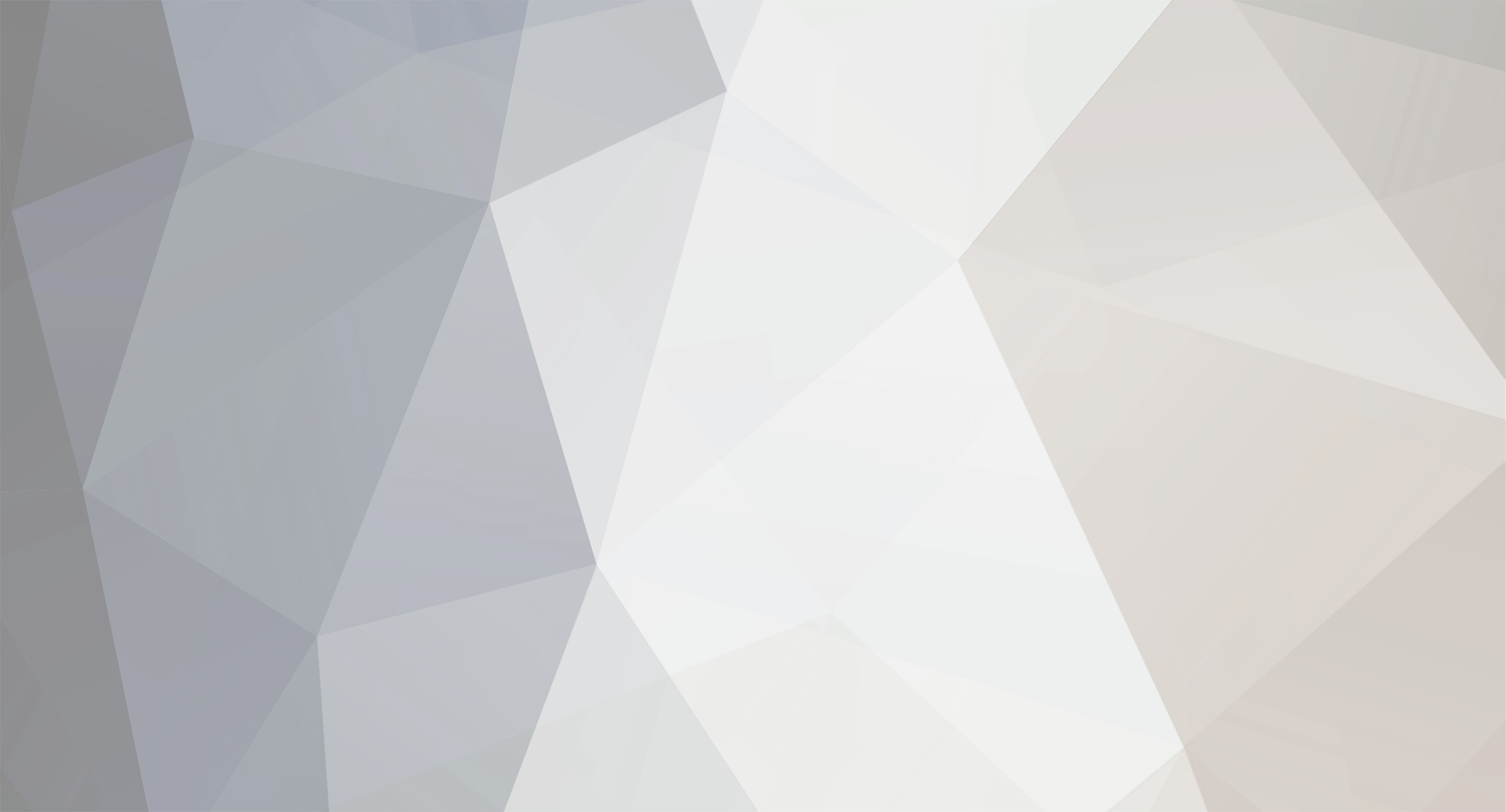
Robert S
Gold Tier-
Posts
159 -
Joined
-
Last visited
-
Days Won
1
Content Type
Profiles
Forums
Events
Store
Downloads
Gallery
Everything posted by Robert S
-
I actually like it when they retain the old B&W images from 100 years ago or so - it gives a sense of the curatorial/condition history of the piece... although it would be nice to also have a modern colour image for comparison. Hate to say it but some museums might be embarrassed by the evident deterioration if they did include both sets of images, though.
-
I think that almost the only way to do any of these traditional crafts now in the west is for the love of them, and as a side hustle, at best.
-
That sounds wrong, unless it was a treasure sword with a long and exceptional provenance. One way to think about this is, for the sword itself, what the average annual gross earning of a sword smith was, before their costs for charcoal, tamahagane, etc. and how many swords a year they could make. Then add the cost for polishing, koshirae, etc. - maybe doubling the final price. If the swords were really in that range I think there would have been some stupendously wealthy swordsmiths who were also serving as bankers to the daimyos... and I don't think that happened, so something is being lost in translation.
-
I wonder why and when these shakudo plugs were put in. Was this a design decision by the original maker? Probably not, but ??? Or if they were put in later why? A style moving against peirced tsuba? Very interesting.
-
Possible: a katana by the third generation bizen iesuke, and custom koshirae for that and my similar period Bizen wakizashi to create a Daisho Impossible: Yamatorige :-)... But maybe commissioning an homage to the sword by a contemporary Japanese swordsmith is possible.
-
Wowzers. I can't believe that Bonhams were fooled by that! Even if you thought it was really antique, the quality is so horrible...
-
Curran: Your comment on the "grainy" texture of the steel is interesting, since there is also obvious forging in some cases. I wonder what causes that? Is it possible that some of these had at one time low level active rust, which has been stabilized, but which disproportionately effected one of the types of steel grain metallurgy in the relatively course grain? Hard to see how it would have looked like that right after forging.
-
Dan: One important thing to understand is that lost wax mold making materials and methods have changed significantly in the last century or so, making iron casting (versus other metals) using lost wax much more likely currently that it would have been in the 19th century, or earlier. I do believe that ultimately testing will show that sand casting was being used to produce some edo period tsuba - probably for the lower end of the market. We know it was being used to produce other iron objects, so I'd be extremely surprised if it wasn't being done for tsuba. Oh for a time machine to go back to a "tsuba store" / sword seller in 1780! But at the end of the day, I don't find the question as significant as many here. If the casting and post casting clean-up and finishing has been so well done that you can't tell for sure whether it was cast, that's serious craft in its own right, trust me! I just enjoy the objects on their merits... but I'm not a collector in the serious sense of the word - I'm just a dilettante who knows what he likes, as I proved with the recent piece I posted here... :-)
-
Expert knowledge and experience
Robert S replied to Lukrez's topic in General Nihonto Related Discussion
Not me :-). I must confess that when it comes to that kind of money I'm more likely to be buying a 30s Rolls, although I haven't pulled the trigger yet. -
I don't know for sure whether that tsuba was sand cast or not, although I agree with Dan Tusba's observations. I will say that that surface texture would be a lot easier to achieve with sand casting than in any other way. But Japanese craftsmen are amazing in their ability to painstakingly achieve textures and effects. Robert S
-
Florian: The photos that I have of the back side are so low resolution that I won't bother posting. I'll add a photo when I receive the tsuba and can take some of my own. It's pretty similar in aesthetics. I'm also not sure if there are inlays missing - I don't think so, but I'll need to have it in hand before I'm sure. Robert S
-
Dan Tsuba: That's a great example of the characteristics of cast iron which are evident with destructive testing. Not of course something most of us would prefer as a testing method, but it does happen! Robert S
-
Dan: I don't think it's the only way of determining whether something is cast, since usually the subsequent clean-up on a casting has not been done to the level we were discussing, or the casting contains obvious flaws, and it's pretty obviously cast. But if someone really had subsequently worked a high quality casting to the point that all casting marks and characteristics had been removed, then you'd have to know more about the specific metallurgy of irons used for casting versus forging at that time, as well as what chemical changes (for instance, carbon content changes) occurred as a result of forging. I've seen information on this from people who are expert metallurgists... which I am not :-) Robert S
-
Exposure to radiation wasn't quite on my list, but it does look like it may speak to a very sad piece of history.
-
DKR: I agree that there are significant condition problems. But beneath that you can see that the tsuba was deliberately made to look rustic or simple... so the rust sort of goes with the aesthetic, although I'll work to stabilize it. I know this look isn't everyone's cup of tea (pardon the pun), but I'm a great fan of cups and other utensils made for chanoyu... so it's right up my alley :-) Robert S
-
Just picked this up - the photos are from the seller. I thought it was an interesting example of a wabi/chanoyu aesthetic in a tsuba. Anyone else have one which falls into this category, or thoughts on it?
-
I've done casting, and good castings can definitely be smoothed and fine tuned to the point that they would look (and practically are) carved. However, poor castings would still have micro flaws which would be evident, and clearly different types of flaws than forged iron. So it depends on the skill of the caster. The metal would still be significantly different in microstructure and/or chemistry, but you'd be unlikely to know without destructive testing (not recommended :-) ), unless you have access to some pretty sophisticated equipment.
-
Converting a tsuba to a netsuke would make a pretty heavy netsuke!
-
That saya is a beautiful piece of lacquer work!
-
As I noted in a previous post, there is some risk of micro-scratches with tissue, since it may contain abrasive particles, due to how it is produced. My caution on this front is for the same reason that I would never use tissue on a camera lens.
-
As a reference. I keep my blade in koshirae, and live in a temperate climate within 1 km of the ocean, but in a house which is heated during the winter. I also inspect my blade and give it a basic wipedown at least weekly, and oil it at least once a month. No rust at all, so far.
-
Or 100% cotton cosmetics pads.