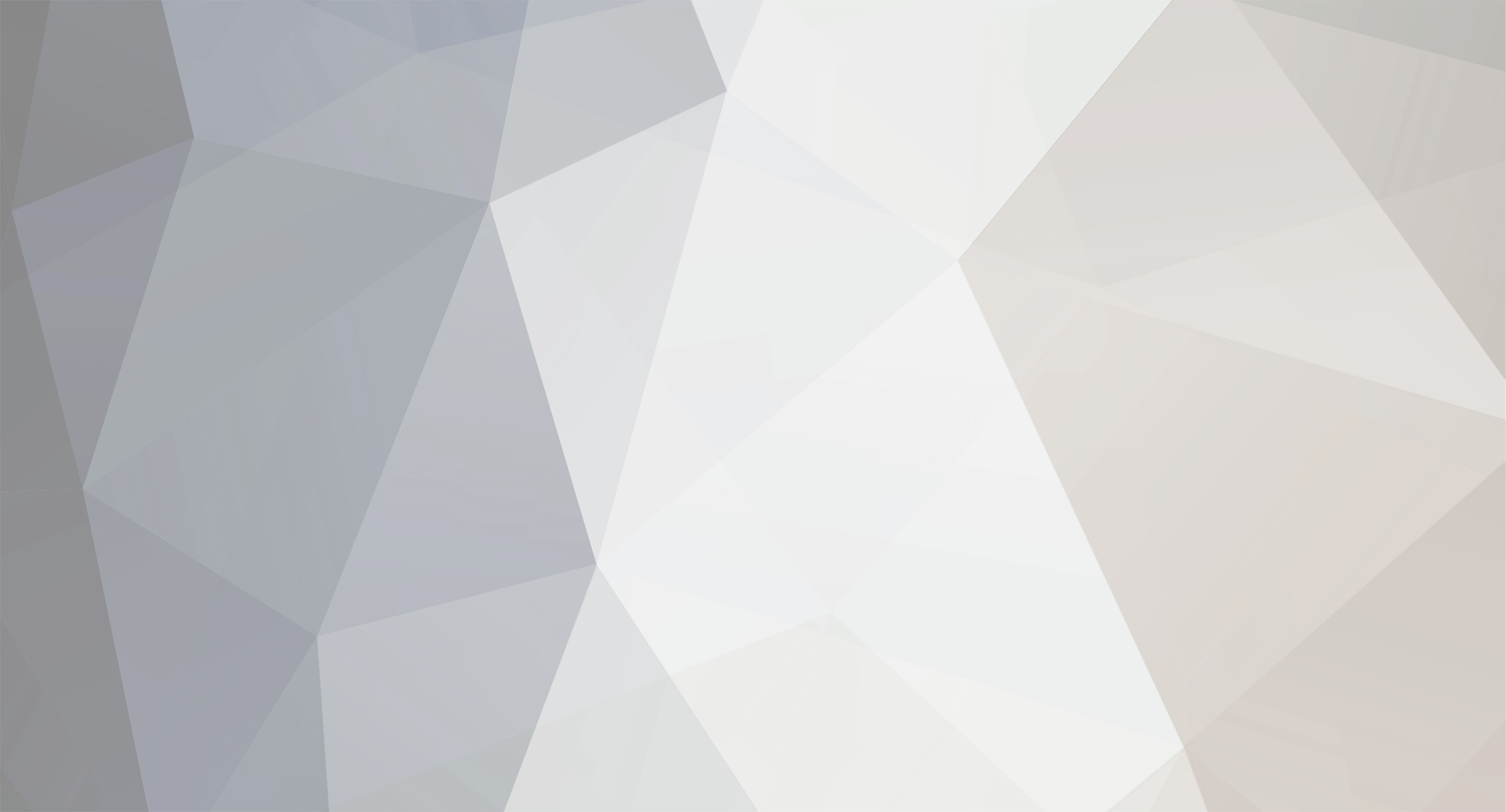
Robert S
Gold Tier-
Posts
159 -
Joined
-
Last visited
-
Days Won
1
Content Type
Profiles
Forums
Events
Store
Downloads
Gallery
Everything posted by Robert S
-
I liked lazy uchi mono :-)
-
His summary of the story in the blog is interesting. It tells a lot about the state of the war that the top graduate went to serve on a submarine, which would not have been the case in the pre-war Japanese navy.
-
I also don't understand the difference in storage conditions for the nihonto between koshirae and shirasaya. If the issue is potential wear on really high quality koshirae, that I understand, but most of the koshirae that I see are not at that level.
-
Giving a nihonto some use ?
Robert S replied to Nicolas Maestre's topic in General Nihonto Related Discussion
I may drift off into the mystical here... but to me there is a significant difference between an object which has been used with respect for centuries, and one which has been stored in a display case. There's a deep energy which is imparted with the combination of use, care and time, which differentiates certain objects. I have some antique tools which are now both valuable and irreplacable, but which I continue to use - really as an act of respect for the maker and past users. Even certain sorts of wear can be part of that energy. Obviously, I couldn't recommend using a nihonto for it's original intended use :-)... but being used and cherished by a skilled iaito practitioner to me would enhance the nihonto, even if there are some nearly microscopic scratches caused by drawing. I also agree that there is something totally different, in an important way, about the experience of practicing with a centuries old nihonto, playing a centuries old violin, or using a very old handmade tool, even if a new one is objectively better. You become a link in a chain of skill and, hopefully not overstating things, love. Personally I think using a koto nihonto for iaito, with enormous respect and reverence, will enhance the blade. Told you it was going to drift into the mystical :-) -
Not to mention that it is not really handachi koshirae - looks like a mix and match grouping of pieces.
-
Facial tissues and other similar products are often made in whole or part from ground, rather than chemically pulped, fiber, and residual very fine grit material from the grinding stones can show up in the tissue. I never use facial tissue for cleaning lenses, for instance, since it can result in scratches on the lens.
-
Grey: Speaking as someone who has had involvement with the pulp and paper industry, I'd be a little careful with facial tissue. There can be micro abrasives in them, as a result of the manufacturing process. I use 100% cotton cosmetics pads instead.
-
Any other Canadians had their blades stuck at customs?
Robert S replied to dyn's topic in General Nihonto Related Discussion
Based on my experience, yes, it is out of norm. I imported a blade last year from Japan to Canada, and it came through customs (same processing centre) in a few days. I would reach out to Canada Customs... although getting any meaningful answer is probably unlikely, at least it will let them know you are on it. Please do post what the outcome is, as I may be importing more nihonto, and would like to know if this represents something that we should begin to expect. -
Well, it's hard to see, and may be an artifact of the photography, but it does look like some of the granular structure along the hamon may have corroded in the past, leaving slight depressions. If so, I'm thinking the more recent togishi decided not to polish them all the way out, in the interests of reducing metal removal. But looking at the actual blade may tell you that I'm wrong :-)
-
The metal grain of that blade is quite interesting. It's hard to tell from the photos, but I wonder if this blade had experienced some corrosion in the past.
-
Because chisels like that use a very hard metal for the cutting edge, they can retain a very sharp edge during use... but they can also chip if not used carefully... as I have reason to know. I agree that Kurashige Tools are likely to know more about the maker, etc.
-
Well, I do quite a lot of cabinet making, and own an extensive collection of Japanese and western chisels, planes, etc, including some which I made. What was your specific question regarding these chisels?
-
What exactly determines the price of a nihonto?
Robert S replied to Ikko Ikki's topic in General Nihonto Related Discussion
As Hoshi said, it may be a kantei trait, but I don't think that the presence of shintetsu on a sword is ever going to increase the value of a sword, as compared to a sword by the same maker without shintetsu. -
I have a bit of a question about this theory, since it seems that for most of the time that Japanese swords were produced, production was clustered around streams bearing quality iron sands. I don't know why this would be the case unless they were utilizing the iron sands to make tamahagane, and using that to make the swords. I'm sure that they did integrate steel from other sources when available, but the idea that tamahagane was only used as a primary material for 70 years seems pretty unlikely.
-
Nice work! A few comments: 1. The "Vickers hardness in cross section" page at the beginning of the Mechanical section is in there twice, once with an added "antique" label, and once without. 2. The data presented on trace element concentration (Phosphorus and Sulphur) in iron sands indicates that these elements tended to be high enough to increase brittleness, and there seems to be limited effect of forging/folding on the concentration of these elements. Despite this, the antique blades tested seemed to have achieved lower trace element levels... so either they were using better iron sands, or eliminating some of these elements through the bloomery process, or they were able to reduce the concentration of these elements through forging or other processes. 3. The relative consistency of carbon content in the edges of the antique blades is pretty remarkable, given the variation on the iron sands. I'd love to know how they determined carbon percentage, since they clearly had pretty good ability to control it. Maybe it was just trial and error with a given iron sand/bloomery process and resulting grades of tamahagane, resulting in a rule of thumb, but maybe there were some other indicators in heating, color or forging properties. I've done some knife making, but of course with modern steels I was starting with tightly controlled steel grades, so never worries about this. 4. Your summary of the forging and folding process on page 5 sort of implies that forging and folding were exclusively associated with the forge welding process of different steel grades toward the end of the forging process. But of course there was a whole bunch of forging and folding of the individual steel grades prior to the process of forge welding and folding the different steel grades together. Thanks for putting this together! I'm getting awfully tempted to try to put together a miniature bloomery furnace and see what I can get with local iron sands :-)
-
A nice video about types of Grain Patterns
Robert S replied to Pierre F's topic in General Nihonto Related Discussion
Nothing is as good as a blade in hand, but that video is definitely useful to us newbies as a complement to books and other resources. -
It is s stunning piece of craftsmanship. My guess is that given this is the second time it has been offered, if it hits 250,000 yen the seller might let it go, although they probably believe it it worth more.
-
For me #4 comes closest, but neither the taper nor the kissaki are quite to my taste. More taper and a longer, more elegant kissaki is what rings with me.
-
First choice for me would be #2, last would be a saw off between #s 3 and 4.
-
Looks a lovely piece, and I agree with the thought regarding the value of supporting living swordsmiths and helping to keep the craft alive. Nicely done!
-
Shirasaya not closing all the way?
Robert S replied to chinaski's topic in General Nihonto Related Discussion
It sounds possible that the reason the saya was cracking in the first place was that it was shrinking due to the low humidity, and becoming too tight around the habaki. Now that you've closed the gap in the saya. the habaki won;t fit all the way in. -
60+. Bought my first nihonto last year, but collecting and occasionally making knives and edged tools for 45+ years Robert S