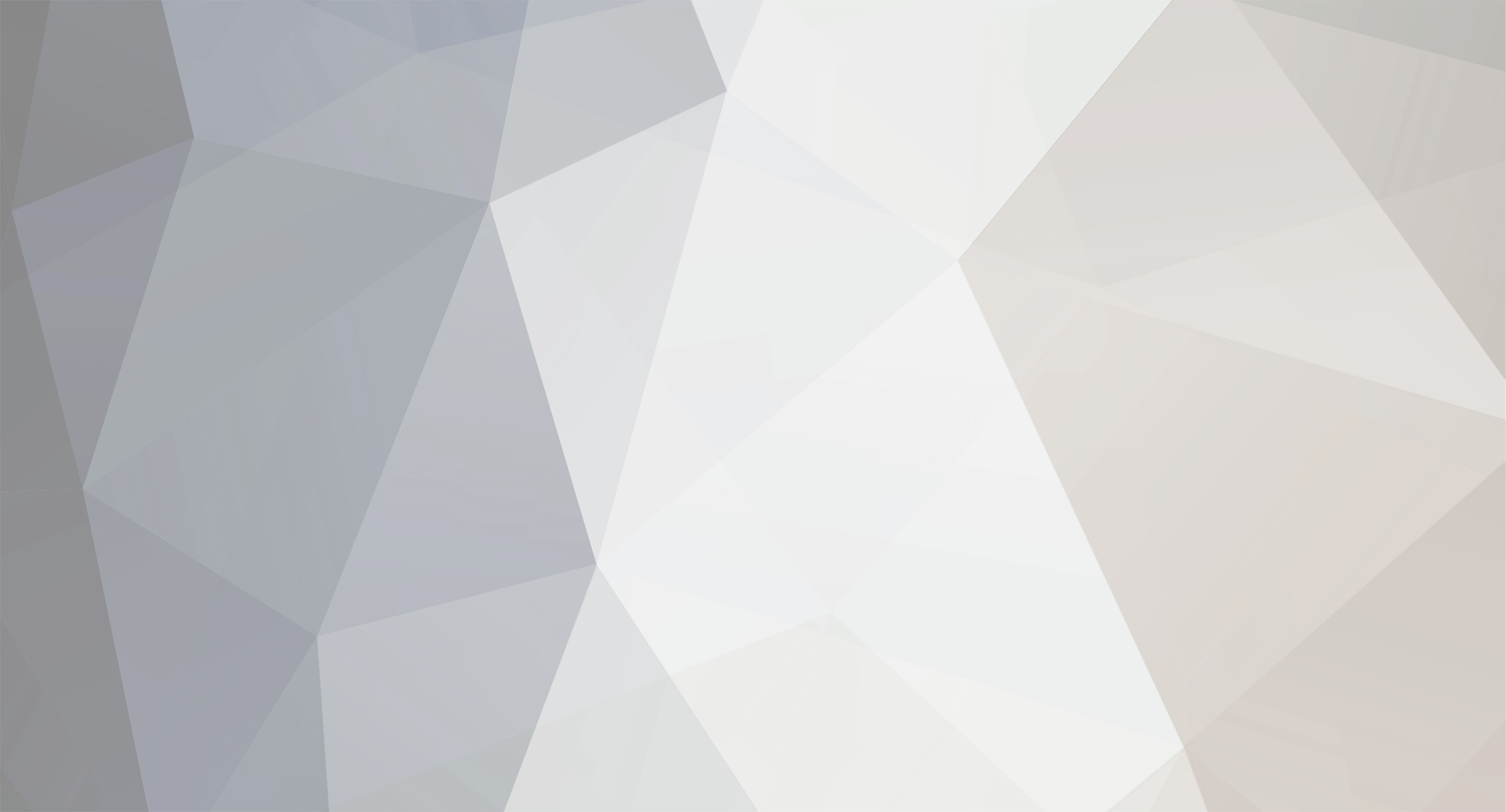
Kevin
Members-
Posts
295 -
Joined
-
Last visited
Everything posted by Kevin
-
wow. 3k + for a KOA ISSHIN MANTETSU on ebay
Kevin replied to drdata's topic in Auctions and Online Sales or Sellers
Interesting. :-) So did they aim for a smaller grain size than was normal for traditionally made blades? The eye versus the pyrometer? Do you have the names of any smiths whose swords failed? Oil quenched blades would suffer from the problems of contemporary homogenous steels. Sorry if I was teaching my grandmother to suck eggs, but not everyone who collects nihonto knows anything about metallurgy or the finer points of making blades. BTW just started getting a proper forge together again. :-) Got the kit to do small work, such as making my girlfriend a small pointing trowel, but missed having a forge for making blades. Kevin -
wow. 3k + for a KOA ISSHIN MANTETSU on ebay
Kevin replied to drdata's topic in Auctions and Online Sales or Sellers
Thought I'd have a go at making things clearer. There’s a good discussion on the effect of heat on grain size in this 1918 blacksmithing manual: http://www.lostcrafts.com/Farm/Blacksmithing-14.html Overheating a piece of simple carbon steel by as little as 100F/40C will coarsen the grain, as the following exercise shows. Take an old, large, good quality file and grind grooves across it, halfway through the file about one inch apart. Now heat one end to yellow while leaving the other end cold. This creates a temperature gradient across the file. There will be a definite "shadow" that goes across the bar. This is the area where the steel is transforming into austenite. Just to the hot side of that shadow is the correct critical temperature. Next, note which groove the shadow is at and quench the file in water. Having done that, put the file in a vice at the first, hottest, groove and break it off. A gentle tap with a hammer will be all it takes because the grain will be very coarse and weak. Have a look at the fracture - it will be coarse. Continue down the bar breaking bits off, noting how the grain gets finer and stronger as you move to the colder end. Pay special attention to the groove where the shadow was located and the one just above it. This will illustrate a temperature difference of about 100F/40C. Try to remember how subtle the colour difference was between those grooves. It is very, VERY difficult – though not impossible – to judge the right temperature by eye. With a bit of practice you might easily get to 122F/50C of the right temperature but that's still not good enough; if you’re over by more than 100F/40C the grain will start to coarsen, compared to the optimum. How much it coarsens depends on how much you're over temperature. You can turn good steel into junk by quenching from too high a temperature. Holding the blade at the critical temperature for too long prior to quenching will also promote grain growth. For simple steels the standard rule is five minutes per inch of thickness. You'd want to soak a 3/16" blade at temperature for about a minute. Soak it for too long (e.g. 90 seconds) and the grain size increases again. All in all, it isn’t surprising that some traditionally made swords failed due to cold temperature brittle fracture. What is surprising is that more didn’t – and that is an indication of the expertise of the smiths whose swords survived such conditions. Bear in mind that they were doing this all by eye and without modern instruments - it was a hell of an accomplishment. So back to the Koa Isshin - they'd have kept an eye on temperatures with a pyrometer rather than relying on colour. This would keep grain size to the the optimum, again reducing the chance of cold-induced brittle fracture. Mind you, that on its own wouldn't eliminate the risk. BTW, you have the same problem with ceramics - the difference between a good firing and a duff one can be 100C or less, particularly with some glazes. Kevin -
wow. 3k + for a KOA ISSHIN MANTETSU on ebay
Kevin replied to drdata's topic in Auctions and Online Sales or Sellers
@Chris It's not just down to homogenous versus heterogenous structure. I remarked in an earlier post that for a given carbon content, grain size – the size of the crystals in the crystalline structure rather than the hada – was also a factor. The crystalline structure can get coarser through the various forging operations if you’re not careful, especially during heat treating. The coarser it is, the more easily the piece will break, as in brittle fracture. The finer it is, the less susceptible it is to brittle fracture. Not surprisingly, susceptibility to cold temperature brittle fracture increases with grain size. OTOH suppress grain growth and you increase the resistance to cold fracture. Modern techniques of getting an ultrafine structure can increase cold fracture resistance seven times. However, these weren’t available in WW2. Now when you make a hamon, there is generally an increase in grain size, as well as a change in the crystalline structure from pearlite to martensite. If there wasn’t, you wouldn’t see the hamon. Increase it too much and the blade will be more susceptible to cold brittle fracture, despite being folded. OTOH, there are modern alloys that have ingredients to suppress grain growth. They’re useless for making a hamon, not because you can’t differentially harden them, but because the hamon would be invisible to the naked eye. They are however extremely tough and would be resistant to cold brittle fracture. However, that’s another technology that wasn’t available in WW2. Now we don’t have enough info on the traditional swords that broke. We don’t know if the failure was a whopping great chip that resulted in a fatal flaw, or whether the blade broke in half, though we do have accounts from feudal Japanese sources of blades breaking. We don’t even know the smiths involved, so we can’t research the details of the hamons involved. However, I’d bet my bottom dollar that grain size was involved, and that in turn depended upon the type of heat treatment involved. It is interesting to note that the Koa Isshin blades seem to have a very fine structure to the hamon which suggests that the heat treatment used kept grain size as small as possible. Kevin -
wow. 3k + for a KOA ISSHIN MANTETSU on ebay
Kevin replied to drdata's topic in Auctions and Online Sales or Sellers
BTW, if it is not too off-topic, visible grain is seen in early (i.e. pattern-welded) European swords: http://www.vikingsword.com/serpent.html Although the constructions can be almost as complex as the Japanese sword, the patterns are, to my eyes, rather clumsier. Mind you, they're achieved by twisting rods and then forge-welding them, rather than multiple folding followed by welding. The more folding you do, the finer the pattern gets. Fold it beyond a certain limit and the pattern pretty much becomes invisible to the naked eye. There's a brief and very basic resume here on various blade patterns from a variety of sword-making traditions: http://www.vikingsword.com/ethsword/patterns.html Kevin -
wow. 3k + for a KOA ISSHIN MANTETSU on ebay
Kevin replied to drdata's topic in Auctions and Online Sales or Sellers
@george I've had several pass through my hands, the last one a few weeks ago. There is a hada there, but it is very fine. Sometimes it needs a good polish to see it. Sometimes you might need a magnifying glass to see the details clearly. All the ones I've seen have been ko-itame. Kevin -
wow. 3k + for a KOA ISSHIN MANTETSU on ebay
Kevin replied to drdata's topic in Auctions and Online Sales or Sellers
@gab72 Well, I may get disagreements over this, but I'd regard it as a hada. A hada in a nihonto is a visible grain formed by folding metal. A Koa Isshin has a visible grain formed by folding metal - so what else do you call it? It certainly won't be a simulation though it may differ in appearance from that of a traditional nihonto. The alternative is arguing that it isn't a hada because it isn't a nihonto, despite the pattern being formed by folding and forge-welding steel. That seems too narrow an argument to me. It presupposes that only nihonto have hada and non-nihonto have something else, even though the visible grain in both cases is formed in an identical manner. All in all, it has been a fascinating subject to research. What I'd love to learn would be whether they laminated different high carbon steels in the skin steel, rather than just folding one piece of homogenous steel. However, the information isn't there to explore all the questions I'd like to ask. :? For example, the principal difficulty in doing folding and welding is making sure that any oxide scale is excluded. If it isn't, you get slag inclusions, blisters and open welds, which are seen in some nihonto. The usual modern method is to use borax as a flux (though the more aggressive fluorspar can also be used) and work from one end, so that the liquid flux and oxide gets squirted out by the hammer blows. I've no idea what the ancient smiths used (or if they used anything), or what the Mantetsu company used. :? Kevin -
Aleksey, what lighting were you using to photograph the blade? A mismatch between the lighting used and the film or, in the case of a digital camera, the colour temperature setting can cause a colour shift in a photo. Just wondered if that explained the difference between your description of the nakago and the photos. Kevin
-
wow. 3k + for a KOA ISSHIN MANTETSU on ebay
Kevin replied to drdata's topic in Auctions and Online Sales or Sellers
The carbon content of the shingane means that it is the equivalent of mild steel. The manganese figure for the shingane is interesting - it would increase the tensile strength of the steel for a given carbon content, plus increasing hardness and wear resistance. In this case the hardness would only be increased by a small amount, so the principal effect would be on tensile strength. Silicon also improves strength and hardness, though it is less effective than manganese. In short, damn all hardening on heat treatment but very tough. :-) Just what you want from a core steel. The carbon content of the kawagane gives it a good balance between ductility and strength when annealed, and has good wear resistance. It will also harden nicely. Kevin -
wow. 3k + for a KOA ISSHIN MANTETSU on ebay
Kevin replied to drdata's topic in Auctions and Online Sales or Sellers
Well, a high of Rc 72 on the edge and a low of Rc 50 on the back would be fine. It's what I'd expect from a good differentially hardened blade. However, the column is given as 'surface of an edge' in English - and what to make of his second column which, in the English translation, is described as 'reverse side of the edge'? BTW, did a bit of digging. If it is anything like modern steelmaking, the small rotary furnace produced the sponge iron from the ore. The process is used today and it produces very high purity iron with extremely low levels of elements such as phosphorous and sulphur, which in any case appear to have been at extremely low levels in Manchurian ore anyway. Steel was probably produced from the sponge iron by the aforementioned electric arc furnace - again, these two processes are used in conjunction today and give you steel with a very precisely controlled carbon content. All in all, it looks like Mantetsu were several decades ahead of the rest of the world. The next stage looks to have been forging a block of folded high carbon steel, then centre-drilling it to give a pipe. That's fairly standard technology for the time - it is how seamless pipe for bicycle frames used to be made. You wouldn’t want a pipe with a seam! They wouldn't have drilled the block entirely through, otherwise you'd have core steel coming out at the kissaki. Into this pipe you'd then put a forged and folded rod and weld the two together – to judge from the photos, using a power hammer. You'd then have to draw it down to the right dimensions, do some finishing work, and heat treat it by yaki-ire using water. That’s the best I can work it out from basic metallurgy and practical thinking. There are gaps in the accounts where I’d like to have more information, and some of the info is a bit garbled. However, you’d need experienced smiths to teach the workers how to fold and weld steel, and how to draw down. The principal difference between the hada of the Koa Isshin and traditional nihonto would therefore seem to lie in origin and function. In traditionally made swords the hada is a by-product of a process designed to make the steel homogenous. Ditto Swedish steel produced by the puddling and cementation process. However, with the Koa Isshin the steel would appear to have been homogenous when it came out of the arc furnace and was folded for the mechanical benefits of using folded steel i.e. achieving the requirement of reducing the likelihood of low temperature brittle fracture. The 1930s was pretty much the extremely early days of studying this phenomenon, and it wasn’t as understood then as it is now. In fact most of the work was done after WW2, especially by the US Navy, who were rather impressed by Liberty ships literally breaking in two, both at sea and in harbour. The problem was that if you have a homogenous steel and a brittle fracture crack starts, it can run, just as it does in glass – I’ve seen a paper of the period that described a 10 foot long crack in a ship as ‘little’. I suppose that it was when compared to one that broke the ship’s back and led to its complete loss. OTOH, if your material has heterogenous areas, the crack stops before it has really started – a bit like plywood. Kevin -
wow. 3k + for a KOA ISSHIN MANTETSU on ebay
Kevin replied to drdata's topic in Auctions and Online Sales or Sellers
Trouble is, Ohmura's data, as it stands, it pretty meaningless. Those are Rockwell C values. He gives a minimum hardness of Rc 50 and a maximum hardness of Rc 72. Now Rc 50 is not far above mild steel whilst Rc 72 is not far from the maximum that you can get from carbon steel. If I had someone who couldn't harden steel within narrower limits than that, I'd sack them before the week was out (if not sooner), cos that is the difference between not doing heat treatment at all and a dead hard edge. I'd expect someone using a furnace to be 2 Rc points apart (e.g. Rc 56-58) on the finished blade. Even a blacksmith with a forge would do better than the figures given by Ohmura. My guess is that the fully annealed blade started off at Rc 50, and the edge hit Rc 72 after yaki-ire, though there are problems with that interpretation. Rc 72 is on a par with an old-fashioned straight razor. The low carbon core steel would get no harder than Rc 50. Interesting that they were using an electric arc furnace for making the iron and a rotary furnace for heat treatment. Quite advanced for the time. Kevin -
wow. 3k + for a KOA ISSHIN MANTETSU on ebay
Kevin replied to drdata's topic in Auctions and Online Sales or Sellers
Hi John :-) Well, yes it is - but I was thinking of the more conventional use of the term which covers adding other metals such as vanadium or whatever. :-) I wasn't, BTW, proposing that Koa Isshin used the complex process of folding seen in traditional nihonto making. That does not however mean that the steel wasn't folded. On the technical metallurgical papers that I've seen, folding plus very good heat treatment (in this case, yaki-ire) would have been the only option available at the time to avoid cold temperature brittle fracture in the severe Manchurian winters. This was, after all, one of their aims. Not surprisingly, given their connections to the Japanese Army in what was then Manchuoko. I still have a strong suspicion that they resurrected the cementation process. Might be wrong though, but it would fit. I suspect that the traditional swords that failed had a larger grain size than was optimal for sub-zero temperatures, despite being folded. No way of knowing though, but it would make sense. That's down to heat treatment. Kevin -
wow. 3k + for a KOA ISSHIN MANTETSU on ebay
Kevin replied to drdata's topic in Auctions and Online Sales or Sellers
Just checked the metallurgical info. Cold fracture in steel does not predate the widespread adoption of the Bessemer and open hearth furnaces. It didn't happen in steel produced by the cementation process i.e. baking pure iron with carbon for a week. This process necessitated extensive folding. Folding would stop the propagation of the brittle fracture cracks that lead to the failure of the whole structure. This information would have been known to the Japanese metallurgists of the time. The only other ways to get lower the T5 temperature (the temperature at which steel undergoes brittle fracture) for a given carbon content is to either alloy it, or to reduce the size of the grains. Now the Koa Isshin blade isn't alloy steel - it's straight carbon and iron. Keeping the grain size small is down to good heat treatment, but they were limited with the technology then available. That leaves them with only one option if they were to fulfil the design remit of making a sword that didn't suffer from cold fractures in the Manchurian winters. Fold the steel. It’s basic metallurgy. Given the technology and the materials, there would be no other option open to achieve that aim. It would be interesting to know is how they turned pure iron into steel. I don’t think it is recorded. Did they resurrect the cementation process? My gut feeling is that they may well have done. After all, they would have realised that the older process didn’t suffer from brittle fracture in extreme cold weather. BTW folding and welding steel isn’t a particularly demanding process. Forge-welding is part of any blacksmith’s skill set. It’s just a question of getting the temperature right, excluding air, and banging it. You could do it with power hammers and a semi-skilled workforce. After all, that was part of the cementation process, which was done on an industrial scale. It only becomes complicated in making a nihonto because they make complex structures. OTOH, drawing down takes a large amount of skill. It isn’t just whopping the red-hot steel with a hammer – it’s having a feel for the steel as a living thing that changes with each blow. Most folks make an utter mess of it first time they try it. Kevin -
wow. 3k + for a KOA ISSHIN MANTETSU on ebay
Kevin replied to drdata's topic in Auctions and Online Sales or Sellers
Hmm! I've done a lot of forging over the years (I started learning when I was 13), including drawing down and blademaking. I've never seen anything like a hada formed as a result of drawing down. Can't think why any form of stretching would give ko-itame - machine-stretched stuff just has lots of straight lines from the rollers, and that's nothing like a hada. They are surface structures rather than part of the steel and as such don't survive polishing. Now way I understand it is that they put a low carbon steel rod (the 'malleable iron' mentioned in Ohmura's article) in a high carbon steel pipe and forge-welded the two together ('performed mechanical junction'). The composite structure was then drawn down. The method was reinvented by American smiths, who refer to it as 'pipe welding'. Now firstly, it doesn't say that the special iron they made was only used for the core. The iron made by the electrolytic process was used for making swords, which implies the whole sword. So they started off with iron and used it to make steel with various carbon contents. How that was achieved isn't mentioned. Secondly, I don't see any reason why they shouldn't have used folding to make the pipe. American smiths do, usually because they are deliberately fusing different types of steel to make the pipe in order to produce a blade with specific properties. In the case of the Koa Isshin, this was quite probably part of the method of avoiding cold fractures in the extreme Manchurian winter, which after all was part of the design remit. A straight carbon steel blade (e.g. showato) would be likely to suffer from cold fractures, as the Japanese Army found out. Come to that, it was a problem with some traditionally made swords as well. Hell, cold fractures posed a problem for the North Atlantic convoys. It seems to have been a factor in the sinking of the Titanic as well. Again, given that Mantetsu went to a lot of trouble to design a very high performance sword as pretty much a prestige project, I can't see them skimping. Hell, to judge from Ohmura's remarks they seem to have modelled aspects of the design on the second gen Muramasa. Kevin -
The term 'mill steel gendaito' originated with Fuller and Gregory to describe a sword that was handmade using traditional methods, including water quenching, but which used mill steel (or more likely, old Meiji-period railway tracks made from Swedish steel produced by the puddling process) rather than tamahagane. Mill steel *can* be traditionally forged, and a sword can be made of mill steel using the traditional methods used for making nihonto. It doesn't make it a nihonto, but it isn't a machine-made blade either. I've got one myself - it is a bloody lethal cutter. Mind you, it's unusual - the smith was copying a Koto design. To be a nihonto, a sword has to be made of tamahagane, be made by traditional methods and be hardened using water and yaki-ire. If one of those stipulations is not met (i.e. tamahagane is not used) then it isn't a nihonto. That doesn't however mean that it isn't a very good sword or that it wasn't handmade using traditional methods. Kevin
-
wow. 3k + for a KOA ISSHIN MANTETSU on ebay
Kevin replied to drdata's topic in Auctions and Online Sales or Sellers
BTW, if anyone is really interested in the various steelmaking processes, there are some good articles on Wikipedia. For blister steel see 'Cementation process'. A number of the early processes have interesting oriental antecedents. The Chinese had puddling furnaces (chao lu, if I remember the name right) and blast furnaces by the Han Dynasty (202 BC-220 AD), plus a version of the cementation process. The Chinese were also making Wootz steel, having picked up the technology from India. There's some reading here, though it isn't exhaustive: http://en.wikipedia.org/wiki/History_of ... y_in_China I'm surprised that the Japanese didn't adopt the puddling furnace at least - tamahagane would have made very good feedstock for producing exceptionally pure iron. The cementation process would have then produced carbon steel with a controllable amount of carbon. However, there's no evidence that the Japanese operated anything but bloomeries, which is what the method of producing tamahagane is. Kevin -
wow. 3k + for a KOA ISSHIN MANTETSU on ebay
Kevin replied to drdata's topic in Auctions and Online Sales or Sellers
Umm! Probably not. The president of Mantetsu gave a speech on the subject announcing his company's intention to 'improve on the Japanese sword', i.e. to apply technology to the traditional way of making a sword in order to make a superior sword. It was a prestige project, if you like. Given the barrelloads of money that Mantetsu was making from all its other enterprises (25% of Japan’s tax revenues came from the company), it was one that they could indulge. Now to tackle drdata's comment, Swedish steel railway tracks from the 19th century have a sort of hada because they were made from iron from a puddling furnace that was then turned into blister steel by heating with carbon for a week or more. This gave billets with a very inconsistent carbon content. These had to be folded umpteen times to get a consistent carbon content. It’s a bit like mixing dough. The resulting billets were then forged to shape. The Meiji railway system used tracks made by this process. It was good blade steel – a higher carbon content than most traditionally made blades plus manganese (makes the blade tougher). In fact Swedish steel was sought after for making blades in Europe – it has extremely low level of nasties such as sulphur. However, puddling furnaces and blister steel were obsolete well before WW2. They were replaced first by the cheaper Bessemer process (1860’s onwards?), which makes steel, and then by open hearth furnaces. The open hearth furnace has in turn been replaced by basic oxygen and electric arc furnaces. As a result, the modern steels that the Japanese were making in WW2 didn't need folding - the carbon content was already consistent when it came out of the furnace. There would therefore have been no need for Mantetsu to fold a modern steel. It would have served no purpose. In addition, modern steels don’t have a hada-like inherent grain. You can temper it however you like, including yaki-ire – you will not produce a hada, because that is produced by folding. 19th century Swedish railway tracks only have a sort of hada because they were folded, many times, during their manufacture. Mantetsu could have turned the pure iron that they were making for swords into steel with a consistent carbon content with no need for any folding. Since there is a hada - and it is quite definitely a hada – it was achieved by intentionally folding the steel. Most likely this was done with power hammers rather than manually. However, you still needed smiths to teach the workers how to do this. This was in line with their idea of improving on the traditionally made sword. Kevin -
New sword from Ryujin - buyer's feedback
Kevin replied to Curgan's topic in Auctions and Online Sales or Sellers
Ah, thanks everyone for the kind comments. I try to do my best and I like doing what I do. I also like folks to be happy if they've bought something off me - it's not simply an exercise in making money. As for drinks - if someone comes round, we've got beers in the pantry and there's a good pub up the road. :-) Leastways, as long as they're not the one doing the driving. Be prepared, as you come through the door, to be the centre of attention of a demented and affectionate lurcher and our three-year old daughter. The lurcher will probably sound like the Hound of the Baskervilles when you knock - however,the greatest risk is being licked to death. Kevin -
Of course we can, and quite legally! Kevin
-
The menuki look to be rather worn gold coloured ones, indicating that they haven't been touched. My guess? Someone has cleaned all the various fittings back, then treated them with an instant silver plate solution, of the sort that you can buy at the hardware store. Such solutions work exceptionally well on copper and copper alloys. Works on iron too, as long as you deposit copper on it, which isn't too difficult. It would be possible to do the menuki as well; however even with the lightest touch it would probably leave some staining on the ito. Kevin
-
wow. 3k + for a KOA ISSHIN MANTETSU on ebay
Kevin replied to drdata's topic in Auctions and Online Sales or Sellers
Not quite. The Manchurian Railway Company came up with a method of making very pure iron specifically for making swords - nothing else. From this they then made high carbon steel and low carbon steel. The high carbon steel was made into a pipe, a low carbon steel rod fitted up the middle of the pipe, and the two forgewelded together and drawn down. Given that it has a hada, I presume that the metal for the pipe at least was folded. Some machinery was incolved. OTOH, the company had swordsmiths over to teach the workforce swordsmithing techniques, so presumably traditional techniques were also used. Oh, and the cutting edge comes out at approx Rc 72. Thinking of the Manchurian Railway Company as being purely a railway company and that the source of metal was therefore going to be railway tracks is well off the mark. They're probably best thought of as a quasi-governmental body. They built entire towns and model cities (including the infrastructure) that were in advance of anything in Japan, were into agriculture and agricultural research, mining, pottery, glass making, steelworks, chemical plants, flour mills, sugar plants, electrical generation and engineering of all sorts. They effectively ran Manchuria and contributed about 25% of Japan's tax income. Not too surprisingly, they also had major connections to the Tokyo government and the military. They were allowed to seize property and could easily stifle dissent. Incidentally, their aim was to improve on the Japanese sword by making the construction (i.e. placement of core steel) more consistent and also avoiding the cold fractures that other swords, including traditionally made swords, suffered from in Manchurian winters. Kevin -
For some reason or other the Japanese government decided to ban the carriage of cashew lacquer by just about every route, on the basis that it might be used by terrorists. The Cashew Lacquer Company, whose product it is, didn't do anything about the change in legislation because, quite frankly, they are not interested in developing a market for this product outside of Japan, and couldn't really care less if there is a market for it outside of Japan. Their domestic market is big enough for them as far as they are concerned. I emailed Hyper-cafe when the news hit, but they didn't seem overly concerned. If they've now run out, I doubt that they will be able to restock. The current situation doesn't just muck up things for people lacquering saya - it is also used by artists, restorers of Japanese instruments, custom fountain pen makers and so on. I'm still trying to find a way of getting hold of it. I really need to get hold of an official in the appropriate Japanese ministry and get chapter and verse on the current laws. :-/ I suspect persistence is going to be everything. We may however have to throw together our own route for getting hold of it. As for urushi and US law, as far as I understand it, you can't stock and sell urushi in the US, but people are allowed to purchase it for private use. There aren't many places that sell it outside Japan. We sell it though, and have shipped it to the US. Kevin
-
If he didn't study there, then the provenance is falsified. If the provenance, which was part of the sales description, is false, then it is an offence under the Trades Description Act. Kevin
-
There has been a large explosion at Fukishima 1 nuclear power plant, according to the BBC. Kevin
-
Looking for a WW2 shin gunto tsuka restoration service
Kevin replied to patrick7813's topic in Military Swords of Japan
Me - but I'm in the UK, which is a bit further away than Fred I'm afraid. Kevin -
You might be more oblique and enquire if the gentleman ever studied there. best wishes Kevin