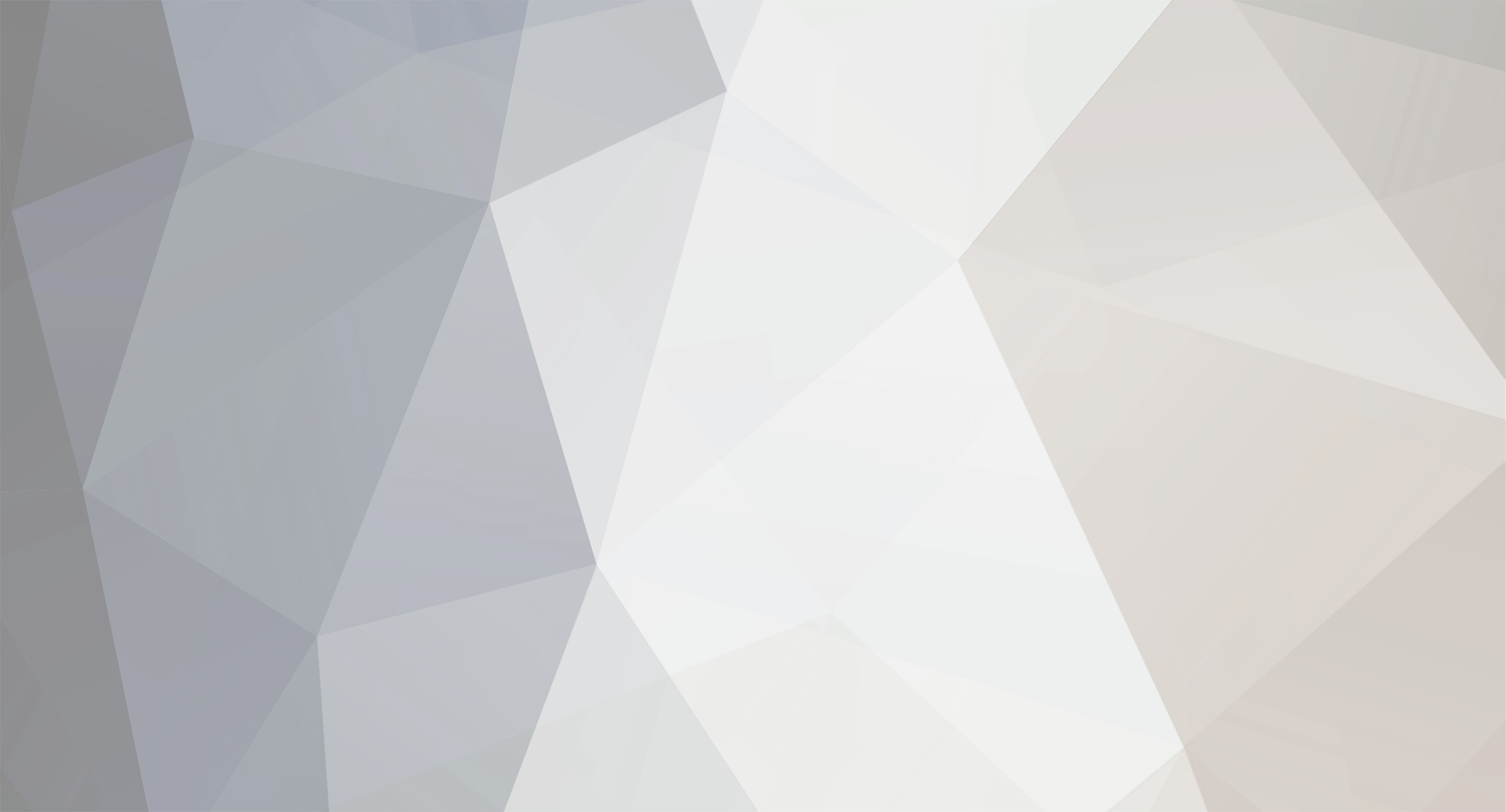
Ed Harbulak
Members-
Posts
189 -
Joined
-
Last visited
-
Days Won
2
Content Type
Profiles
Forums
Events
Store
Downloads
Gallery
Everything posted by Ed Harbulak
-
Gunto 1944 saya interchangable? (traditionally forged blade)
Ed Harbulak replied to Drago's topic in Nihonto
I used to own a Nagamitsu that pretty much had mounts that looked like yours. What was missing was NOT a metal covering for what you are calling the "wooden liner", but a leather combat cover that fit over the wooden saya. Since the blade originally had a leather combat cover, that also explains why the metal fitting from the bottom half of the saya are absent. Instead of looking for a metal scabbard, you should consider getting a leather combat cover made for the saya. Since many metals were becoming scarce toward the end of the war, many swords made late in the war had scabbards of a basic wooden saya with a leather combat cover. Good luck with your restoration project, Ed -
Celluloid Same of WWII...and Type 3 mon.
Ed Harbulak replied to george trotter's topic in Military Swords of Japan
Hi George and Bazza, I got to thinking about aluminum scabbards and possible seams. While I haven't notice a seam and it doesn't look like there is an obvious seam in my scabbard as the outside is quite smooth and I haven't looked inside, perhaps they used an extruded aluminum tube to make a seamless aluminum scabbard. In order to insure that paint would adhere properly to the aluminum, it would probably be neccessary to give the aluminum a special treatment prior to painting. That treatment might also have an effect on corrosion years later. There are many different alloys of aluminum and the various alloys can have rather different corrosion properties. Depending on the particular aluminum alloy used for building aircraft versus what might have been used for scabbards, the corrosive effects seen years later could be quite different. One would think the details of making not only aluminum but steel scabbards should be pretty well documented somewhere. They obviously did make these things, we just don't know the details. But then there's so much we don't know. Ed -
Celluloid Same of WWII...and Type 3 mon.
Ed Harbulak replied to george trotter's topic in Military Swords of Japan
This past weekend I examined an obviously machine made gunto by a Seki smith who signed Kanemune that has celluloid same. I happen to own a nice gendai by Nagamura Kiyonobu who is listed as having made medium grade gendaito and medium to high grade showato that also has celluloid same. My blade is very obviously a traditional forged blade and has an aluminum scabbard that I would presume would be rather uncommon. Based on these two examples, it would apper that celluloid same can be found on either the poorest quality gunto or on better quality gendaito. So what kind of same was used on a particular sword was probably either a matter of using what was available at a particular moment or perhaps the choice of the owner. We just don't have enough information so far to draw many conclusions. Just another mystery that needs solving and an interesting subject. Ed -
I enlarged the rather poor quality picture and it became even more obvious that it's Chinese, NOT Japanese no matter what they say it is. The handle wrapping is wrong and plus it looks like they used rather cheap cotton rather than silk ito. The fittings seem to be rather poor quality also and since 99% of what comes out of China in the way of so called Japanese swords, is fake, there's no reason to believe this is real. But, better to ask first rather than take a chance. Or, when in doubt, do without and save your money. Good luck. Ed Harbulak
-
While it would have been better if the blade and nakago had not been plated, the nakago is not ruined. The remaining plating can be removed either chemically and/or electrolytically leaving a bare nakago which can then be repatinated. I still see traces of copper plating which suggests to me that the original plating was in fact first copper, followed by nickel and finally chromium. Is it worth restoring the nakago? That's another question and will have to be answered by some future owner. In any case, all is not lost. Ed Harbulak
-
For $16,000 it isn't too hard to find a signed sword in perfect polish with NBTHK tokubetsu hozon papers. Just from a money standpoint, this Kanemoto, if indeed that's what it is, isn't any bargain considering the shortcommings that have been pointed out. It is a nice sword, just not worth the asking price. Ed Harbulak
-
If you have a copy of Slough's book, look on page 82 for a description of the stamp. It's the Tai stamp and appears on late war blades made by smiths associated with the Izumo Seiko steel works. Located In Shimane. The forge was located near the Izumo Taisha shrine and by 1945 the country was in dire need of divine assitance, hence the Tai or Dai stamp on some blades. The oshigata on page 82 is from a blade I used to own once upon a time but eventually sold to pay for another blade I had purchased. Congratulations on a nice blade. Ed Harbulak
-
Hi Joe, I have to disagree with Mark. while the mei is not clear, I'm quite sure it says "Echizen Ju Kinai Saku" and the subject is typical of the school. While I'm far from being knowledgeable about tsuba, I happen to own one that's very similar, which is what leads me to believe yours is from the same school and the mei is as I've indicated. There were several generations, and I don't know which one made yours, or mine for that matter. Ed Harbulak
-
Henry, The picture of the blade suggests it's a fine, well made sword, however I'd be concerned that the kanji for MASA is totally different from the way it's written in a genuine mei. That may explain why none of the previous owners have bothered to get it papered. Or, perhaps they tried to get it papered but it failed shinsa. On the other hand, if indeed it is a fine, well made blade, then even if it's gimei, it's still a well made blade and the gimei can be removed and perhaps putting the mumei blade through shinsa will reveal who might have actually made it. Ed Harbulak
-
Token Konno has a DVD on Japanese Sword Polishing that sells for $60 or at least that's the price listed on the flier I picked up at the 2006 Tampa Sword Show. Try http://www.tokenkonnoart.com. Konno san also is a sword polisher and shows up at the U.S. sword shows. I've seen the older VCR verson of this DVD and it presents an excellent overview of just what is involved in properly polishing a Japanese blade. Ed
-
I have a flawlessly made tanto and also a flawlessly made wak, both are shinshinto. They both easily passed shinsa and were attributed to higher ranking smiths. The tanto was attributed to Koretoshi (who was the second generation Tsunatoshi) while the wak was attributed to the 8th generation Owari Nobutaka. There are many reasons for a blade to be mumei and swords should be judged on the quality of their workmanship not whether they are signed or not. If nothing else, at least you don't have to worry about a mumei blade being gimei and if it's a flawless blade, the workmanship should enable you to decide if it's worth owning. We all get too hung up on swords with signatures, there are plenty of outstanding mumei blades, shinshinto and older out there. Ed Harbulak
-
Older nakago welded on a newer blade - how to recognise it?
Ed Harbulak replied to Marius's topic in Nihonto
I think we sometimes get overly concerned about the degree of rust on the nakago of a sword and if it was artifically produced or natural. I have a signed WWII gendaito made by Nobufusa that I was sure was a shinto era blade when I bought it a few years ago at a gun show. The nakago was so rusted that the mei was very difficult to read. The rest of the blade looked normal enough, with the usual staining and light rust often found on WWII era blades. I bought the sword thinking it was an older shinto blade in WWII mounts and was surprised to discover once I was able to read the mei that it was indeed a gendai with so much rust on the nakago that it looked far older than it was. Yet, I know who brough the sword back from the war and that all he did with it was hang it on his wall for display. I concluded that either the nakago had accidentally gotten wet in salt water and was never dried while the blade itself had been dried and or oiled, or the nakago had been handled by someone with sweaty hands that over the years caused an excessive amount of rusting. The sword itself had been surrendered on Okinawa at the end of the war and that's when and where the vet (US Army Air Force) received it. The moral of the story is that the degree of rust on a nakago can be very misleading and we should not try to read more into it than is really there. Not every rusty nakago is rusty because it was faked in order to make it look older. Sometimes rust just happens for any number or normal reasons. We all like pristine blades and nakagos, but the nakago was meant to eventurally get rusty. Sometimes the rust just forms faster than we would expect. Judge the blade, not the rust. As for welded tangs on blades, there is an extensive discussion on the subject in the back of the book, "The Japanese Sword", by Kanzan Sato. Read, read and read some more and try to remember what you read and learn from it. Ed Harbulak -
The mei reads "Bungo no Kami Yukihira" but there is no smith with the name of Yukihira and the title of Bungo no Kami listed in Hawley nor in the Shoshin listing of titles of Japanese sword smiths. That would seem to make the mei rather suspect unless there is an unlisted smith with that name and title. Ed Harbulak
-
The above attachement is from Gendai Toko Meikan and gives information about Okimitsu II, son of Okimitsu I. I have a star stamped blade by Okimitsu I and he was indeed a fine gendai sword smith. He learned to forge swords from Murakami Masatada who was a student of Kajiyama Yasutoku, one of the Yasukuni shrine smiths. To the best of my knowledge, the first generation Okimitsu used kiri yasurime with sujikai yasuri on the mune and ha edge. From the photos in Gendai Toko Meikan, it appears his son, Okimitsu II, used keso style yasuri. His son did help his father with sword forging during WWII and perhaps also made blades during that time period though he would have been a teen ager at the time if I'm not mistaken. Your $200 sword should look great in full polish and well worth the effort. Ed Harbualk
-
Hi Kevin, The signature certainly looks gimei to me, plus the tip of the nakago is wrong for this smith. The shape of the blade looks pretty decent, but the signgature isn't that of second generation Tadahiro by any means. Even the students of Tadahiro wrote a better looking mei than on this blade. A bad signature doesn't make it a bad blade, you just have to judge the blade on its own merits not the mei. Ed Harbulak
-
Hawley's lists some 20 Mino based smiths using the name Kanemoto from Koto through Shito times. Since the sanbonsuji hamon is so regular on this blade, if it's by Kanemoto at all it has to be one of the much later smiths using that name. Unfortunately many of those later smiths are not well documented, so finding examples of genuine mei from the later generations may be rather difficult. Then too, the blade could have been made by any number of Mino smiths working in the style of Kanemoto and either adding a gimei signature or leaving the blade mumei with some later sword dealer "improving" the blade by adding a false signature. Ed Harbulak
-
Sho-Shin.com lists 45 smiths with the Omi (no) Kami title. If you down load "Titles of Japanese Swordsmiths" from http://www.Sho-Shin.com you will have a handy reference for tracking down all the swordsmiths who had a title. Extremely handy when a blade is suriage and all that's left of the mei is the title. At least it greatly narrows the search for the possible smith. Ed Harbulak
-
Yasukuni Yasunori
Ed Harbulak replied to huntershooter's topic in Auctions and Online Sales or Sellers
Yasukuni blades are normally signed about the mekugi ana with a two character signature. According to the Yasukuni book, they are signed below the mekugi ana, generally as "Yasu sombody, respectfully made" when they were made for the Emperor to be given by him as gifts. I would guess these gifts were given to some officer graduating at the head of his class, for meritorius service, perhaps a major promotion in rank or something similar. I would also expect that a sword being given by the Emperor as a gift would have a lot more on the nakago than just the name of the smith and the date. So even without comparing the mei on this blade to a genuine mei, I'd want to do a lot more checking. The blade itself certainly looks a lot like what I'd expect a Yasukuni blade to look like, but when things get expensive there will always be fakes. Just my opinion and I could be totally wrong. It will be interesting to see how the bidding reflects other peoples' opinion. Ed Harbulak -
Last summer I went to the estate sale of a marine as it was advertised that there were some swords in his collection. It turned out that the three or four swords he had were all Chinese reproductions and priced accordingly. I assume he wasn't lucky enough to get a genuine Japanese sword while in the service (presumeably WWII in the Pacific) but never the less always wanted one. When the Chinese copies became available he apparently bought a couple to remind him of his days in the war and his relatives conducting the estate sale may have assumed he brought them back after the war. It just goes to prove that not all swords from the estates of WWII veterans are necessarily genuine. There were some other genuine WWII items at the estate sale, such as linked .50 cal. machine gun ammo with correct date stamps on the heads. So he was obviously somewhere in the Pacific, just didn't bring back any Japanese swords, or if he did, no longer had any at the time he died. Ed
-
Peter, As a general rule, the smiths of the Tadayoshi school wrote the "zen" character of Hi-zen with the small stroke to the right side of the right hand vertical stroke. The correct Japanese way to write "zen" is with that small stroke between the part of the "zen" character that looks like the character for moon and the right hand vertical stroke. Since the way "zen" is written in the mei on your blade is wrong for members of the Tadayoshi group, I'd have to say that the mei is gimei. That's not all that unusual, of course, when it comes to Japanese swords, so judge the blade on it's own merits, not on the signature. Ed
-
If the smith's name was Ikeda you might want to determine if the blade is a gendaito. Ikeda was the family name of the Yasukuni smith Yasumitsu. Before using the name Yasumitsu, he was the 10th generation Kazumitsu. Might be an interesting blade. See page 186 in Slough's book. Ed
-
Definitely gimei, or fake signature. In this case, the easiest way to tell it's a fake signature is the second character, the "zen" of Hi-zen. The Tadayoshi school wrote the "zen" character differently. The stroke in the lower middle center of the character is written properly, but the Tadayoshi school put that stroke on the outside right of the right hand verticle stroke. Find an authentic signature of any of the mainline Hizen smiths and you will see the difference at once. So much to learn and so little time, but keep learning. Ed
-
Just to further prove that there are exceptions to every rule, I have a gendai blade mounted in 1944 mounts that only has a single mekugi ana in the ubu nakago. The tsuka also has only one mekugi hole and never had a second. The blade is star stamped and dated Oct., 1944. Perhaps by the end of the war they were even trying to save on mekugi. Ed
-
For centuries, violins and other similar Western stringed insturments have been put together using hot hide glue. The top of a violin is fastened with diluted hot hide glue so that the top can be easily removed from time to time for repairs or other needs. I have used diluted commercial liquid hide glue to fasten the two halves of a newly made shirasaya together. It holds well enough to keep everything together, yet with a little pressure applied to the inside the shirasaya will split open for cleaning. While applying a bit of water to an opened rice glue joint on a shira saya should work, you can also try some diluted liquid hide glue. Work the glue, or just water into the split with a thin bladed spatula and tie firmly till dry. Ed
-
I use a paste wax (Simonize brand automibile wax) on all my shirasaya and have never had any problems. Since the objective of a shirasaya is to protect the sword as much from external moisture as well as physical harm, I don't know that breathability is all that important or even desirable, unless you are hoping any moisture inside the shirasaya will defuse out. Of course, the blade should not be wet when it goes into the shirasaya. One or perhaps two rather thin applications of a paste wax should be all you need to help keep the shirasaya from getting too dirty. Ed Harbulak