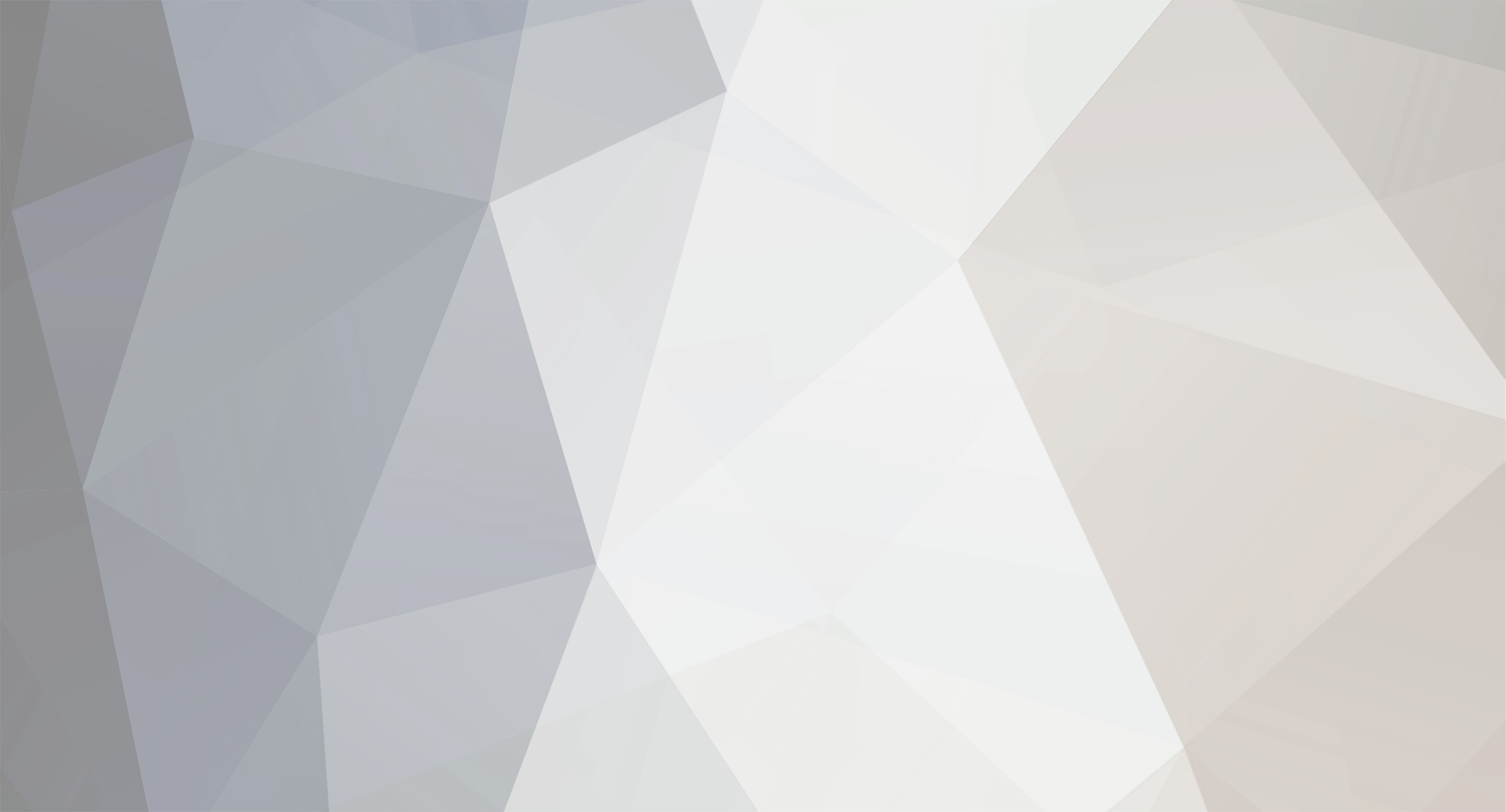
IanB
Members-
Posts
1,778 -
Joined
-
Last visited
-
Days Won
23
Content Type
Profiles
Forums
Events
Store
Downloads
Gallery
Everything posted by IanB
-
Jussi, Yes they are the ones. Useful to have on record. Ian Bottomley
-
This belongs to an armour I know but cannot remember where. Silver rabbits bouncing over waves on a leather ground - help senility setting in. Ian Bottomley.
-
I'm afraid my computer only shows location. Ian Bottomley
-
A big problem here is that there is very little to compare it with. The Royal Armouries in Leeds has only one item: a Mongol helmet bowl with silver overlay of shamanistic figures and tendrils so the decorative technique is OK. The usual source of information - Stone's Glossary' has failed to help. I will have a search in the Royal Armouries library next time I go into work but don't hold your breath. Ian Bottomley
-
It looks to me as if is really a backplate and the two embossed regions are for the shoulder-blades. The way the shoulder-straps are shaped also suggests this, since if it were a breastplate the fastening rings would be just behind the shoulders. I have to confess my initial reaction was that it was totally 'Mickey Mouse', but having really looked at it I am not too sure. If you look really carefully, there are key-fret decorations at the waist and around the arm holes, the rings are lap-welded and there are very distressed leather edgings. It may well be what the label says. Ian Bottomley.
-
As SAS says ( this use of cryptic identifiers drives me crazy - if you were talking to me face to face I hope you wouldn't hide your head in a bucket) the wakizashi would be worn and even that would be limited in size. In the 1680's the Tokugawa decreed the maximum length should be about 15". Bald head the Unworthy.
-
SAS, Yes, the swords for the Shogunal court had to be mounted in shakudo with absolutely plain shakudo tsuba and a horn kashira. I have a hilt with the fuchi in shakudo nanako, with mon also in shakudo and the obligatory horn kashira. I have a feeling I have the tsuba tucked away somewhere as well. The whole idea seems to have been not to present anything flashy when crawling towards the Shogun on one's knees. Ian Bottomley
-
Many years ago there was circulated a sheet of different wraps that a traditional tsukamakishi family published showing about 8 -10 wraps. One was described as 'senior samurai of the Shonai Han' another as 'lower class samurai of the Shonai Han'. This suggests some groups did have their own identifiable styles. I have a katana done two colours, buff and black, and I have seen other swords in this two colour combination. So I think the answer is at least a partial yes. Ian Bottomley
-
looking for Sugawa's book: the Japanese Matchlock
IanB replied to Chuck75's topic in Tanegashima / Teppo / Hinawajū
An fascinating read, but most interesting to me was the illustration of the three barrelled snaphaunce pistol then in Mexico. I had the privilege of handling it, or one very like it, in the hands of a US collector many years ago. It had probably arrived in Mexico with the Keicho mission to Europe undertaken by Hasekura Tsunenaga who was shipped across the Pacific, with other Japanese in a ship built by Will Adams and Mukai Shogen, Ieyasu's Admiral. Hasekra then travelled on a ship of the 'plate-fleet' to Spain whilst the other Japanese, one of whom was a bullion dealer, traded in silver with the Spanish in Mexico before returning to Japan. We know from a letter sent by Date Masamune of Sendai in response to an accusation by Tokugawa Hidetada, that the Tokugawa had supplied the gifts of armour and weapons for the mission to Europe and the snaphaunce I saw had defaced Tokugawa kamon on the barrels near the breeches as well as later Buddhist Deities in zogan higher up the barrels. The mechanism for ignition was clearly inadequate, as two of the 'steels' against which the flint struck had been replaced by bronze copies of the one remaining original. They took the form of L shaped pieces attached to spiral brass springs fastened at the rear of each pan. My memory is a bit woolly on exactly how these were supposed to work. I think they had a small stud at the bottom of the striking face that hooked into a hole in the flash guard at the front of the pan. When hit by the flint, the cover and steel was pushed rearward, unhooking the stud and allowing the spring to lift the steel and pan cover clear of the pan. Clearly it never really worked, and certainly wouldn't with bronze 'steels', but it was obviously considered a suitable gift to present to the Mexican authorities. Ian Bottomley -
Ciro, No, it isn't twisted strands and it is not soldered on, it is a fukurin - a U section piece of metal fitted over the edge of the plate. They are usually mercury gilded copper which is a bit tricky to get done in our society, You can get it electroplated in gold but somehow the colour doesn't look right. If you can get it plated the right colour use copper, but brass will make a reasonable substitute. How to make it - cut a strip from the edge of a sheet of brass that is a bit longer than you need. Soften it by getting it red hot and plunging it into cold water, but be careful as it is all too easy to melt the brass. You now need to make a punch like a chisel, but rounded at the edge rather than being sharp. Because the brass is soft, the chisel doesn't need to be hard - iron will do. Use this to hammer a groove along the centre line of the brass strip, supporting it on a block of lead or the end-grain of a piece of wood to form the strip into a U section that fits reasonably closely over the edge of the mabezashi. It might need re-softening again at this stage. Now bend it around the mabezashi. As it bends around the curves, the strip will tend to open up so go gently, tapping it beck to the U section where it does and re-softening if needed. The secret is gentle tapping doing a bit at a time until it fits. Real fukurin are pinned at each end and there will be tiny holes in the mabezashi where the pins go through. It was also usual to leave rounded protrusions from the edge of the fukurin at these points to take the pin / rivet. You now have a rim that fits the mabezashi, but whose cross-section is a U with the edges the same thickness as the rest. You can now file the edges down to give a more rounded section. Using a sharpy, mark diagonal lines along the whole length and using a triangular needle file, cut along the marks to make grooves. Don't file too deep and cut through. Finally use a file to round the surface between the grooves, then polish it all up. You can now fit it to the mabezashi, tapping it to close it so it grips the plate with a soft faced hammer. A fair amount of work but not too difficult if you take things slowly and gently, softening the brass if it gets springy through work hardening. If at first it doesn't work, chuck it away and have another go. Ian
-
Malcolm, The plural of forum is florums as any fool know! Have a great Crimble Buddy. Ian
-
Markus never fails to impress by his erudition. My knowledge of Japanese grammar, and the complexities of word order when read, is so minimal it could be written on the back of a stamp but somehow the sense seems to get through. Returning to the object in question, it is remarkable that Muneyasu would undertake such a minor commission as a kozuka. Perhaps Mr. Kawaji (or Kawamichi) was quite important. As I said, he was running what amounted to a 'finishing school' for armourers as well as turning out armours himself. The signatures on my armour are quite definite about Muneyasu being Yasukiyo's teacher yet the diary states the pupils were actually taught by a Munechika and the mask on my armour is an exact copy of two others I have seen signed by Munechika and are quite different from those signed by Muneyasu. So, it looks as if Muneyasu's workshop was a busy enterprise with quite a few involved in manufacture and teaching. Ian Bottomley
-
Uwe, According to Koop and Inada, 應需 can be read motome meaning to the special order of 川路君 - read as Mr.Kawamichi. Ian
-
Myochin Muneyasu was a Bakamatsu smith who ran a workshop / training centre in Edo. he published a diary in which he recorded some of his commissions as well as details of the pupils he took on. I am fortunate in having an armour by one such pupil, a Ki Yasukiyo, who stated on the dou, helmet, mask and kote that he was Muneyasu's pupil. From the diary I have calculated he was 19 when he travelled from Nagato to Edo where he stayed only three years so he must have been taught the basics in Nagato, being sent to Edo to learn the latest fashions. Ian Bottomley
-
Rokujuro, True we should us metallurgical analysis. As for the hardness of tekkotsu, I made the assumption on the basis that since they are proud of the surrounding surface they have worn less. and yes, the edges of tsuba do wear. I have one with arched edges which on one side are worn so thin as to be almost worn through. Ian
-
For years I have been banging on about the casting of sukashi tsuba and asking how they were produced when we know there were no piercing saws in Edo period Japan. Yes, you could chain-drill around the outline of every space and then chisel away the waste metal, but what a vast amount of work. The makers of these objects had to eat which meant turning out their products economically. No, these tsuba were carved in wood, with the solid parts somewhat over thick, a mould made and then cast. They then needed to be de-carburised by heating in a sealed container with iron oxide when the cast iron is converted to malleable iron that could then be cleaned up with scrapers and files. If as I suspect this was the process, the so-called 'bones' exhibited by some tsuba are simply regions where the de-carburisation was incomplete leaving harder pieces that wear less and end up raised above the surface. Ian Bottomley
-
Barry, The helmet you show is very odd. It is clear from the images that there are distinct gaps between the plates that would suggest a tatami kabuto but in fact the plates are fixed. I can only think that it may have been a tatami kabuto that has had the sections riveted to each other. There is one golden rule with regard to armour and that is there are no rules. So many items have passed from hand to hand, been modified, re-lacquered and generally changed to suit an owner's needs. Remember that all bushi had to own an armour, or be lent one if they were so poor as to be unable to acquire one for themselves. For many it didn't matter what it was as long as it filled the requirement. This would be especially true during the Edo period where they know they would never wear it in battle so a tatami kabuto that had been riveted solid would have been perfectly acceptable. Ian Bottomley.
-
Sorry but not a chance. I would suggest trying more oblique lighting. Ian Bottomley
-
Ciro, Well we can say a few things. First it definitely post dates the 1540's since the fukurin around the peak and fukigayeshi are roped in imitation of the edges of European armour. Almost all of the imported European armour seems to have been presented to Tokugawa Ieyasu who then passed some on to his followers, so it is a reasonable deduction it probably post dates 1600. It was a fashion that went out of favour later in the 17th century. Secondly the shaped edges to the plates of the shikoro are a definite indication the helmet in its present form originated in Kaga province We know from the work of Dr. Orikasa of the Armour Research Group that the Maeda only employed Haruta and odd independent armourers until 1800 so it is a safe bet it is probably Haruta work. The Maeda didn;t take over Kaga until the 1600's which corroborates the post 1600 date. The presence of fukurin on the suji and the igaki around the base of the bowl are a hang-over from the akodanari of the late Muromachi era which again suggests a 17th century date. So in summary I would say Haruta work from the 17th century. Ian Bottomley
-
Related to all of this is a case I became involved in (totally against my will I might add). It involved a shipment of Chinese made so-called 'samurai swords' impounded by the Customs at Dover. They were clearly marked 'Made in China', had the most appalling stamped out mounts, black painted saya and horrendous bindings, yet the shipper insisted the mixed metal blades were 'traditionally made'. What has caused all the problems is that our brilliant legislators failed to add the word 'Japanese' to the definition of 'traditionally made' . What swung it in the end and had the shipment stopped, appears to have been the fact that as I pointed out there were no 'Samurai' in China and hence they could not have been 'made in China as traditionally made for samurai'. Ian Bottomley
-
Artur, a beautiful job. I am just ready to start work on a similar hilt and I hope it comes out as good as yours. The worst part is untangling the silk from the skeins they are sent as. The darned stuff twists and knots up if you just look at it. Anyway, I will with luck start wrapping later today - after sorting out the last skein. Ian Bottomley
-
All, Try and get a copy of 'Firearm Blueing & Browning' by R.H. Angier. It contains hundreds of recipes for colouring iron / steel from brown to black. Curiously many contain copper salts as well as acids and acidic salts. The length and breadth of this problem is that what is needed is to initiate an even coating of rust which, being hydrophilic will then keep absorbing moisture from the atmosphere and build up the desired oxide layer. In all cases it is necessary to keep removing the loose red rust whilst the patina builds up underneath. The colour you get depends on the degree of hydration of the oxide layer. I have only had to deal with a tsuba that some kindly soul had 'cleaned' with acid. Although it is slightly pitted, I did manage to get a good russet colour on it and then after washing and drying, applied a coat of beeswax which filled up some of the pitting. All I do now with it is give it a polish with a woollen cloth from time to time and it looks reasonable - not good because it was too damaged but at least I can live with it.. Ian Bottomley
-
Andi, The approved conservation method to deal with lifting and flaking urushi is a solvent based adhesive called paraloid. However, the problem with it is that it hardens at the edges as the solvent evaporates and takes a long time to harden right through since the lacquer itself in impermeable. This stuff is used professionally since it is reversible, a requisite for all conservation techniques. Ian Bottomley