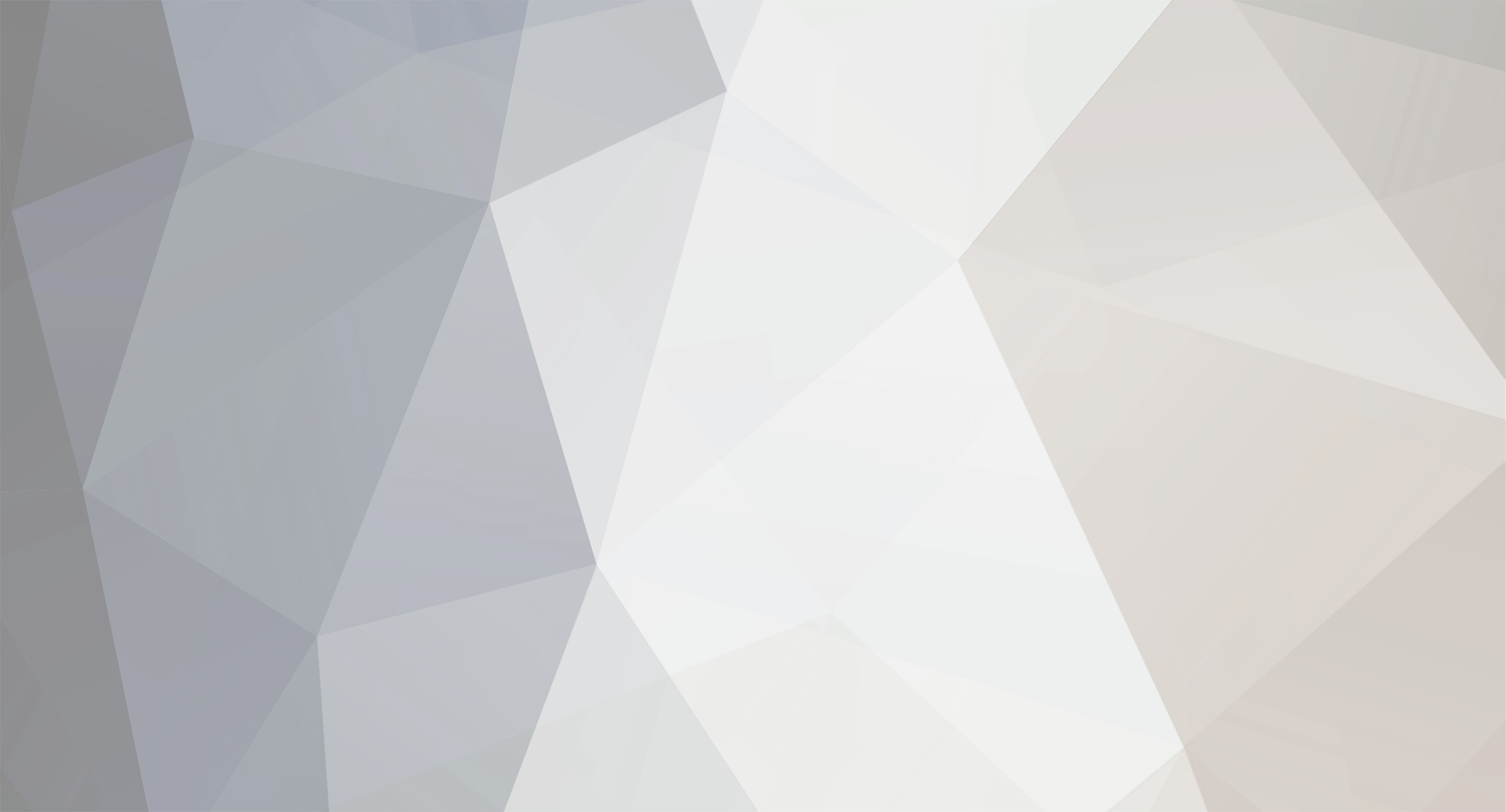
Robert S
Gold Tier-
Posts
171 -
Joined
-
Last visited
-
Days Won
1
Content Type
Profiles
Forums
Events
Store
Downloads
Gallery
Everything posted by Robert S
-
A word about amateur polishing
Robert S replied to Brian's topic in General Nihonto Related Discussion
Thanks all for the excellent discussion on training togishi and learning polishing. Lots that I'll be thinking about further there :-) -
A word about amateur polishing
Robert S replied to Brian's topic in General Nihonto Related Discussion
It's a great question. Traditional apprenticeship structures are the way they are for a number of reasons: 1. They were typically training quite young people who had a lot to learn about the factors I mentioned above ( patience, etc.), and were expected to learn that not through organized learning, but mostly through osmosis, because the master didn't have time to become a full time instructor - they had to mostly continue practising their craft. 2. Similarly, they were expected to learn technique in significant part without explicate instruction (except of the "what the heck do you think you're doing, you idiot?" variety :-) - I got lots of that! ) 3. Once they had begun to get some skill, they needed to pay the master back for their skills in the form of work 4. Long apprenticeships served as a gateway which limited the number of practitioners and maintained supply and demand balance. In many other crafts we now accomplish #s 1 and 2 through focused instruction in a much shorter time, replace #3 with tuition, and are desperately shot of skilled people, so #4 no longer applies. I totally agree with the kantei part, and the relation to stone selection, etc. Again, the basics can be explicitly taught, to a significant degree - at least to a journeyman level. A master level then takes many years of practicing. You're always going to have a significant number of practitioners, whether traditionally apprenticed or not, who are working at the journeyman level... and lots of nihonto show signs of that kind of polishing - perfectly acceptable, but not inspired. -
A word about amateur polishing
Robert S replied to Brian's topic in General Nihonto Related Discussion
Jean: I'm fully aware of the structure of nihonto steel, and the complexities of the interaction of that steel with a natural stone. That is in fact what fascinates me. I want to start experimenting on my own knives to understand how natural stone and other materials vary in effect, including microscopic examination of the slurry and surfaces produced. Then on to older Japanese knives (pre stainless) which are more similar to nihonto (forged, folded, differentially hardened) As for whether I would try to learn how to build a violin without being taught: absolutely. I'm journeyman level in quite a number of crafts, and master level in one, and that is exactly how I have learned many of them. I just wouldn't presume to create a Stradivarius first go :-). There's a lot of talk here about technique. In my experience with training people in any craft, teaching the technique is the easy part, although it is important. The more critical parts (and the harder parts to teach) are patience, visualization (of what the desired end state is), observation ( of what effect each moment's work is having), understanding (why is that happening), and adaptation (closing the feedback loop). Some people are never able to learn those skills in a deep way. I honor and respect the knowledge and thoughts of everyone on this forum, and one of the great strengths of this group is that we don't all come from the same culture or background. The more we learn, the more fascinating it is. -
A word about amateur polishing
Robert S replied to Brian's topic in General Nihonto Related Discussion
John: I'm not talking about a process that would produce "ill trained grinders" :-). I am talking about a process that would allow new togishi to be trained through alternative avenues than traditional apprenticeship. I won't write the essay that I could on why traditional apprenticeship is structured the way it is, and the benefits and drawbacks of that approach, but I will say that I do not follow the "that's the way it's always been done, so that's the only way to do it" school. I was traditionally trained in one artform, and I see the improvements in results that are being achieved with more modern training methods. -
A word about amateur polishing
Robert S replied to Brian's topic in General Nihonto Related Discussion
Oh yes, and on the subject of stones, I'm also going to experiment with alternative options for very expensive/unavailable stones. As a knife maker, I'm very familiar with how natural stones work, and I 100% agree that substituting, for instance, ceramic artificial stones creates a very different process and result. However, I am curious whether combining industrial micro abrasives with other softer powdered materials, plus modifying the hardness of the substrate, can imitate the kind of abrasive paste which develops on a natural stones as you work it, and which is, in my opinion, key to the results that togishi achieve. -
A word about amateur polishing
Robert S replied to Brian's topic in General Nihonto Related Discussion
The one issue I have with a lot of this thread is that it seems to imply that polishing is a black art, which tends to dissuade people from even trying to learn it. I think we all need to be thinking carefully about how we encourage people to learn it responsibly and at least reasonably within the togishi tradition, given that we already have a shortage of polishers, and it's only likely to get worse. For myself, I am ordering in polishing stones and supplies, and I am going to start experimenting, following all the information I can gather from books, videos, etc. ... but don't worry, not on nihonto. As an occasional knifesmith, I have old blades lying around that weren't my favourites, and which have collected some rust or discolouration over the years. I'm going to see what results I can get using traditional togishi methods as best I understand them, and then move on to traditional Japanese kitchen knives, etc. Someday, years from now, if I'm getting consistently repeatable and high quality results with those, then yes, I will work on a cheap nihonto as a trial. Given that I can't afford a 5 to 10 year apprenticeship in Japan, that seems to be the only path, and even if I never venture to work on a nihonto, I will have learned a great deal about traditional Japanese steel, polishing, etc., which can only benefit my understanding of nihonto. I'll also meticulously document my journey, which may help someone else down the line. Finding outside the box methods to encourage the development of new generations of polishers is probably necessary if we really care about the preservation of nihonto. -
Comparing the mei on this sword and the one in the 2017 post, it's clear they're not by the same person. However, since there were multiple generations, that doesn't necessarily mean that one or both are gimei. More examples would be needed to be sure.
-
I didn't know that Picasso ever designed tsuba... but that is clearly a cubist tsuba!
-
Thanks, David. It's a great resource for learning an bit more about tsuba attributions
-
Based on the photos, I don't see evidence of delamination resulting from corrosion. Forged steel typically does have layers - it's a feature, not a problem, unless the corrosion has progressed to the point where delamination is occurring, which is rare. Truthfully the level of rust on that tsuba looks superficial, and worth stabilizing. A sidebar story on steel: for a period in the 1980's, Nissan was using a recycled steel which had not been properly resmelted on the frames of their trucks. That stuff delaminated at the drop of a hat! The old smiths who made swords, tsubas, etc., were way better at steelwork than 80's Nissan!
-
I actually like it when they retain the old B&W images from 100 years ago or so - it gives a sense of the curatorial/condition history of the piece... although it would be nice to also have a modern colour image for comparison. Hate to say it but some museums might be embarrassed by the evident deterioration if they did include both sets of images, though.
-
I think that almost the only way to do any of these traditional crafts now in the west is for the love of them, and as a side hustle, at best.
-
That sounds wrong, unless it was a treasure sword with a long and exceptional provenance. One way to think about this is, for the sword itself, what the average annual gross earning of a sword smith was, before their costs for charcoal, tamahagane, etc. and how many swords a year they could make. Then add the cost for polishing, koshirae, etc. - maybe doubling the final price. If the swords were really in that range I think there would have been some stupendously wealthy swordsmiths who were also serving as bankers to the daimyos... and I don't think that happened, so something is being lost in translation.
-
I wonder why and when these shakudo plugs were put in. Was this a design decision by the original maker? Probably not, but ??? Or if they were put in later why? A style moving against peirced tsuba? Very interesting.
-
Possible: a katana by the third generation bizen iesuke, and custom koshirae for that and my similar period Bizen wakizashi to create a Daisho Impossible: Yamatorige :-)... But maybe commissioning an homage to the sword by a contemporary Japanese swordsmith is possible.
-
Wowzers. I can't believe that Bonhams were fooled by that! Even if you thought it was really antique, the quality is so horrible...
-
Curran: Your comment on the "grainy" texture of the steel is interesting, since there is also obvious forging in some cases. I wonder what causes that? Is it possible that some of these had at one time low level active rust, which has been stabilized, but which disproportionately effected one of the types of steel grain metallurgy in the relatively course grain? Hard to see how it would have looked like that right after forging.
-
Dan: One important thing to understand is that lost wax mold making materials and methods have changed significantly in the last century or so, making iron casting (versus other metals) using lost wax much more likely currently that it would have been in the 19th century, or earlier. I do believe that ultimately testing will show that sand casting was being used to produce some edo period tsuba - probably for the lower end of the market. We know it was being used to produce other iron objects, so I'd be extremely surprised if it wasn't being done for tsuba. Oh for a time machine to go back to a "tsuba store" / sword seller in 1780! But at the end of the day, I don't find the question as significant as many here. If the casting and post casting clean-up and finishing has been so well done that you can't tell for sure whether it was cast, that's serious craft in its own right, trust me! I just enjoy the objects on their merits... but I'm not a collector in the serious sense of the word - I'm just a dilettante who knows what he likes, as I proved with the recent piece I posted here... :-)
-
Expert knowledge and experience
Robert S replied to Lukrez's topic in General Nihonto Related Discussion
Not me :-). I must confess that when it comes to that kind of money I'm more likely to be buying a 30s Rolls, although I haven't pulled the trigger yet. -
I don't know for sure whether that tsuba was sand cast or not, although I agree with Dan Tusba's observations. I will say that that surface texture would be a lot easier to achieve with sand casting than in any other way. But Japanese craftsmen are amazing in their ability to painstakingly achieve textures and effects. Robert S
-
Florian: The photos that I have of the back side are so low resolution that I won't bother posting. I'll add a photo when I receive the tsuba and can take some of my own. It's pretty similar in aesthetics. I'm also not sure if there are inlays missing - I don't think so, but I'll need to have it in hand before I'm sure. Robert S