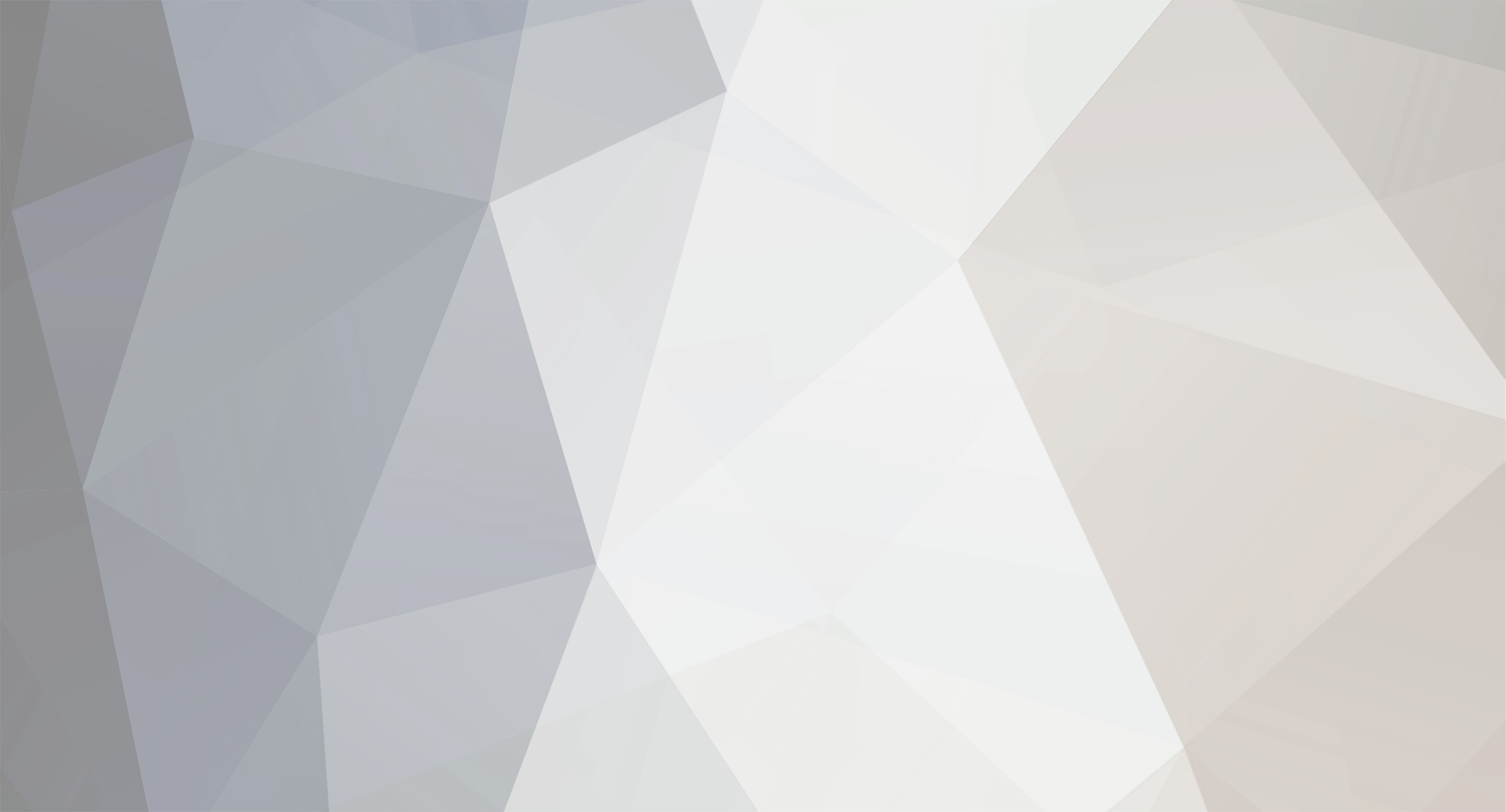
Kiita
Members-
Posts
27 -
Joined
-
Last visited
Profile Information
-
Gender
Male
-
Location:
USA
Profile Fields
-
Name
Aaron
Recent Profile Visitors
The recent visitors block is disabled and is not being shown to other users.
Kiita's Achievements
-
That's what I meant, even if it perhaps wasn't clear from what I wrote. In my experience, while most modern honyaki knives are monosteel in that they are made from a single piece of solid steel, they're rarely referred to as such, as the differential hardening puts them in a category of their own. Monosteel is usually meant as referring to solid steel, through-hardened (fully hardened). This is a matter of semantics, and on some level subjective. The metal ferrule is common on older hocho, especially if they were not at the higher end pricewise when originally sold.
-
The attached diagram may be of use. Monosteel is western parlance for a solid steel blade with no hamon (if it had a hamon it would be called honyaki), not sure what the Japanese term is. If you can't see any lamination lines it's probably monosteel, though on old rusty steel like that knife it can be hard to tell. The easiest way to check is to try sharpening the kireha on a muddy water-stone like those reddish brown 1000 grit King brand ones that seem to be found so often in Japan as to be a tripping hazard, if it's laminated you'll see a contrast between the soft steel of the jigane and the hard steel of the hagane. Traditional asymmetrical Japanese type kitchen knives like the one pictured are ni mai or two layer laminated, which is very rare on nihonto for obvious reason. San mai and warikomi are common to both kitchen knives and swords. Kobuse is also a form of lamination, and essentially warikomi in reverse, and is exclusive to swords. Here's a good set of diagrams for sword lamination types: http://www.ksky.ne.jp/~sumie99/construction.html
-
Looking through various sources, one additional possibility is a very well used 付け包丁. Kamaboko knife. Wrapping might be a later addition to strengthen a damaged handle. Edited to add: This post on KKF has some examples of old style Japanese kitchen knives as depicted in woodblock prints for future reference https://www.kitchenknifeforums.com/threads/Japanese-web-info-list.55062/page-7#post-1080381
-
I'm not totally convinced it's a takohiki, for the following reasons: It's very thin, most of them I've seen are around 3mm at the spine. It's possible it was sharpened down, but I would expect to see more of the original width remaining at the neck in that case. You said the ura side was flat if I'm not mistaken, and takohiki, like yanagiba and other traditional type sashimi knives, have hollow grinds on the ura side more or less always (searching hamaguri grind will get you some examples). The wrapped handle is atypical, normally on kitchen knives you see ho wood with either a smooth buffalo horn or metal ferrule, or plastic on postwar Showa period and later knives. In illustrations and prints from the Edo to Taisho periods I've kitchen knives with a very short section of wrapping, but only a few rows max. The reason for the preference for smooth handles is clear if you imagine trying to get fish slime out of the wrapping. Is it laminated or monosteel? Usually sashimi knives are nimai laminated. All of that said, it could very well simply be an atypical example of a takohiki, these things do vary.
-
In support of the differential heating theory, I've actually seen it appear accidentally on non-sword cutting tools before, apparently in that way. Why would it be done that way? It might have originated as a byproduct of smiths very carefully watching the edge temperature to prevent grain growth from overheating and excess soak time, which would reduce toughness, in the same way that fine grained nioi hamon were considered tougher than nie. No need to risk grain growth at the thin edge by waiting for the whole blade to come to temperature if you're only intending to harden part of it anyway. A cool looking result is discovered in polishing and then it becomes a desired feature swordsmiths work to optimize. Another just-so-story but it seems as likely as any.
-
Holding a blade, or indeed any old and well used object, and speculating, imagining, where it has been and what it has done over its history is of course part of the fun, and something I have done often, that said, unless proven otherwise it's all in our heads. For me, I am too immature as a sword enthusiast to say for certain whether I reside in either camp. I have found individual swords compelling in any number of ways, as art, as weapons, as curios or artifacts. I believe, however, that one shouldn't get these ways confused. A sword with no artistic merit will never gain it no matter how famous its past owners, the most beautiful hamon in the world does not make a broken sword cut better, and a gendaito will never be a "samurai sword" (as used colloquially) no matter how well made it was. I can happily evaluate swords as artifacts or art but not both at the same time.
-
The art vs artifact discussion is well trodden ground, and I wouldn't say that one side or another is correct, they're simply different perspectives. For the art collectors, who comprise the majority of this forum, patina, in the sense of wear, corrosion, and general out of polishness, are categorically negative because they interfere with viewing the characteristics of the sword. Even relatively light corrosion by most standards can totally prevent one from seeing hada and hataraki. Regarding provenance, I suspect that for most it's less a lack of interest and more that very few of these stories but the most famous are provable, to put it gently, so they may as well be discarded and the blades allowed to speak for themselves. The historian has some potential advantages, however, as he might be, for example, as an Edo freak far more interested in a generic Shinto wakizashi, or as a Sengoku enthusiast, in a Bizen kazuuchimono or basic yari, each of which is more representative of its era, than a grand old tachi of greater artistic merit, saving him quite a bit of money. The Heian otaku is out of luck though.
-
That kind of scratch pattern is far too coarse for hazuya or jizuya, more like arato. You would be there for the rest of your life trying to grind through pitting with uchigumori fingerstones. Presumably the previous owner went at it with a 1-300 grit green silicon carbide stone such as are quite common in Japan.
-
Not every mine (that seems to be the accepted term for many of these sites, as they were often extracted via tunnels or shafts rather than pit quarries) currently out of operation was shut due to exhaustion, many were simply encroached out of existence by expanding suburbs during the Showa era, as they were located quite close to Kyoto proper. Theoretically the stone could still be extracted, but it's not practical. On the other hand, a younger member of an old stone cutting family has recently begun mining Nakayama stones for the first time since the 1960s (if I remember correctly), so it's not all bad news.
-
If you're afraid that a blade in your care is actively rusting badly, a thick saturation of good quality gun oil is harmless, easy, and will stabilize it substantially by excluding oxygen. I gather that uchiko and a rag is uncontroversial for significantly out of polish blades. I've used it myself, it at least allows one to see the hamon somewhat, and while it may as others have described elsewhere harm a blade in good polish, I find it difficult to see how how anyone could meaningfully damage an already scratched or corroded blade with it.
-
For anyone who wants to try polishing blades and thinks it can't possibly be that difficult, there is an almost infinite supply of forlorn, rusty old yanagiba and deba for next to nothing on Yahoo Auctions Japan, with no value as anything other than tools and no risk of destroying an object of artistic merit. I think you'll find that even restoring a 20cm kitchen knife to a neat finish free of rust, with correct hamaguri geometry and crisp shinogi, and an even natural stone kasumi polish, is an art of its own, even though it pales in complexity compared to sword polishing.
-
Looked that up and I'm getting a lot of shogi related results, is that what you're referring to?
-
Age unknown, but it's definitely iron. It's possible it's on the older side, but I'm not experienced enough to say so with any confidence. 76mm wide, quite thin, maybe 2mm on average, chigaibishi or chigai kuginuki mon, patina is a little darker in person, pitting considerably heavier on reverse side.
-
From the pictures, drilling it out wouldn't be difficult at all. Center punch with a freshly sharpened punch, clamp it well, then drill it out in a drill press with a short stiff bit such as a center drill somewhat smaller than the pin diameter, which will be far less likely to flex and wander. After that, depending on how it looks, either step up the bit diameter until you've basically got a hollow thin walled tube, which will flex and crush rather than mark the ana, then pull it out from the backside, or just cut out the rivet head on the side you drilled with a countersink and drive it out gently. The first if the pin section of the rivet is deformed and bent, the second if it's straight. Don't try to drive a bent pin through a straight hole. I have unpinned many straight razors with this method, and the pin diameter on those is only 1/16" or about 1.5mm, so the amount of real estate you would be working with here is massive in comparison.
-