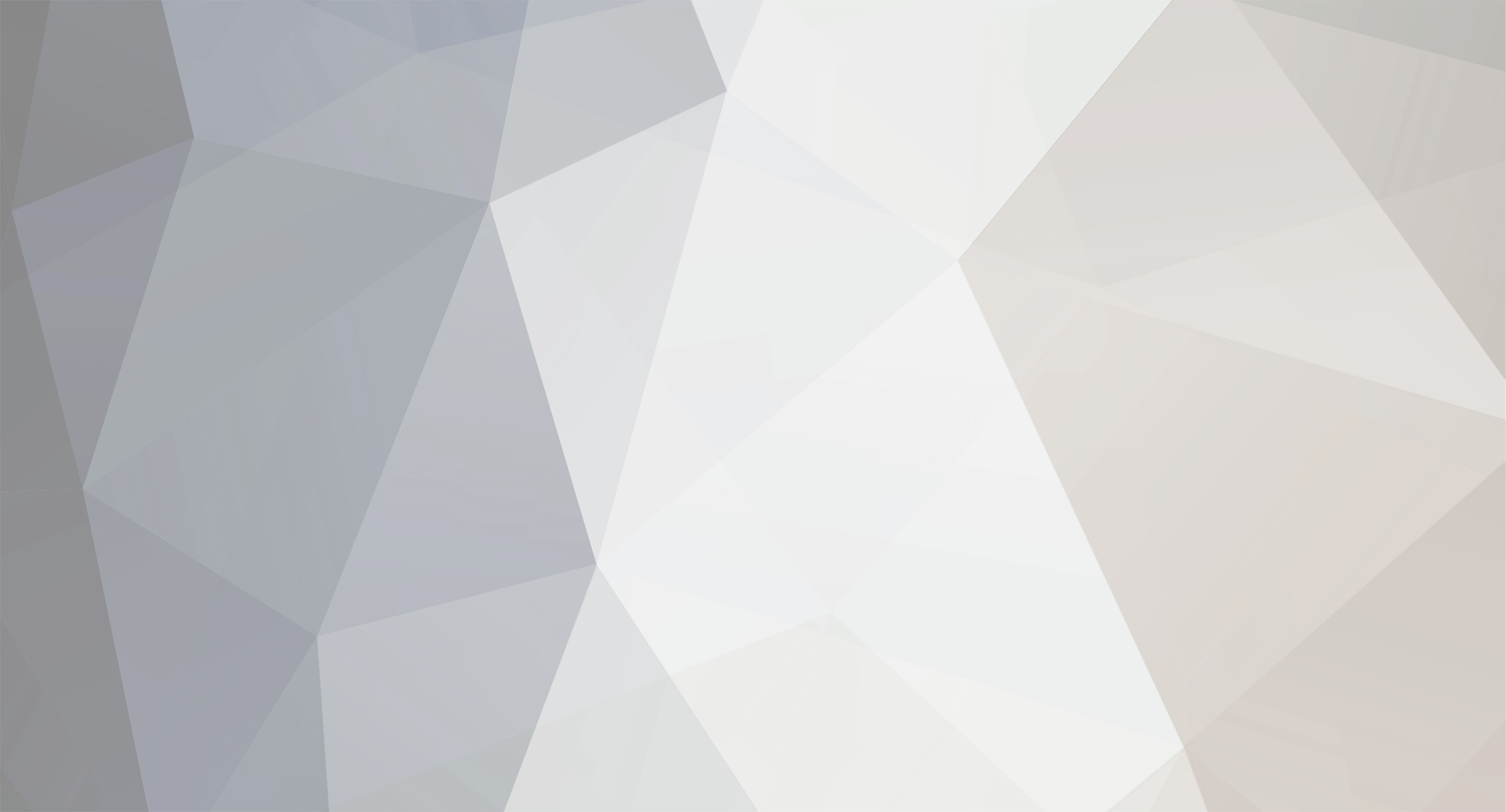
Robert S
Gold Tier-
Posts
168 -
Joined
-
Last visited
-
Days Won
1
Content Type
Profiles
Forums
Events
Store
Downloads
Gallery
Everything posted by Robert S
-
Need some expertise on blade.
Robert S replied to Nazar's topic in General Nihonto Related Discussion
Nazar: Just wanted to pass on my total support for Ukraine in this horrible war. I'm so sorry you've had to put aside your life to fight off an aggressive invader. I hope that soon this will be in the past. Growing up in Saskatchewan, Canada, I lived within a Ukrainian expat community, many of whom arrived as a result of past horrific actions initiated by Moscow. Slava Ukraine! Robert S. -
I wonder what the evidence is for this claim in particular. I would expect that there would be few blades out there which have been polished through to the core steel if that were true... but it seems that they are not uncommon.
-
Aogami Super - Blue Steel and Tamahagane Steel
Robert S replied to Mustafa Umut Sarac's topic in Nihonto
Tamahagane is a form of bloomery steel. which has much lower elemental control than modern steels. Japanese smiths made up for that with extremely sophisticated processing of tamahagane, which modified the content of carbon and other elements. Modern steels can have extremely tight control of elemental content, crystalization, etc. which allows blade manufacture with much lower effort... but the end results in both cases can be exceptional. The only meaningful comparison is the end product, not the underlying steel. -
Bizen Norimitsu? Gimei or real?
Robert S replied to Ronald Aguirre's topic in General Nihonto Related Discussion
Definitely needs a polish, but I don't think it's that "dead", at least compared to some I've seen. If you love the blade, I'd say go for it, as long as it isn't too expensive -
Where historical patina really is historical patina, I think most collectors are interested. The problem is that most - indeed I would say almost all - of the patina on nihonto isn't historical (except in the case of the nakago)... because the Japanese owners over the centuries weren't interested in patina and had the blades polished when they began to get marked. Thus what we see these days is more likely to be signs of a blade that has been neglected in the 20th/21st century... which I suppose is an indicator of the changes in Japan in more recent history, but not terribly interesting. There are a tonne of well and truly rusted blades out there which were abandoned in sheds and closets in Japan... but that patina is a real problem!
-
What a gargantuan mess, Neil. Unbelievable. We don't have those problems (yet) in Canada, fingers crossed.
-
A word about amateur polishing
Robert S replied to Brian's topic in General Nihonto Related Discussion
You can see that it was "buffing good" alright, probably with a power buffer, which has completely blurred the shape (even of a "hideous Chinese fake") :-) -
That nakago is... odd. The portion with the signature appears to have been attached to the sword at some point, yet the portion itself appears to be suriage. Makes me wonder if this might be a concatenation - a portion of a nakago off of a very old, broken sword attached to a different blade.
-
On the purely subjective side, there are those, like me, who are interested in aesthetics only, and don't particularly care about papers, attributions, value... Mind you, we run a grave risk of being the greater fool in the market as a result, but as long as we're playing with "who cares" money, that's OK. It's not that I'm not fascinated by attributions, and the historical knowledge which is so rich on this forum, but I wouldn't buy a blade with all the papers and attribution in the world if it didn't appeal to me at an aesthetic, non-intellectual level.
-
That discussion by Darcy is really useful. The nihonto I bought recently had red rust on the nakago, and I'm definitely oiling it deeply and repeatedly, to try to stabilize it. I think some stabilization even of black iron oxide surfaces is worthwhile, to prevent the potential onset of red rust.
-
It was great fun lurking i this thread. I don't know nearly enough to even have ventured a guess. Way to go everyone who did! One question: Nihon Shinto Shi mentions "shallow Sori". Looking at that blade, I wouldn't have defined the sori as shallow - more like average... but my eye is probably off.
-
Am I correct in thinking that what you are pointing at with the phrase "Damascus pattern" is really pattern welded steel ( which definitely does get called damascus these days). The old original Damascus steel from Europe/the Middle East was much more like Japanese nihonto steel, to my knowledge.
-
Shakudo when it loses its patina due to wear is bronze/copper colored, in my experience. This is distinctly brassy looking. Although there are a lot of different bronze and brass chemistries, this looks to lean on the brass side.
-
I really like the surface texture on that tsuba. Somewhat unusual... which doesn't add anything to school, but there it is!
-
Agreed that the kissaki looks like an odd hybrid shape. I wonder if this is related to reshaping following some damage (an edge chip) near the kissaki.
-
There will always be a significant umber of people who do things the "old way" for all kinds of reasons - the link to past sword-makers, the challenge, or just that a craft produced using different tools will always be slightly different. However, I'd bet that if the old koto sword makers had been given an opportunity to experiment with a hydraulic press, they would have, although they might not have adopted it in the end. Master craftsmen are always experimenting and learning.
-
Well, if you could get the second one for something like $20, it might be worth having just for the sheer awfulness of it. :-)
-
A word about amateur polishing
Robert S replied to Brian's topic in General Nihonto Related Discussion
Thanks all for the excellent discussion on training togishi and learning polishing. Lots that I'll be thinking about further there :-) -
A word about amateur polishing
Robert S replied to Brian's topic in General Nihonto Related Discussion
It's a great question. Traditional apprenticeship structures are the way they are for a number of reasons: 1. They were typically training quite young people who had a lot to learn about the factors I mentioned above ( patience, etc.), and were expected to learn that not through organized learning, but mostly through osmosis, because the master didn't have time to become a full time instructor - they had to mostly continue practising their craft. 2. Similarly, they were expected to learn technique in significant part without explicate instruction (except of the "what the heck do you think you're doing, you idiot?" variety :-) - I got lots of that! ) 3. Once they had begun to get some skill, they needed to pay the master back for their skills in the form of work 4. Long apprenticeships served as a gateway which limited the number of practitioners and maintained supply and demand balance. In many other crafts we now accomplish #s 1 and 2 through focused instruction in a much shorter time, replace #3 with tuition, and are desperately shot of skilled people, so #4 no longer applies. I totally agree with the kantei part, and the relation to stone selection, etc. Again, the basics can be explicitly taught, to a significant degree - at least to a journeyman level. A master level then takes many years of practicing. You're always going to have a significant number of practitioners, whether traditionally apprenticed or not, who are working at the journeyman level... and lots of nihonto show signs of that kind of polishing - perfectly acceptable, but not inspired. -
A word about amateur polishing
Robert S replied to Brian's topic in General Nihonto Related Discussion
Jean: I'm fully aware of the structure of nihonto steel, and the complexities of the interaction of that steel with a natural stone. That is in fact what fascinates me. I want to start experimenting on my own knives to understand how natural stone and other materials vary in effect, including microscopic examination of the slurry and surfaces produced. Then on to older Japanese knives (pre stainless) which are more similar to nihonto (forged, folded, differentially hardened) As for whether I would try to learn how to build a violin without being taught: absolutely. I'm journeyman level in quite a number of crafts, and master level in one, and that is exactly how I have learned many of them. I just wouldn't presume to create a Stradivarius first go :-). There's a lot of talk here about technique. In my experience with training people in any craft, teaching the technique is the easy part, although it is important. The more critical parts (and the harder parts to teach) are patience, visualization (of what the desired end state is), observation ( of what effect each moment's work is having), understanding (why is that happening), and adaptation (closing the feedback loop). Some people are never able to learn those skills in a deep way. I honor and respect the knowledge and thoughts of everyone on this forum, and one of the great strengths of this group is that we don't all come from the same culture or background. The more we learn, the more fascinating it is.