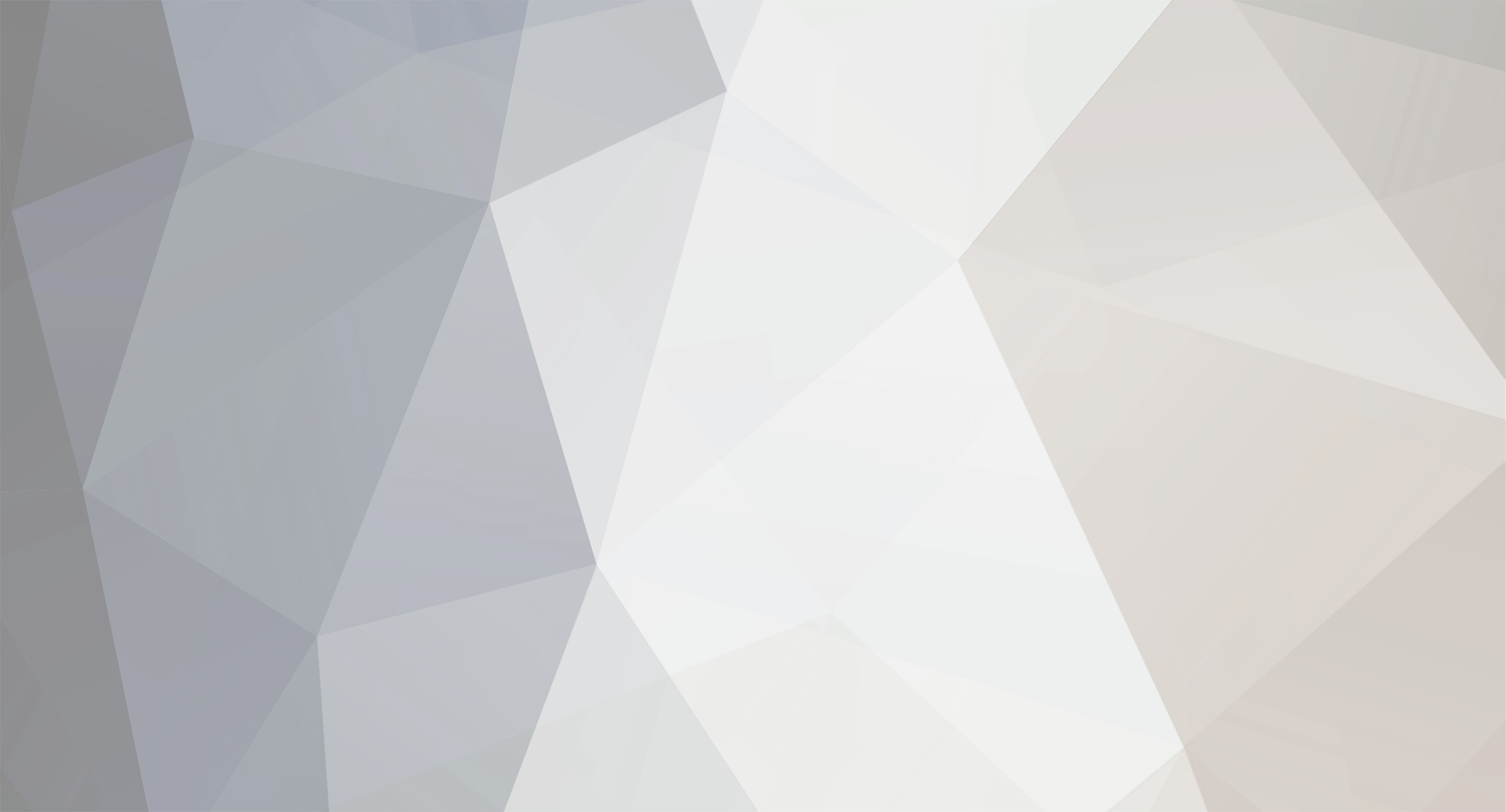
IanB
Members-
Posts
1,778 -
Joined
-
Last visited
-
Days Won
23
Content Type
Profiles
Forums
Events
Store
Downloads
Gallery
Everything posted by IanB
-
All, Like Ron I am sure this gun originally had a nipple of some form that had been broken off - a common enough occurrence since they were deliberately made very hard. The remaining hole is too large to be a vent and there would have been no point in creating the step if all the gun had was a simple matchlock pan in that position. The image that looks down from above the cock shows that the gunsmith has in fact off-set the ignition system to the right so that the original sights could still be used. I also note that the hammer has come to rest at about the correct height above the barrel to have struck the top of a nipple and rebounded slightly, a feature of good quality hammer shotguns that allowed the firing pin to retract back into the breech face and allow easier opening after firing. I suspect that what we are seeing is a matchlock that has been 'modernised' by conversion to percussion ignition by a very competent gunsmith that has subsequently been converted back by snapping off the nipple and cutting the groove in what had been the flat-face hammer. Had the supply of percussion caps dried up, it would have been the only way to make the gun usable again. Ian bottomley
-
Gwyn, Although Bill has closed his shop, he still attends the major arms fairs. He should be in Birmingham for the next fair there. Ian Bottomley
-
Honjo Masamune found!! (well almost... maybe)
IanB replied to Adrian S's topic in General Nihonto Related Discussion
Adrian, I too became involved with a TV show on this subject - an example of the current obsession by TV producers to produce progammes about 'Lost Treasures' (whether they are really lost or not - or ever really existed). I refused to be drawn into the Honjo Masamune debate and confined my contribution to bland generalizations and standing around holding a sword. I personally think you have hit the nail on the head twice in your posting. Tokugawa Iemasa was a prominent politician, and as you say, a 'Prince'. It is very unlikely that anyone in the American occupation forces would have ordered a person of such rank to hand over any swords in their possession. I have never seen or read anything about the situation with regard to the Imperial Household collection, but I assume it was quietly 'overlooked' out of deference to the Emperor. I am sure a similar attitude would have prevailed with a person of the standing of Tokugawa Iemasa. It is also most unlikely that Tokugawa Iemasa would have struggled to a police station with a bundle of 15 swords himself. If anything he would have informed the police and it is they who would have had to fetch them from him. Also, if it was his intention to 'set an example to others', he would have made sure the handing over would have been carried out with all of the publicity he could muster. Similarly, had the sword been reverentially spirited to some safe Japanese location like a monastery it would have re-emerged, again with maximum publicity, as soon as any potential threat to it had passed. It is difficult to know just what to think, but I am inclined to the view that the whole saga might be something of a myth. The blade was supposed to have had several chips it sustained at Kawanakajima. Were these polished out before the oshigata was done? It then seems to have been passed between everybody and his brother, including a relative of Toyotomi Hideyoshi, Hideyoshi himself (twice), Shimazu Yoshihiro and Tokugawa Ieyasu, before ending up with the Kii branch of the Tokugawa - not in fact the branch who were Shoguns. If it was a blade valued at 1000 mai, and supposedly the finest blade ever made, an awful lot of people seemed quite prepared to pass it on to others before it gained its revered status. Do I see the hands of the Hon'ami in here somewhere? Ian Bottomley -
-
In my previous post I said nothing about casting steel nor did I suggest that cast iron tsuba were left as such. I also made the point that there was no reason whatsoever why a tsuba should not be forged from bloomery iron and then shaped with chisels and scrapers into its final form. What I tried to point out is that the Chinese were definitely making malleable objects by removing carbon from cast iron and that if such a process were applied to the making of sukashi tsuba it would reduce the labour involved enormously. In ' Iron and Steel in Ancient China' Donald B. Wagner describes the decarburising process used in China in which the carbon content of the cast iron object is lowered by heating in an oxidising atmosphere. He also points out that hydrogen and steam would not be a factor in the pre-modern technique. He describes how the cast object was packed in closed pots with iron oxide (often haematite or iron scale) having a large percentage of Fe2O3. He also states that it is important to mix this with previously used packing material (which is largely Fe3O4) in the ration of 1: 3-5 to ensure the required reaction takes place at a rate that allows the carbon time to migrate from deeper layers within the object. From the degree of decarburisation of various Chinese artifacts that have been sectioned and analysed he concludes that the process, when carried out above 1000 C, converts a layer of 2 mm to ferrite and pearlite in about 1.2 days. Because the plate has two sides, some 4mm of the plate are converted to a tough but malleable steel by heating for just over a day. In addition the edges of the apertures will also be subject to the reaction and will loose carbon by exactly the same amount as the upper and lower surfaces. This is hardly a thin surface layer. I have absolutely no evidence that this was done in Japan and that tsuba were made in this way, but it makes a lot of sense that they were. What is incontrovertible is that the Chinese were doing it many centuries ago and that Japanese iron workers were fully aware of the process since they used it, and still do, for making traditional kettles. Ian Bottomley
-
Doug, Your question about the casting of tsuba is interesting and raises many questions. Clearly different types of tsuba involved different production techniques. We know exactly how many soft metal tsuba were made as Ford has filmed the process in detail, including the casting of a raw billet, hammering to thickness and inlaying large pieces of the base metal to achieve raised areas. When it comes to iron tsuba, we are talking a wholly different tradition. Early iron tsuba with a few simple piercing would almost certainly involve forging the basic plate, drilling holes where the piercing was to be and refining their shape with chisels, scrapers and possibly files, any texturing of the plate being done with punches. All very straight forward and using techniques we know the Japanese used. Problems arise when we extend these processes to more elaborate sukashi work. It is one thing chiseling out 3 or 4 shapes from a thin plate, but another when the design calls for a dozen or more openings, often with only thin divisions between them, in a plate of some thickness. I just pulled up an image of a Choshu tsuba by Yoshitsuke depicting Autumn grasses and there are there are 23 'holes' if the nakago ana and the two hitsu ana are included. Looking at it another way, this example is more hole than tsuba. Modern tsuba makers quite happily drill little holes and use a piercing saw to do a task like this, but nobody has ever demonstrated that such saws existed in the past. The nearest equivalent are the short narrow cuts in ito sukashi work. The fact that these cuts were the characteristic of the group's work suggests they were special and their makers were proud of being able to do them. Had it been a common technique used by most tsubashi making sukashi tsuba, they would have had no relevance. So we are back to drills and chisels and yes, the sukashi tsuba I mention above could have been made the that way but what a monumental task. Much simpler to carve it out of wood, with all the elements of the design left rather thick, make a simple two piece mould out of clay and make a basic shape in cast iron. The product would have flash and mould lines, but if a tsubashi can remove chisel marks with his scrapers, he can remove these as well - refining the over sized elements of the design in the process. This refining of the casting could be done to the iron as cast but it would be more sensible to decarburise the metal first - and that was a process that had been known for centuries. The Chinese were producing cast iron over 2000 years ago and were producing plates of the stuff that they then decarburised into a malleable metal. They made many of their tools by casting and decarburising them, so why shouldn't the Japanese? We know that the market is awash with cast tsuba, but many of these are cheap nasty copies made for the toursist trade in the 19th century. Why bother flattening off the seppadai or removing traces of flash and moulding marks when the buyers of these gems wouldn't know a real tsuba from a drain cover. There was a thread about a Soten tsuba a while ago where the faces of the samurai were blank flats. They were cast that way and lumps of copper or silver were normally soldered on later - how else could you retain the added face when there is no iron surrounding it to hold it in place? The Mantis Dude is correct in that Japanese craftsmen took immense pride in their work, but they were not going to go out of their way to make life harder for themselves, nor were they above using techniques that gave them a living. I have seen plenty of 'gold' inlay with the outer surface worn off revealing copper underneath. Why inlay a great blob of gold when you can cover a piece of shaped copper with gold foil and inlay that. No, I maintain many of these guys had a living to make and the more they sold the better they ate. I would remind you of the famous quote about putting the tsuba in a rice mortar, giving them a pounding, then choosing the ones that have not broken. How in the name of goodness is bashing forged plates with a wooden pestle going to break them? They might bend but not break. No, this is a way of detecting tsuba that have not been satisfactorily decarburised and are still essentially cast iron. Ian Bottomley
-
John, That doesn't look too bad. Good brushing and waxing will make that look ten times better. Nice quality mail by the way. Ian Bottomley
-
Jean, I am certainly unqualified to comment on the blade itself, but the tagane makura looks rather too obvious for a blade purporting to be Muromachi. Ian Bottomley
-
Grey, I'm sure that would work provided care was taken to avoid the stitches and fabric. The brocade used for so many armours is a weft based fabric having the most delicate warp threads so they don't interfere with the design. When these go, the weft just floats off as loose threads and there is very little you can do unless you are a skillful fabric conservator. As I have said, if the fabric is hemp, it is normally so tough you can be a bit more robust with it. Usually, provided the armour is kept in a dry place and it isn't that 'wet' looking rust it isn't going to get much worse. Better leave it well alone than cause more damage. Ian Bottomley
-
John, I really don't think you should take the metalwork off the iyeji - that involves taking off the lining to sewn the metalwork back and then the hassle of resewing the lining. Far simpler is obtain a short-haired stencil brush and gently brush off as much loose rust as you can, being careful not to break any stitching or rubbing the fabric - especially if it is silk (hemp is far more robust). Hold a piece of gauze or netting tightly down over the area and then use the smallest nozzle of a vacuum cleaner to suck off any residual rust. Finally using the same brush, apply an inert wax such as microcystalline wax to the mail, again being careful about the stitches and fabric. It should look a heck of a lot better and should inhibit any further rusting. Ian Bottomley
-
another good sword i found at an old antique shop
IanB replied to joe424's topic in General Nihonto Related Discussion
Joe, I am assuming that is your name - well done you on acquiring what may well turn out to be a reasonable sword. I detect from your posts your enthusiasm and the pleasure your new acquisition has given you. It is tragic that the blade has suffered abuse from some idiot in the past, but that is not the blade's fault. Have it looked at by a qualified polisher and take their advice on what can be done to repair or minimize the damage. Even if they cannot remove all of it, I'm sure it could be returned to a state that will give you even more pleasure, and more importantly allow you to learn from it. Ian Bottomley -
Mariusz, A museum about 30 miles from where I live acquired two collections made by local rich families who traveled to Japan in the 1880's and competed with each other as to who could acquire the finest pieces of lacquer, arms and ivories. Among the rather good collection of swords is what I decided when I examined it, was a mounted kodachi. It is probably 15 or 20 years since I handled it so please forgive the lack of details. This sword is about 90cm total length with a gold lacquered scabbard and silver mounts, the tsuka having stylised kenukigata. It would be easy to leap to the obvious hamamono conclusion except that everything about the sword gave me the impression of an extreme restrained and refined taste. I have a mental image of it having a sageo of violet deerskin and perhaps ho-o birds on the saya. I remember the blade struck me as having the proportions of a regular sword, except for a rather pronounced sori, whilst being diminutive. It might have been made for a boy, but in my opinion was far too refined. I came to the conclusion it was for wear at a court whilst wearing ceremonial robes. I'm sure I have read somewhere that such swords were worn because they would have been rather useless in an assassination attempt. Ian Bottomley
-
Brian, I would hazard a guess that the missing trigger-guard had the back end shaped with a hook that fitted into the elongated slot behind the trigger and hooked onto the brass inset. The front end would terminate in an oval plate to fit the recess in the woodwork with an extension on top with a hole for a retaining pin that went through the stock. So to fit it you would hook the back end in place and then push the front end into its location and fasten it with a pin. I believe it was not uncommon for good Kunitomo barrels to be sent off to be stocked in Sakai as the woodwork and brass mounts were considered better quality. Ian Bottomley
-
Randy, I hope you are making some progress. It failed to register with me that the kamon on the saya of your sword is accompanied by another in the form of a wheel. That second kamon was used by the Sakakibara family (and no doubt others). Sakakibara Yasumasa was of course one of Tokugawa Ieyasu's Shi Tenno. There is a famous portrait of him sat in front of his hata sashimono with the wheel kamon. He is wearing an armour with dragon and waves decoration done in lacquer. There is a similar cuirass in the Stibbert Museum with the same decoration but in russet iron which might be an alternative dou for the armour. The Royal Armouries owns an armour with a kirritsuke kozane dou and an akodanari kabuto of about the same era that has the same kamon but with the stub of the axle and a lynch pin depicted. I suspect this was a cadet branch of the family. Ian Bottomley
-
Dan C, Ron, When I was in harness, we did a number of x-rays on Indian gun barrels at teh Royal Armouries and they did just hammer a lump of metal into the breech end of their barrels. It was difficult to say whether they were actually welded or just hammered in hot so that the contraction on cooling gripped the plug. Many of their barrels were made by wrapping a strip spirally around a mandrel and welding it together. I used to have a part of one that had been badly welded and had 'unwound' during shooting. I bet that gave the bloke a fright. An early Portuguese book on gun making describes how the iron mandrel should be allowed to become rusty and to coat it with lime so the barrel does not become welded to it during the forging of the barrel. In Belgium (Liege) and in Birmingham, where the were making hand forged barrels into the 20th century, the strip wound around the barrel was shaped to a trapezoidal section so that when wound on the mandrel each turn overlapped the previous one to get a better weld. They also from time to time banged the end down on the anvil with the thing at welding heat causing the turns to weld together. Those guys used to create the strips from different steels that were twisted together in all manner of ways to give patterns in the finished barrel when etched. There is at least one barrel, illustrated by Greener the Birmingham gunmaker, that has the name 'Liege' worked into the patterning of the strip. Ian Bottomley
-
Randy, I wish you the best of luck on your quest. There are no end of books on kamon, almost all of which list hundreds of designs, carefully arranged by subject, but with no mention of who used them. Since there was no official body responsible for registering kamon, equivalent to the Colleges of Heralds in Europe, there is little hope of identifying the owners of most designs. Unless a kamon belongs to an existing family, or had belonged to an important family in the past, I'm afraid it is virtually impossible to identify it. There is also the problem that kamon were awarded to vassals for services rendered which leads to well known designs being propagated around the country and being used by families with no blood relationship with the original owner. A good source of information for the Sengoku Jidai is No 118 in the Gakken Series which deals with Samurai Warlords, another is 'Kamon no Jiten' (my copy is out on loan so I cannot give you the author or ISBN at the moment). Sorry to be so negative . Ian Bottomley
-
Paul, Delighted to hear you are on the mend. You are too valuable to have lying around in a bed. Ian Bottomley
-
Looking for places to visit in Japan
IanB replied to Chriso's topic in General Nihonto Related Discussion
Chris, Rather than Nikko, or perhaps in addition to it, I would include Kunozan Toshogu in Shizuoka. Whilst Nikko is a sumptuous Shrine, they only have the one armour of Tokugawa Ieyasu and his sword collection that was sadly all burned in a fire in the 19th century (although some have now been restored). In Kunozan are many of the Tokugawa family's armours on display, including Ieyasu's two gold lacquered ones, as well as much else. I would also add the Tokugawa Art Museum in Nagoya if for no other reason than their display of National Treasures and superb catalogues - especially the ones on 'Military Accessories of a Daimyo's Household' and the one on their sword collection . When I was there last there was a naginata on display that made you want to give up trying to collect, as well as the solid gold tea-ceremony outfit which I was told weights nearly a hundredweight! Ian Bottomley -
Anthony, Under the seppa it says 'two bodies' - futatsu do. Ian bottomley
-
GLASS IN THE HISTORY OF EARLY JAPAN
IanB replied to watsonmil's topic in General Nihonto Related Discussion
Ron, Some years ago I was invited to visit the excavations of Date Masamune's castle in Sendai. Although nothing remained of the main tower, the garden area survived and they had managed to deduce the original planting and had discovered some large pieces of Bohemian drinking glasses decorated with enamels. One had most of a mounted knight on it and the archaeologist had found an identical example in a German museum catalogue. Although nothing to do with the thread, it seems the size of the castle base was increased in the early Edo period and that the stones used were much smaller than the original and more or less conical with the bases forming the face of the wall. It was thought that the skill needed to handle massive polygonal stones had been lost and they had to rely on the makers of grave markers for the new stones. Ian Bottomley -
Dow, Please accept my apologies for not replying sooner, I had put your query on the back-burner and was subsequently distracted by decorating. I'm afraid to say I think your helmet is not all that old, although it is in an old style. A considerable number of these helmets, as well as complete armours, were made for the tourist trade in the Meiji period by redundant armourers who were desperate to make an income. The best can be very, very deceptive since they often incorporate genuine old elements. There is one in a large collection here in the UK that only really gives itself away because the sleeves, shinguards and haidate are all different despite being sewn onto the same sumptuous brocade. Invariably they took a few liberties, Westerners being far less knowledgeable than the samurai. Most obvious on most of these armours is the size and flatness of the lacquer on the scales - especially on the underside that often seems to have been given the minimum of attention. They also tended to use cast kanamono (ornaments) that often show a missed piece of flashing or repeat too often on the armour. Note the three triangular ones on your helmet. This trade in spurious armours and helmets continued into the Taisho period and quite a few seem to have been made for the coronation of Emperor Showa. Don't be down-hearted. I have a Meiji helmet I have associated with a real Muromachi do-maru. It is in the right style and quite a good copy and I ain't going to get a real one. Ian Bottomley
-
Woodblock print with matchlocks!
IanB replied to Viper6924's topic in Tanegashima / Teppo / Hinawajū
Eric, That print comes from the book illustrated by Utagawa Kuniyoshi. Whether such a shield was ever used I just don't know - I have never seen one. The Royal Armouries used to have a large standing shield, like a European pavaise, of heavy iron plates sugake laced together and fitted with a bar that locked it open and another that formed a prop at the back. Sadly I never saw it in the flesh nor indeed saw a photo of it because it was sold off in the 1960's or 1970's when the Museum had to raise money for an English great helm that had surfaced on the market. I know that Russell Robinson intended to relace it but couldn't find a supplier of braid big enough. It then passed through the hands of a dealer in London and I believe it finally came to rest in Texas. Where it is now I do not know, the collector / dealer in Texas who I think had it passed away fairly recently and the family didn't say anything about what happened to his collection. Ian -
Woodblock print with matchlocks!
IanB replied to Viper6924's topic in Tanegashima / Teppo / Hinawajū
All, There are several of these ladder back-sights illustrated in the Catalogue of the Tokugawa Art Museum 'Military Accessories of Daimyo's House' p.86. Two are shown that fit onto those back-sights having only a transverse hole through them rather than the T-slot. Two others appear to have a pair of uprights whose use is less obvious. Ian Bottomley -
Woodblock print with matchlocks!
IanB replied to Viper6924's topic in Tanegashima / Teppo / Hinawajū
I once made a long journey by rail and on foot to a museum that I had been told was holding a special exhibition on guns and gunnery. Cannot for the life of me remember where except that it was way out in the sticks in a brand new and very swishy building. When I arrived, it turned out that the exhibition was of about a dozen scrolls from various gunnery schools without a single hinawaju in sight. Linear meter after meter of scrolls done in cursive script, only one of which even had illustrations like this. Wandered round looking totally bemused then stalked off to get a bowl of noodles. Ian Bottomlet -
Malcolm. Not only did Louis Vuitton use stylised kamon as a design on his leather, he actually was inspired to make his luggage after seeing Japanese cartridge boxes at a Paris Exposition. Ian Bottomley