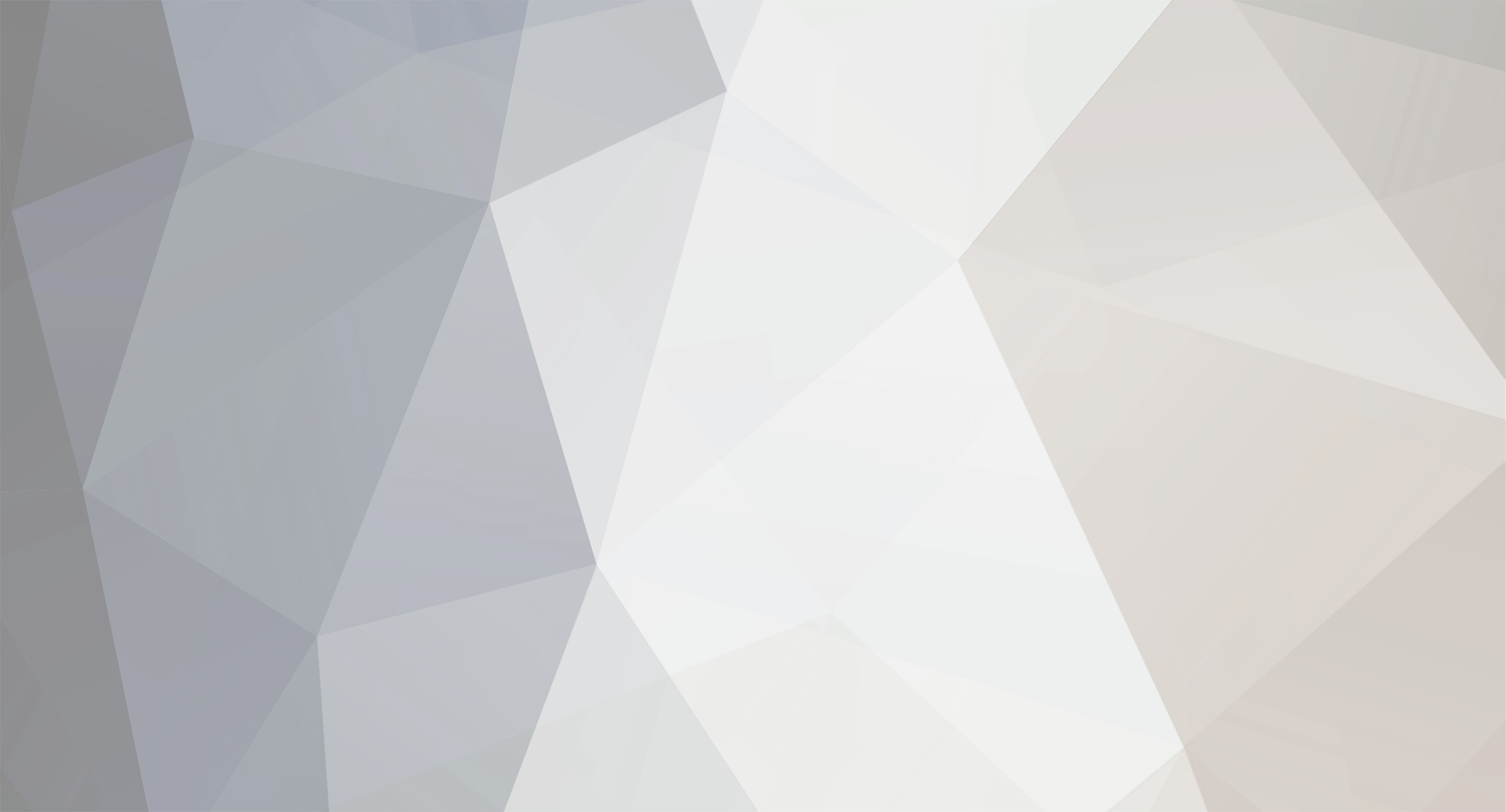
GregD
Members-
Posts
79 -
Joined
-
Last visited
Content Type
Profiles
Forums
Events
Store
Downloads
Gallery
Everything posted by GregD
-
-
Hada ,hamon,Showa stamp,non-traditional
-
Nugui is the process,Kanahada is made from the slag that comes off the sword as it is forged,ground into powder,mixed with oil and filter-pressed through washi paper onto the sword.The same is done with Ji-teko(naturally occurring loedstone or magnetite)and iron oxide.The visual results of what the "ji" will look like will depend on how well you filter any one or combination you may make.Another less aggressive kanahada(takes longer but will not "wash out" the grain boundaries that are brought out by the stones)is made by saving the residue that forms while using hazuya fingerstones.It gets rinsed off the blade,left to dry,mixed with oil and also pressed onto the sword through the filter paper as done with the others.
-
While I can agree with Brian about this not being a "How To" forum his final point about not using sandpaper is probably one of the most important and simplest reasons "why not?" The sandpaper and saya is a subject iv'e touched on a dozen times before and still got my testies bit off by people that insist they know what they are doing(they've used it a zillionn times before--on their Paul Chen)While carving wood isn't rocket science there still is a purpose for cutting inner surfaces in specific ways to contain the blade properly and to touch or not certain surfaces.All equiptment I use is for cutting or planeing to a finished flat or curved surface,no abrasives.Everything else(shop area)is vacuumed and working surfaces cleaned.I would like to think common sense kicks in while doing this kind of work to keep the sword safely stored while carving.While I dont do too much of this work anymore,I know that there are some very skilled people out there that are capable of doing this work,there are also some that cant turn a screwdriver and insist on polishing a sword with a Dremel. Greg
-
The assortment of tools I use,have added a few more tools since this picture was taken but I can pretty well get the job done with whats here.My favorites here are the namazori(small yariganna type tools)I like to use these at the habaki pocket and the clearance for the area at the kissaki.The one longer crankneck nomi was one of three that was made to order by a sayashi in Japan(he got the pick of the litter so to speak)its for max. material removal while the small radius planes are for smoothing out the pocket(i think its like cheating but they work great)I also have a Starrett surface plate for checking flatness. Greg http://i1095.photobucket.com/albums/i47 ... 0122-1.jpg
-
Fujiwara Kanenaga, anti-rust steel and "real hamon".
GregD replied to Bruno's topic in Military Swords of Japan
That all said........there is a reference in Fuller and Gregorys in reference to stainless steel :"They successfully this new steel called Taiseiko(or Fuseiko) for millitary sword making managing to bring out the hamon.I have seen two of these swords.Having a metal working background,alot of that having to do with heat treatment of steel,I can assure you that these blades were seletively heat treated.My only regret is not buying them when I had the oportunity. Greg -
Iv'e heard of a heat treatment where they take the bare blade to quench temperature,hold it horizontal,edge up,and pour water over it (without clay).Could be an example. Greg
-
Jim.....it all just starts out with a kanna,saya nomi etc,oh,by the way,you'll need more stuff to sharpen it with. Greg http://i1095.photobucket.com/albums/i47 ... 0122-1.jpg http://i1095.photobucket.com/albums/i47 ... na/607.jpg
-
As Grey stated,it looks like(and was )made in China yesterday and as such has nothing to do with Japanese swords.Anything else to do with this sword would be a waste of time and space on this forum. Greg
-
Im'e gonna go back to Daniels reply on this one,I have never seen a Nagamitsu in the '44 mounts with the metal saya lined with wood.Whats possibly missing on yours and the one on Ebay is a fabric wrap and the stippled laquer over it,(although I have a star stamped sword in these mounts that is just glossy laquered)I may have mentioned it earlier in this forum,aside from one "frankensword" Iv'e seen at a gunshow years ago with an oil quenched blade in it,most,if not all were plain tool steel. Greg
-
Help with ID and tell me about this sword
GregD replied to GunJam's topic in Military Swords of Japan
here is the steel plate the screw is threaded into,do not try to pry or drive the screw out,it unscrews.http://i1095.photobucket.com/albums/i47 ... G_0443.jpg Greg -
Traded for another Ishido Teruhide today,this is on the saya liner,most of it printed and some added in pen,top right is the date,the rest is kinda hard to make out.Just figured id'e toss it in the mix for either a refferance or as the brain teaser.Either way,if anyone can give more info it would be appreciated. Thanks GregD
-
These are generally two piece slab construction(althogh i have a couple of Takeda san -mai knives),but what you are missing is that where the welds are between the two slabs the material is removed(or physically upset whith a punch) to make this pattern rather than selectively heat treated like a sword. Here's something a little older. Greg
-
Tough one to call unless you have it in hand--that said,from the positions of the mekugi-ana,color of the sabe,looks done a long time ago.One thing to look for is remnants of the oridginal yasurime sometimes left on a portion of the end of the nakago(left intentionally as an indicator). Another thing ill'e take the opportunity to point out-in the second pic,where the mune-machi is ,notice the core as it enters the nakago(darker,or more easily oxidized lower carbon content steel vs the higher carbon steel brighter steel on the outsides)see if you can follow how far it goes into the nakago(might also indicate cobuse construction) Greg
-
Looks like a polisher did some"test areas"---kinda like putting in a window,determined the blade was just too flawed and felt it wasnt worth the effort.I think retempered,washed out hada,you can see it is there but blends too much when nagui was used,a partial attempt at "hadori",wont cover the ware which i believe were created when retempered. Greg
-
-
-
I think there is some confusion about terms and processes here.First off,as far as "NCO" swords are concerned they have nothing to do with "Gunto"(although not discussed in this topic i have seen the referrance to "NCO Gunto") I have only seen two "Showato" blades in NCO mounts,the rest being a lower carbon content steel probably not capable of being heat treated to produce a hamon to begin with,the half a dozen or so that i have worked on (rust removal) you could cut with a file.In the catagory"Gunto"you can find several blade types,first being a basic tool steel that i read a referance to being similar to A-2 tool steel,can be air or oil hardened but the referance i read was that they were air quenched.Any of these i worked on you could also cut with a file althogh this steel can acheave a hardness in the 60 c Rockwell range,and left softer to retain some toughness.These swords have chemically applied hamons. Althogh this is the most basic "Showato" blade I prefer to call them "plain toolsteel blades" and put them in there own catagory."Showato" on the other hand are in the range of blade that are between the "plain toolsteel blade" and Gendaito.the most basic being mill barstock being machined or ground to sword shaped then selectivly heat treated to produce a hardened edge(real hamon).Usually polished on machinery or hand to a certain level then chemically treated(warm cider vinegar) to etch and enhance the hamon, then contrast polished with chromium dioxide(the modern polishing compoung of the day) or a form of nugui.The rest are combinations of "forged and water quenched(selectively heat treated to produce hamon) but of non traditional material""forged and oil quenched(selectivly heat treated to produce hamon) but of non traditional steel" and mill bar stock (non traditional)that has been formed to sword shape then water quenched.Forging and heat treatment are two different processes,forging is used to physically manipulate structure or shape and size,"heat treatment" is used to change the properties of the material(hard or soft) That said ,Mr Bowen is absolutly correct in his statement "forging produces hada(grain),but never a hamon".Producing the "hamon" is an altogether seperate process(yaki-ire)the applicaton of clay to the blade in certain areas to act as a heat sink and a "mask"to make the sword cool at different rates when quenched producing a hardened edge area.Proper polishing of a sword helps enhance what is physically there. Greg
-
Gunto With Aluminum Scabbard. Opinions and translation help.
GregD replied to Randal's topic in Military Swords of Japan
This is the opening without the koguchi,definatly a metal sleeve.I examined it a few months back to see if could make a new liner for it,now after reassessing (and looking at the material it is made of)it may only go back a few inches.It looks like it is made of brass,as such,if it were the whole leghnth it would probably weigh as much as a steel saya. I oridginally thought the coloration was an "iridite" coating(a protective used on aluminum that is easy to chemically apply)And as far as refering to the finish as paint I sometimes generalize to simpify a statement.A few years back i found out how this "irushi" surface was produced after removing layers of black and red paint from a '44 pattern saya (similar or the same texture)---lets put it this way,I used laquer thinner and tricholrethane 1,1,1,(did test area first)it didnt harm the oridginal finish at all.When i enquired about it I was told it was probably irushi mixed with a filler material(wood pulp).That said-here are some pics of the rest of the sword. Greg -
Gunto With Aluminum Scabbard. Opinions and translation help.
GregD replied to Randal's topic in Military Swords of Japan
what it may have looked like.... The saya at the top aluminum,the rest are steel,notice the finish.The aluminum has more of a stippled finish,and is over a fabric wrap(prob.had trouble getting the paint to adhear to the alum.) Greg -
-
A new low in WW2 forgeries
GregD replied to jason_mazzy's topic in Auctions and Online Sales or Sellers
Ime gonna go part way with Mark here.I think more a utility knife than a "Kamikazie" dagger.And not stamped as a war trophy but a translation for export.Made By T.Sindoa(the rest i cant make out) Greg -