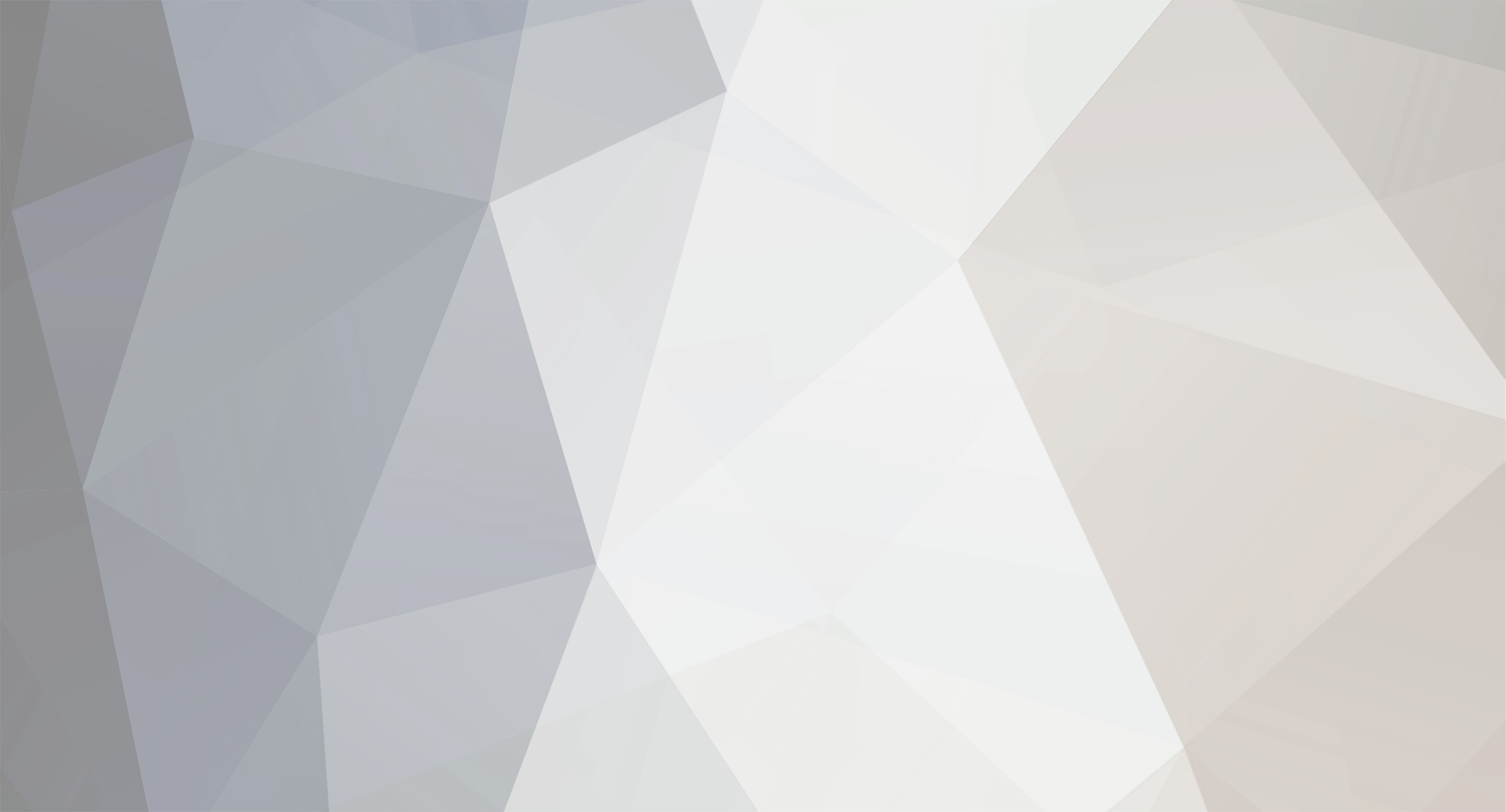
Kevin
Members-
Posts
295 -
Joined
-
Last visited
Everything posted by Kevin
-
I did my best to make it look good. :-) A sense of aesthetics went into it when I was designing and making the prototype. Even the varnish was handmade - though my girlfriend asked me to do it outside next time, due to the pong. :-) She had a point. :-) In any case, a well-made tool is a pleasure to work with. I've got a load of my grandfather's tools (mostly 1900-1920, but some of the planes go back much earlier), and they're a delight to handle and work with, in a way that a lot of modern tools aren't. I also like to take pride in my work. :-)
-
"Little pricey but looks really good!" I could do them cheaper, but then I'd have to make them all myself and that would have a knock-on effect on the rest of the business, not to mention home life, plus the lack of space to do more than 2-3 at a time. By the time you've figured in the time for the woodworking, wood finishing (and actually making the finish, which I did), and metalwork (and most people forget the cost of their own time if they're not making a living from it, £20-£30 an hour being what the average craftsman charges), cost of materials, cost of ancillaries, cost of packaging and so on, you find out that costs mount up. If you then get an engineer and a cabinet maker to do the work for you (leaving you free to do other essential business things), you then have to figure in their costs and still make a profit because unless you do so you're out of business, and no one has a tsukamaki-dai to purchase. You've also got to work on the basis that you'll probably only get 1-2 orders at a time because they're a highly specialised tool, so you can't assume that you'll benefit of economies of scale of getting orders for 5-10+ simultaneously, and thus you have to price accordingly. It's something that my wife met several times when she used to do the fairs. At one fair, in Masham, North Yorks, members of the local Women's Institute came round, looked at her stuff, and loudly and disparagingly proclaimed to all within hearing range that they could make the quilts that she'd spent days working on for less - and believe me, making and backing a large, double-bed sized quilt takes ages. Well yes, they could make it cheaper because they weren't trying to make a living at it, so they didn't have to figure in time and costs. Neither had they got up at ungodly o'clock to drive several hundred miles with stock (figure in the costs of van and petrol, and a couple of days of a room at the pub, plus the cost of the stall). I got a bit politely acerbic with them and they went away. :-) Said women then went round the rest of the fair upsetting all the other craftspeople with similar remarks (the guy who did pyrography was livid when we compared notes in the pub that night), and left without buying anything from anyone. You can only compare it with what people could do non-commercially - which isn't really a comparison for reasons given above - because no one else is offering one commercially. In actual fact when I was enquiring about sources for dai I constantly met the remark from companies that no one was making one because, having looked at it in the past, they concluded that it would be too expensive to sell, and no one would buy one. I imagine that they were visualising the eventual price as rather higher than this and having considered what they were thinking of, I concur. The postage costs alone would be prohibitive and the total cost would, I think, be the thick end of £1,000. I would however observe that, in the case of my dai, maybe 2-3 wrapping jobs would pay for it. The other alternative to making them cheaper would be to come up with a less durable design, and that I'm not going to do. I am hoping that these things last a tsukamaki-shi's working life, and several generations beyond that. If I'm lucky they may even become antiques. :-D I can hope that I've done my designing well enough for that to happen. :-D I like to take pride in my work. :-) I'm currently working on a modified clamp for tsukamaki. It will be a cheap one - £10 at the most. I'm hoping to make a more professional version for under £100, though that depends on how long making it and finishing it takes, plus cost of materials etc etc. I may when done have a look at seeing how much a tool-making company would charge to make limited runs, and whether it is worth it. Kevin
-
"Congratulations Kevin, very impressive and useful." Thanks. :-) I always wanted to offer one, but no one appeared to be doing any. Eventually I made some enquiries in Japan, and found that no one made them there either, leastways not for sale, and if I wanted to offer one I'd have to make it myself. Cue a few very late nights playing with bits of wood in the forge/workshop and at one point ponging the house out making the spar varnish with which to finish it (my partner had some pointed remarks about that). On further digging it seemed to be that tsukamaki was a rather neglected art. Togishi can get hold of the stones and equipment easily enough. Saya and tsuka makers can get hold of their tools and materials without too much trouble, as can lacquerers. By contrast, tsukamaki-shi can get hold of the ito easily enough, but the actual tools that they need? Until now they had to go searching round the net for the things that they could get - which invariably meant ordering from several different sites - and then go hunting for the plans for the things that they couldn't get, and either make them themselves or get someone else to make them. If they can find someone to make them that is. It took me two weeks of trudging round the local cabinet makers to find one who could and would make the dai, and even then finding him was due to a chance remark of mine to the guy in our local ironmongers who did the engraving. That’s also assuming that they don’t get bad advice from other sites. :-/ Anyway, this is part of an an effort on my part to put the situation right – my piddling contribution to trying to get folks involved in the arts of the Japanese sword so that there are future craftsmen and women. Along the way I’ve had a chat to a few tsukamaki-shi and asked “What do you want? What do you need?” The *principles* were based on Buck's traditional stand. However his design is big and couldn't go through the post except as a flat pack - and even then it would be too heavy. I also wasn't convinced of the sturdiness of a flat pack version. Additionally I'm not going to make the assumption that everyone has a workshop. Some may have to do it on the dining table, and put the dai away afterwards. So it needed to be smaller than Buck’s design (that way it also didn’t attract huge postal costs), but sturdy. I didn’t like the idea of an unbraced back plate. Having considered that, I didn’t like the empty space of just having a socket there – it looked like a waste - so the top bit of the socket evolved into a shelf that not only strengthened the braces, but provided useful storage space under it for the tsukamaki-shi, plus somewhere to put things out of the way on top of it whilst working. The bolts for the sashigane are more for stopping it coming out unexpectedly; actually it probably won’t even without the bolts, but I wanted to make sure that it couldn’t ever do that. I know – over-designing. :-) The idea of clamps came about from a consideration of the turning forces on the dai in use, and the principle was nicked from a table loom my wife has. The coach bolts are in case someone has a workroom, and wants it fixed permanently. Oh, since I was just this minute asked, it comes with the sashigane, the clamps, the coach bolt assemblies, and the bolt assemblies for the sashigane. Spare sashigane are available and if someone loses a clamp I can replace those. I don’t see any point in offering M8 coachbolt assemblies and M6 bolts, wingnuts and washers because you can get those down the ironmongers though if anyone has difficulties I’ll help out. If someone buggers one I’ll have a look at fixing it unless its obviously totalled. I don’t know how anyone would total one (or even damage one to the point that it needed repairing), short of setting about it with a lump hammer, but I long ago stopped underestimating people or the accidents that can happen. BTW I checked the prototype sashigane with a katana, wakizashi and tanto tsuka to make sure they’d fit. I figured it more efficient and cost effective for customers if I adjusted the dimensions so that one did all of them, rather than make several different sizes. Less bits to lose as well. :-) The next challenge is a tsukamaki clamp. I’ve been looking at some commercial clamps intended for other uses to see what could be usefully modified to serve as a tsukamaki clamp. Not everyone has lots of money. However at some point in the near future I’ll fire up the forge and bash out a prototype of a more professional clamp out of mild steel, hot black and card it if need be, and maybe put on some plastic grips such as you get on some pliers. Getting a tool company to reproduce the design may however be a problem; speciality tools are expensive and I’d rather keep the price down. It depends on quantities needed; it may be that I’ll just have to make them myself. I’ve been mentally designing it in my head (that’s where I design everything) and visualising going through the steps. “On an unrelated note since your hosting has changed alot of the valuable articles and resources from your old website are no longer available, will they be reactivated eventually?” I honestly don’t know. I had to go with a shop template because the latest sort of bells and whistles needed, such as being mobile compatible, were a bit beyond me. I’m not yet sure quite how to get non-selling, information only, things up there. I will no doubt find out eventually. In the meantime I’ve still got the files on my computer so if anyone wants anything I can email it to them. Kevin
-
No, it is mine. Nothing to do with Chris.
-
I don’t know if this is the right place, but here goes. As I recall, some fair while ago someone on here was looking for a tsukamaki stand. Unfortunately there were none available at the time, not even in Japan (I asked). You had to build your own. Well now there is one available. I’ve just spent the last 2-3 months researching, experimenting, designing, and woodworking to create a prototype, then getting the prototype to production. Not content with that, I observed that tsukamaki was a rather under-resourced art. People had to hunt all over the web for what was available, then hunt around for plans for what wasn’t in order to build it. This seemed a bit silly and incredibly time wasting to me so, so I asked a number of tsukamaki-shi what they used and what they needed, and have pulled a load of stuff together into one section. I haven’t quite finished yet. There’s a few other items needed, particularly clamps. I’ve had a look at a few commercial items but it mostly looks like I’ve got to fire up the forge and make a prototype. I’ll do what I can to keep the price down – it all depends on how long it takes to make, though I may be able to shorten the time with a jig for making the overall shape for the two halves. https://www.ryujinswords.com/tsukamaki
-
Last address I have, as of July 2012, is: ERIC ROUSH 348 COATES DR APTOS CA95003-4307 Kevin
-
Anyone know the type of construction use by the Akamatsu Taro e.g. kobuse? I've got someone asking, and I can't find the info anywhere. Kevin
-
False advertising for those that know
Kevin replied to cuttingedge59's topic in Auctions and Online Sales or Sellers
Hmm! I had some dealings with him years ago, when he first appeared. Nothing important - just a testing the waters thing. Very little happened his end for a long time except for lots of promises. I changed my mind, and asked him to return my items. I had a lot of difficulty in getting him to comply, until I got a US contact of mine to put some pressure on him. If need be, he would have had a personal visitation by someone acting on my behalf. All of a sudden, he was sending them back. :-) Now I've no idea if I can recreate that situation. It has been a long time. However, if I know details I can look into it. Alternatively, contact his local PD or, if the transactions cross state lines or are international, the FBI. Kevin -
Not as far as I know. However, he's the one best placed to answer that. I might drop him a line if he doesn't see this. Kevin
-
Thanks for the compliment Mariusz. :-) It's nice to find out that I've gathered a reputation. :-) All I've really done is to treat customers as I'd like to be treated. Selling swords - or anything for that matter - should wind up with the buyer feeling happy because he or she has got what they wanted at a reasonable price, and the seller happy that they've made a sale, made a bit of a profit, and that the customer is happy with their purchase. Such a simple thing, really, as well as being good business sense. Nobody ever made money long term by screwing folks over, and the idea of doing so doesn't sit right with me anyway; I've got to look in the mirror in the morning. I hate the idea of unhappy customers anyway. In fact quite a few become friends, and that's how I like it. :-) best wishes Kevin
-
Same goes for eBay in general. There's too many sharks in the field, and not just on eBay. You have to be aware, do research, and ask questions. If the photos are bad, don't buy, ever. However, I'm still on eBay, and you've bought from me in the past. :-) I don't think you were disappointed. :-) Kevin
-
Actually I'm a bit sad about this development. I remember years ago that Mike had a good reputation. If something was gimei in his opinion, he'd say so in his listing. If you asked him a question, you'd get an honest, informed opinion. Bought a few swords off him myself - he had a lot of genuine good stuff. Some of it went off to shinsa and came back with origami. Then he vanished for a long while. No idea what's happened. It's not what I expected of him. As I said, sad. Kevin
-
Umm! That's a bit garbled. There's a handling charge payable to Parcelforce for doing the Customs processing. It's Parcelforce that will be carrying it, and it is basically an admin charge. Customs will hold up the shipment for a while whilst they process it and decide how much tax you're going to have to pay. This can take 2 weeks, though they are usually quicker. You'll then get billed for the handling charge, VAT and any duties. Once those are paid, your stuff is released and delivered. And errm! I've got honoki round here, already imported. :-)
-
Don't know if this is the right area for this, but we now have a Facebook page where I periodically witter about things that we're doing, along with photos. http://www.facebook.com/Ryujinswords Kevin
-
Sounds like a good idea. I'll give it some thought. Kevin
-
We do a bamboo and rosewood version. A bit pricier. :-) Kevin
-
Hi Paul OK I stand corrected. :-) Kevin
-
PM sent. Agree with runagmc - get someone competent and reputable to do whatever work you need. Go and see them first. Look at stuff they've done, form your own opinion - ask for a second opinion if need be - and, if happy, discuss the job in detail so you're both agreed on what needs doing and roughly how much it is going to cost. You don't want any surprises in any department. In general, you're going to find very few businesses in the West - let alone in the UK - that can deal with every aspect of restoration, any more than you find many Westerners who are properly trained as swordsmiths in the Japanese tradition. With sword restoration you need several different craftsmen, not just one, so your odds of finding such a business go right down to just above hen's teeth level. OTOH, there's a few people out there who'll say "Sure, I can fix that!" and you'll find that the 'urushi repair' has been spray painted. We've had to do a number of repairs on 'repairs' for people. Now AFAIK we're the only business in the UK that can do anything from building koshirae from scratch, with urushi lacquer, to a good Japanese standard, repair koshirae (including repairing urushi), tsuka-maki, polishing etc etc all as one operation. Otherwise the poor old customer has to go out and find competent craftsmen for all of these jobs, get quotes from each and every one and, if necessary, co-ordinate the lot. Either that, or he's got to send the whole lot to Japan and pay more for a job that we can do just as well. Not entirely my opinion. :-) We had a Japanese guy here not long back - his family have some lovely, droolworthy swords and his kantei knowledge was excellent. Anyway, he was looking at every aspect our work, and he expressed astonishment that he could find work that good in the West, and all under one roof. We may get some work from him. :-) Right now we're restoring a couple of museum exhibits. One is a ginormous naginata - something like a 28"-29" blade, with a nakago about the same length. The other involves some urushi repair. I may post photos when done. :-) Kevin Ryujinswords.com
-
For future reference, we do horn slabs and fittings at ryujinswords.com, and we're in the UK. It's a bit quicker than getting them from the US. :-) Actually, we do pretty much everything. :-) As for the problem with one of the shirasaya - I'd have to look at it first, though there are solutions. However, the ability to solve problems, and the skill to do it is, however, is what folk pay us for. :-) Kevin
-
AFAIK the numbers are part of an internal IJA accounting system and not related to arsenal stamps. Kevin
-
That's why you get a new liner made. :-) Kevin
-
Umm! A different metal saya *may* fit - then again, it might not. Best you can say is that it might be possible. You've got three factors to consider: 1) the curvature (sori) of the saya versus the curvature of the sword 2) the widest dimension of the saya versus the widest dimension of the sword 3) length of sword versus that of the saya Now (2) and (3) might be OK - and are easily checked - which leaves you with the curvature. That's the one that often mucks things up. Get measurements. If the curvature of the sword differs from that of the saya, you're not going to change that of the saya by cold-working - it is going to have to be forge-worked. Can be done, but not many collectors or dealers do forge work. I do, but then I like beating bits of redhot metal into something different - it's relaxing and creative. :-) Not to mention it's a good way of keeping very fit. :-) BTW, if forge work is needed, you better make sure you've got a steel one. Don't know if this type is seen in aluminium saya, but I have seen ally saya for the earlier type. Additionally, don't aim for one that has a perfect paint job - the paint is going to get burnt off. Is it worth doing this? Yes, if you can't get a metal saya that fits and you're determined to have it in a metal saya. If you've got a metal saya that fits, the rest can easily be restored, including the paint. Done it for customers before. Though it will take a bit of digging around for the right paint. Spray paint won't do - you need the proper military enamel, and preferably one made to the same sort of specs as the original paint. And textured. You might need bits repatinated as well - or not as the case may be. Kevin
-
BTW markturner, I should point out that it isn't necessarily going for whatever the price is when you drop in on the auction, precisely because it is an auction. Right now, it's up to approx 1000 AUD. That doesn't mean that it will necessarily go cheap. Chances are that there are some folk waiting in the wings until the last few minutes - and possibly the last few seconds - to do some sniping. That invariably happens with Japanese swords - in fact you should count on it happening. Sensible folk don't bid at all until the last few seconds, because all bidding earlier does is put the price up. If you want it, it's best to just watch and see how things go. BTW, I have in the past picked up some nice swords on eBay, and made a tidy profit on them, when someone here has drawn my attention to a sword listing I liked by asking "is it genuine?" followed by "don't think I'll bid - eBay is full of sharks!" :D OTOH some listings just seem to get missed; hardly anyone bid on the papered ken I bought several years ago, so I got a really good deal. I'd get considerably more for it if I sold it, but it will never be for sale. Similarly some swords just go cheap because the right people didn't see it in time and the seller didn't put a reserve on it. It's not that long back that I picked up a papered Yasukunito in polish for $1000. Needless to say that it sold for rather more than that. :-) Sometimes that happens. The eBay price is not therefore an indication of it being genuine. The listing details and the photos are what you should base your decisions on. If there's not enough info, ask for more. If you don't get enough to satisfy you, don't bid or buy. Kevin
-
Well he's not described as a business seller, he hasn't got anything else listed at present, and the last car part he listed was sold last year, so he is probably selling his own sword, plus any odds and sods that he had around the garage and that he no longer needs or wants. Why don't you ask him? As for eBay generally, there's more than a few people here who sell stuff on eBay, either privately or as dealers. I'm one - look up ryujinswords on eBay. It doesn't take too much to ask folks here if an eBay seller is OK, or whether you should avoid touching them even with someone else's bargepole. Then again, the sharks aren't only found on eBay. I've also bought some very good swords and yari from eBay sources like this one. A few I've even kept, such as a Koto yari and a ken, because they were definitely keepers. My girlfriend got given the yari as a present. :-) The 'returns not accepted' issue - well, there's a difference between business and private sellers. Private sellers aren't bound by consumer protection legislation, so they don't have to accept returns. However, with a private seller you can still raise a dispute (e.g item not as described) which, if eBay found for you, would get your money returned. I've known of that happening with other privately sold items e.g. mobile phones. You could even do a chargeback. A private seller would then be daft not to accept returns, because that would leave you with their sword and them with no money. That's rather more protection than you'd get for buying something off another collector for cash. Finally genuine, as in a genuine Japanese sword? The nakago matches the papers and it looks kosher. Glancing through - and only glancing through - it looks like a nice blade. Personally I'd rather like a complete set of good shots of the blade - the listing only provides some shots of the blade. True, it was papered in the past - I'd rather like to see what the whole blade is like now, on both sides. However, you'd have to ask the seller for those - a reasonable seller will provide them. Mind you, a lot of folk aren't that good at taking photos of swords. I'm still trying to master it to the extent that I'd like. :-) Kevin