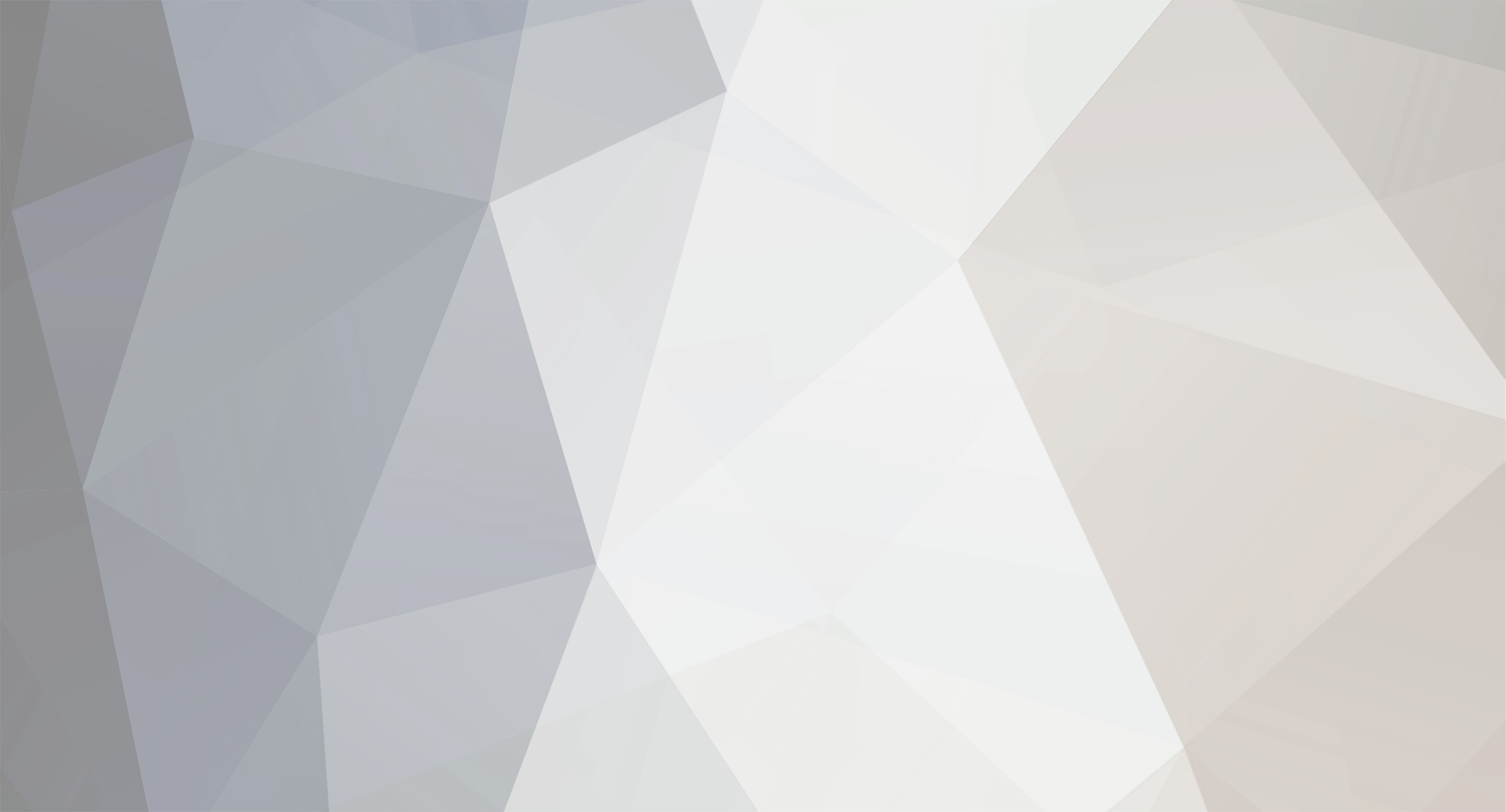
roger dundas
Members-
Posts
980 -
Joined
-
Last visited
-
Days Won
9
Content Type
Profiles
Forums
Events
Store
Downloads
Gallery
Everything posted by roger dundas
-
And thank you Peter and Colin. It would have been a reasonable enough piece in it's day but well past it's best in this condition . Just part of the unravelling history of such things that fascinate us. Roger j
-
Thank you Grev and Dale for your responses . Roger
-
This Tsuba was cheap back in early 2020 except the postage in the end made it less so and took forever to receive (from Japan) The reason for this post and for the purchase is that I saw what I believe was a somewhat similar small sized Tsuba (65.6 x 60.6 x 3.8) and stated to be Korean. I appreciate that many of the NMB tsuba collectors would not be interested in this but it has a place for me, especially if it might be from the time of Japan's invasion of Korea in the late 1500s. I realize that in this tsuba's construction, the maker had allowed the kozuka ana area of the tsuba plate to be expanded which is possibly more Japanese (?), on the other hand the nakago ana is rectangular in shape ( 3cm x .8) which might indicate Korean useage. I was hoping for your opinions please. Roger j
-
Once again, raising it's head- is it cast or is it formed, heated, sawn, hammered, chiseled, filed, poked and prodded into shape from a lump of iron, steel or other exotic metal. How easy is it to always be sure. I personally love the uncertainty of it all eventually leading to a certainty and an understanding. Thanks to all you very smart and knowledgeable contributors. Roger j
-
Glen, you had me wondering if I had made up the description "castellated" whereas "crenellated" was instead the correct word .On checking it appears either would do the job (I think). Enjoying the information about these sometimes enigmatic tsuba . Roger j
-
Glen, the last tsuba you have just shown above has what you probably noticed, in that the two dragons face a Christian orb surmounted by a cross rather than a "jewel". With gilded crosses at just above three o'clock and also just above 9 o'clock. This seems to occur with tsuba having castellated nakago-ana area. Piers pointed this out in a discussion early last year. Another point for Japanese manufacture ? I think I got that right ? Roger 2
-
It is good to see the name Ford Hallam once again including of course his contribution. Roger j
-
Sounds to me a great project Glen and would love to see the end result. It just is intriguing to see the amount of patient intricate work that goes into the making of some of these such as you show above. Maybe the mainland Chinese influence is a distraction for some but the overall amount of skill and time it must have taken (I don't see how it could be otherwise) is what is so impressive to me. Roger j
-
Ron, I used to be disconcerted when no one responded or commented on something I posted until it was pointed out that it could be because members themselves were unsure and might not want to take a stab/a guess. Sometimes putting forward your opinion works because members then have something to either correct or otherwise. Roger j
-
An outstanding conversation and dissection from my point of view. NMB at its best ? Roger j
-
Thanks Marco and Geraint. So that is how it was done, the carved piece that stood proud above the rest of the plate was inlaid (welded ?) onto the forged plate and then chiseled and shaped. That males sense if I read that correctly . Why I questioned the process was because some of the iron tsuba I have, display on one face just a small butterfly or a small rock or such like, raised above the surface of the plate. If the rest of the plate has been chiseled or filed away then that means a lot of work for not much effect. Are there any videos I wonder where a tsuba maker in iron is at work ? Roger j
-
I am a bit hesitant to respond here Marco because it is a question I have rather than a knowledgeable remark. I do like your tsuba. Am I a slow learner ? Because my question is about how the maker actually made the piece ? Does the maker start off with a mokko shaped plate about 6 or 7mm or so thick all over and then chisel away all of the metal except leaving remaining the shapes of the dragon in semi-relief from the background of say 4mm thick. If so, that is a lot of stock removal. The clouds and other surface marks are more readily achieved. Or is the tsuba initially cast and then worked on and chiseled to define and refine the final product. I have iron tsuba where I wonder if some of the iron elements standing in relief from the surface hadn't been later welded on and then finally shaped - or is that a ridiculous idea. I am well aware of the earlier extended discussion about cast as against straight out chiseled and shaped tsuba. But my mind still hasn't come to grips with precisely how some of these pieces were made. Made in the days before power tools, gas or electric torches or welders, nothing but hammers and chisels and saws and files of lesser quality than today. Be gentle with me please. Roger j
-
Spartancrest/ Dale said 'good luck in your collecting- no one ever stops at one'. So true. The addiction is a little akin to other readily available drugs like alcohol and nicotine. More fun and pleasurable though. Roger j
-
Tanto in Aikuch mounts-signed 'Hizen no Kuni Tadayoshi'
roger dundas replied to roger dundas's topic in Nihonto
Thanks Bruce and I always appreciate your comments, all of them. I think what has happened is we took pictures some couple of years back but didn't get around to posting them for some reason but found them stored away when we took this lot. I liked the thick blade too. Roger j -
Tanto in Aikuch mounts-signed 'Hizen no Kuni Tadayoshi'
roger dundas replied to roger dundas's topic in Nihonto
Thanks for responding Ray and as I thought. I presume it would be better to have no makers name at all, have it removed or leave as is ? From what I see here, countless nihonto, tosogu as well carry a gimei attributions and aren't removed . Again thank you. Roger j -
Have I posted this before ? If so I just don't recall any comments regarding the name which I quite honestly considered to be gimei/spurious when purchased in 2008. I once earlier had katana signed Tadayoshi with military leather covered civilian saya and was pretty pleased with myself until gently advised by my friend BaZZa that it was gimei. A bit deflating for the novice. The blade was what appealed, 21cm long, 1cm thick at its thickest at the habaki. I am unable to comment about the worthiness of the blade itself because I just wouldn't know. The simple shibuichi mounts and laquered saya are all in good order and that is also what appeals. I would welcome any comments and apologise if this is a reprise of an earlier posting. My wife who took the pics wondered if it isn't the early stage of memory collapse ? Roger j
-
So does it mean another few hundred years will need to pas before these 4 can again again be considered worthy of consideration ? And how best to store or handle them over this time or is there some alchemist out there who has some sort of formula to redeem this lot ? Just wondering Roger j
-
Now that is a good question and looking forward to the responses as well . Roger j
-
You are pretty amazing Dale with all these extra morsels you bring to the NMB table, forums. Well done and thank you. Roger 2
-
An intriguing insect but take care, the girls don't have the best reputation for the way they treat their closest friends. Roger j
-
Opinion on Momoyama ko-kinko tsuba of butterfly, plum and peony.
roger dundas replied to Ron STL's topic in Tosogu
Thanks Thomas/Iekatsu. Well that shoots down my proposition and clears up the method used for construction. Forgive me for saying but it still looks like repousse work to me although as you say these are a single plate so that cannot be. Thank you, Roger j -
Opinion on Momoyama ko-kinko tsuba of butterfly, plum and peony.
roger dundas replied to Ron STL's topic in Tosogu
I have been looking and thinking further about the above tsuba and would propose that they are formed from two worked plates attached back to back without the middle 'sandwich' copper middle plate found with san-mai tsuba.. Attached either by rivets (but I don't see any) or some sort of adhesive or solder which would date them after C1600 plus a fukurin for full security. Although the "Shibuichisword/Long tsuba site" states that similar plate designs were created by carving away the background (in a way like Michaelangelo did with his marble statues) just leaving the design itself in relief, the technique is called 'Sukidashi-Bori'- the metal carved away ; I would like to put my head above the parapet here and say that I think that once again it was instead done using repousse- the design punched and chiseled into the back of the plate, the plate turned over and refined with chisels from the face side and finished with nanako, gilding or whatever. I just think that a thin, relatively soft shakudo sheet wouldn't easily lend itself to such deep carving whereas repousse would be far easier and more manageable. Anyway, that is my take on it and I can claim to have some amateur experience with repousse work- not a huge lot but enough. If there is only the one plate with designs on either side then my proposal doesn't hold water. Roger j -
Opinion on Momoyama ko-kinko tsuba of butterfly, plum and peony.
roger dundas replied to Ron STL's topic in Tosogu
More semi-relief rather than high relief. If I keep trying I might get something right to-day. Roger j -
Opinion on Momoyama ko-kinko tsuba of butterfly, plum and peony.
roger dundas replied to Ron STL's topic in Tosogu
Yes Thomas, I just had another look . You are right and I was wrong to surmise San-mai. But the manner of work has that repousse worked, San-mai appearance to my way of thinking. It makes me wonder just how the high relief figures of butterflies and blossoms were worked up from the background ? They don't appear to have the edge sharpness that a chisel might produce ? Roger j -
Opinion on Momoyama ko-kinko tsuba of butterfly, plum and peony.
roger dundas replied to Ron STL's topic in Tosogu
It is really pleasing to see the well cared for condition of this old 'Momoyama (?)' period piece. Many, many of generations of previous owners have taken the trouble to keep the integrity of the relatively fragile surface design intact. So often these san mai tsuba show design distortion through use or some lack of care. Just my take on it. Roger j