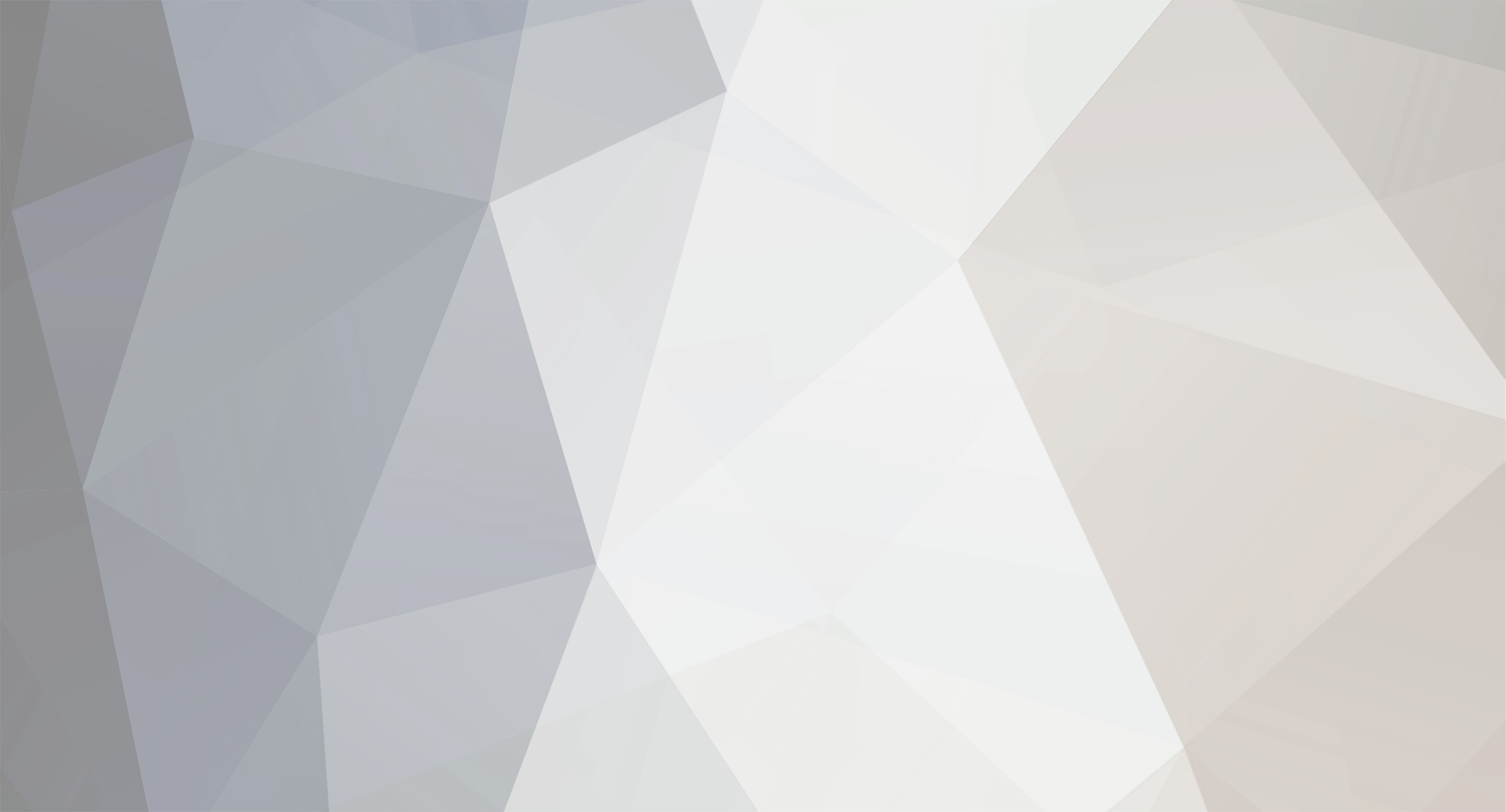
Robert S
Gold Tier-
Posts
172 -
Joined
-
Last visited
-
Days Won
1
Everything posted by Robert S
-
Florian: The photos that I have of the back side are so low resolution that I won't bother posting. I'll add a photo when I receive the tsuba and can take some of my own. It's pretty similar in aesthetics. I'm also not sure if there are inlays missing - I don't think so, but I'll need to have it in hand before I'm sure. Robert S
-
Dan Tsuba: That's a great example of the characteristics of cast iron which are evident with destructive testing. Not of course something most of us would prefer as a testing method, but it does happen! Robert S
-
Dan: I don't think it's the only way of determining whether something is cast, since usually the subsequent clean-up on a casting has not been done to the level we were discussing, or the casting contains obvious flaws, and it's pretty obviously cast. But if someone really had subsequently worked a high quality casting to the point that all casting marks and characteristics had been removed, then you'd have to know more about the specific metallurgy of irons used for casting versus forging at that time, as well as what chemical changes (for instance, carbon content changes) occurred as a result of forging. I've seen information on this from people who are expert metallurgists... which I am not :-) Robert S
-
Exposure to radiation wasn't quite on my list, but it does look like it may speak to a very sad piece of history.
-
DKR: I agree that there are significant condition problems. But beneath that you can see that the tsuba was deliberately made to look rustic or simple... so the rust sort of goes with the aesthetic, although I'll work to stabilize it. I know this look isn't everyone's cup of tea (pardon the pun), but I'm a great fan of cups and other utensils made for chanoyu... so it's right up my alley :-) Robert S
-
Just picked this up - the photos are from the seller. I thought it was an interesting example of a wabi/chanoyu aesthetic in a tsuba. Anyone else have one which falls into this category, or thoughts on it?
-
I've done casting, and good castings can definitely be smoothed and fine tuned to the point that they would look (and practically are) carved. However, poor castings would still have micro flaws which would be evident, and clearly different types of flaws than forged iron. So it depends on the skill of the caster. The metal would still be significantly different in microstructure and/or chemistry, but you'd be unlikely to know without destructive testing (not recommended :-) ), unless you have access to some pretty sophisticated equipment.
-
Converting a tsuba to a netsuke would make a pretty heavy netsuke!
-
That saya is a beautiful piece of lacquer work!
-
As I noted in a previous post, there is some risk of micro-scratches with tissue, since it may contain abrasive particles, due to how it is produced. My caution on this front is for the same reason that I would never use tissue on a camera lens.
-
As a reference. I keep my blade in koshirae, and live in a temperate climate within 1 km of the ocean, but in a house which is heated during the winter. I also inspect my blade and give it a basic wipedown at least weekly, and oil it at least once a month. No rust at all, so far.
-
Or 100% cotton cosmetics pads.
-
I liked lazy uchi mono :-)
-
His summary of the story in the blog is interesting. It tells a lot about the state of the war that the top graduate went to serve on a submarine, which would not have been the case in the pre-war Japanese navy.
-
I also don't understand the difference in storage conditions for the nihonto between koshirae and shirasaya. If the issue is potential wear on really high quality koshirae, that I understand, but most of the koshirae that I see are not at that level.
-
Giving a nihonto some use ?
Robert S replied to Nicolas Maestre's topic in General Nihonto Related Discussion
I may drift off into the mystical here... but to me there is a significant difference between an object which has been used with respect for centuries, and one which has been stored in a display case. There's a deep energy which is imparted with the combination of use, care and time, which differentiates certain objects. I have some antique tools which are now both valuable and irreplacable, but which I continue to use - really as an act of respect for the maker and past users. Even certain sorts of wear can be part of that energy. Obviously, I couldn't recommend using a nihonto for it's original intended use :-)... but being used and cherished by a skilled iaito practitioner to me would enhance the nihonto, even if there are some nearly microscopic scratches caused by drawing. I also agree that there is something totally different, in an important way, about the experience of practicing with a centuries old nihonto, playing a centuries old violin, or using a very old handmade tool, even if a new one is objectively better. You become a link in a chain of skill and, hopefully not overstating things, love. Personally I think using a koto nihonto for iaito, with enormous respect and reverence, will enhance the blade. Told you it was going to drift into the mystical :-) -
Not to mention that it is not really handachi koshirae - looks like a mix and match grouping of pieces.
-
Facial tissues and other similar products are often made in whole or part from ground, rather than chemically pulped, fiber, and residual very fine grit material from the grinding stones can show up in the tissue. I never use facial tissue for cleaning lenses, for instance, since it can result in scratches on the lens.
-
Grey: Speaking as someone who has had involvement with the pulp and paper industry, I'd be a little careful with facial tissue. There can be micro abrasives in them, as a result of the manufacturing process. I use 100% cotton cosmetics pads instead.
-
Any other Canadians had their blades stuck at customs?
Robert S replied to dyn's topic in General Nihonto Related Discussion
Based on my experience, yes, it is out of norm. I imported a blade last year from Japan to Canada, and it came through customs (same processing centre) in a few days. I would reach out to Canada Customs... although getting any meaningful answer is probably unlikely, at least it will let them know you are on it. Please do post what the outcome is, as I may be importing more nihonto, and would like to know if this represents something that we should begin to expect. -
Well, it's hard to see, and may be an artifact of the photography, but it does look like some of the granular structure along the hamon may have corroded in the past, leaving slight depressions. If so, I'm thinking the more recent togishi decided not to polish them all the way out, in the interests of reducing metal removal. But looking at the actual blade may tell you that I'm wrong :-)
-
The metal grain of that blade is quite interesting. It's hard to tell from the photos, but I wonder if this blade had experienced some corrosion in the past.